Bridging The Data Divide: How Egglife Foods Unified The Plant Floor With SafetyChain And Ignition
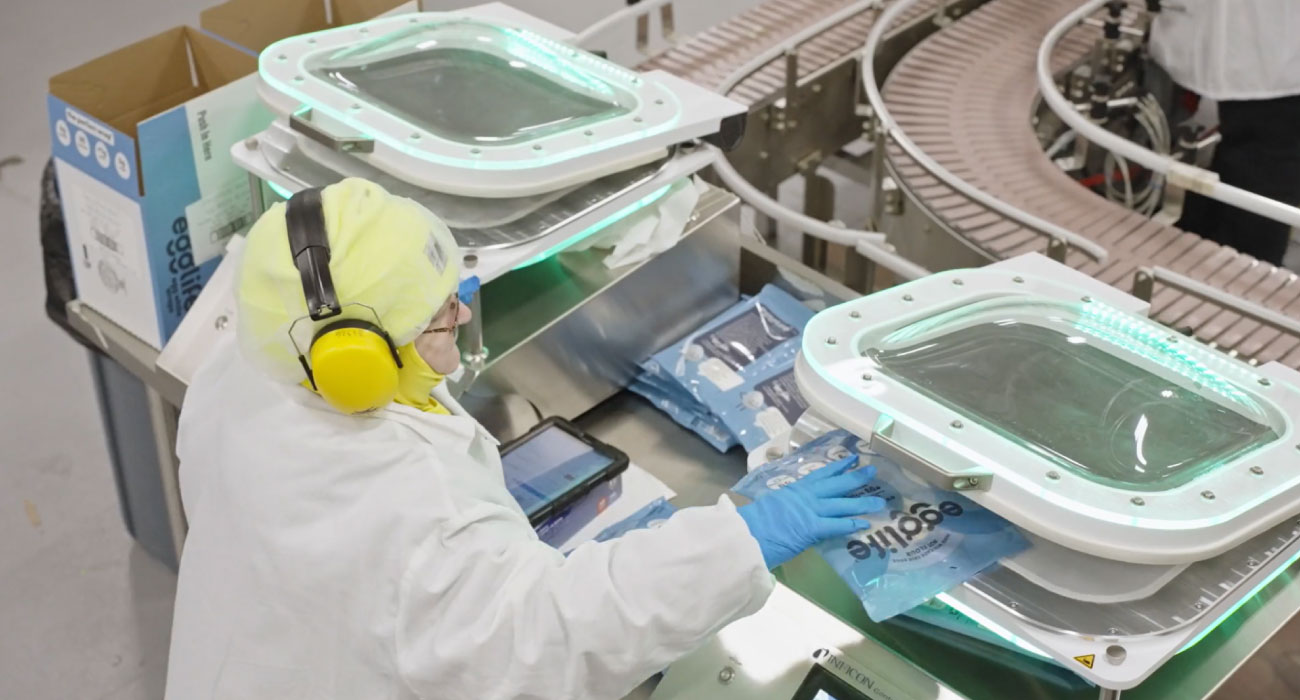
When producing a product consistently, every action impacts the next. However, that doesn’t always mean the manufacturing plant floor operates as a connected system. Delayed or incomplete information across the floor puts everyone, particularly operators, in a poor position to problem-solve and correct issues in real-time.
The disconnect between machine data and quality assurance is a common bottleneck that disrupts consistent production. Combining and contextualizing this data can inform an immediate understanding of where action is needed, laying the groundwork for automation.
Egglife Foods, Inc. is a great example of bridging the gap between quality and machine-level data. By partnering with SafetyChain and Inductive Automation, they’ve unified plant floor data and eliminated latency between data capture, actionable insights, and results. Egglife can connect the dots between thousands of data points across the floor, so quality checks are understood alongside machine performance.
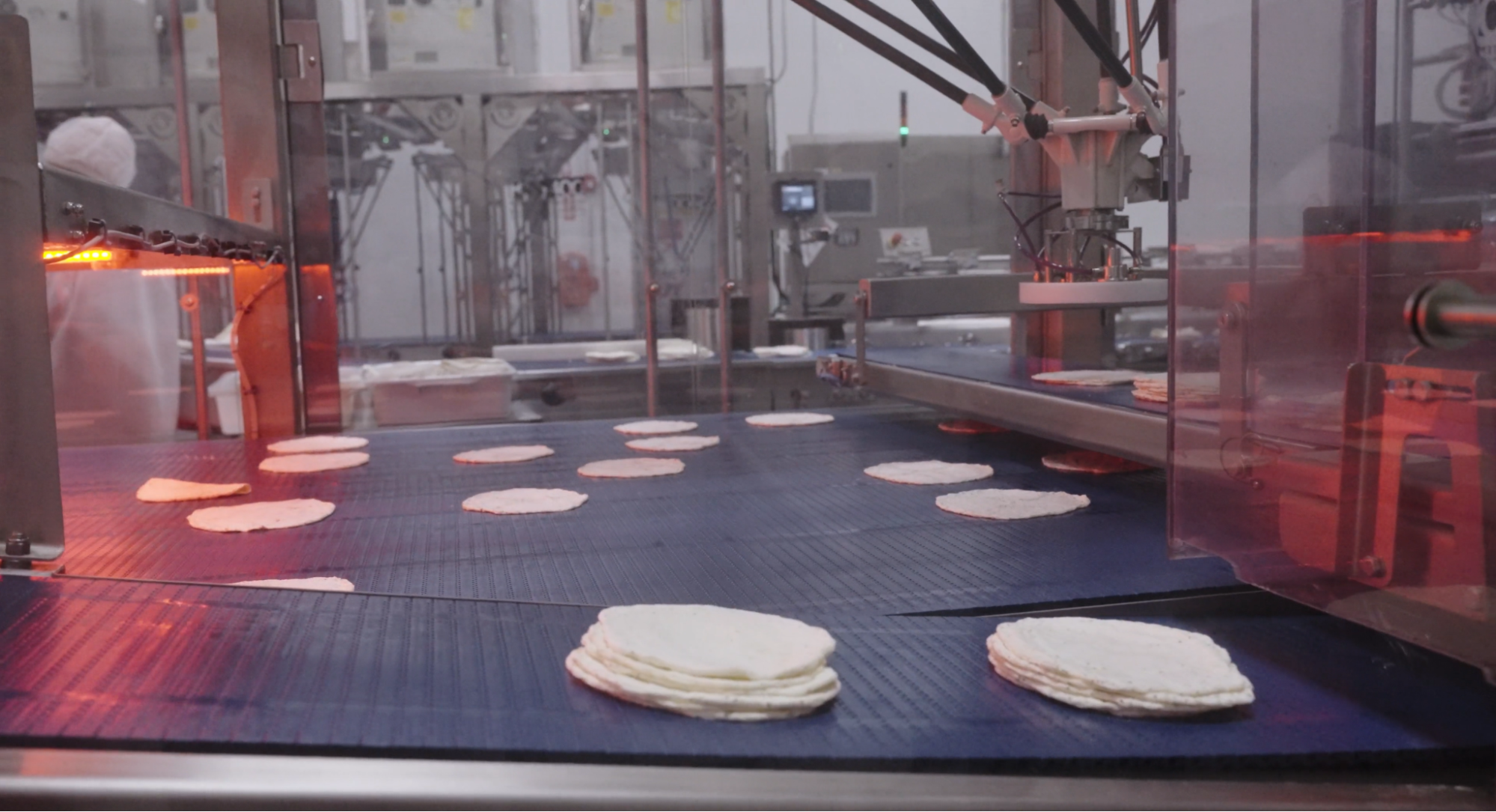
A Connected Plant Floor — A First- Or Last-Mile Issue?
It’s easy to sacrifice the future for the present, especially when point solutions promise to address today’s urgent problems and deliver “rapid ROI.” However, poor technology selection (i.e., inadvertently picking closed systems) leads to isolated data, limited interoperability, and poor growth potential. An accumulation of stand-alone applications is exactly how the majority of manufacturers end up with hundreds of subsystems, siloed activity, and a misunderstanding of how actions in one part of the plant impact the others.
With the introduction of advanced data processing technologies, there is a lot of interest in the “last mile” analytics — the gap in analytic output and actual changes in behavior on the plant floor. A more painful challenge for most manufacturers is the first mile and the “middle miles.” These miles involve getting the data out of the plant floor’s many closed systems and machines, and connecting it with other manufacturing subsystems (human input, machine performance, quality/compliance, etc.) to generate the appropriate context for better decision-making. Anything that doesn’t allow data in or out is a closed system to avoid; this should be table stakes.
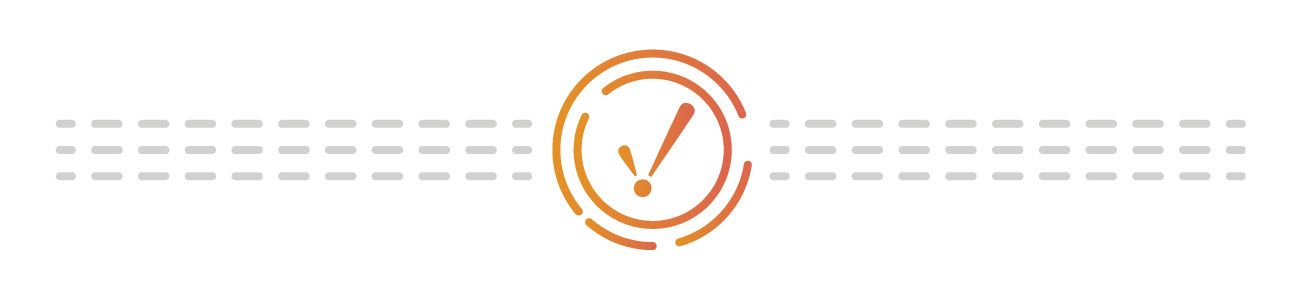
Solving The First Mile
An early constraint in the journey to a connected plant floor is leveraging as many of your existing systems as possible. When it comes to solving the “first mile” problem, Inductive Automation’s web-based supervisory control and data acquisition (SCADA) system, Ignition, is unbeatable. Ignition supports multiple frameworks and industry protocols, connects with your existing shop-floor stack, and elevates machine data for utilization in downstream systems and processes. There is no need to look further than Ignition to open up traditionally closed systems (and without breaking the bank).
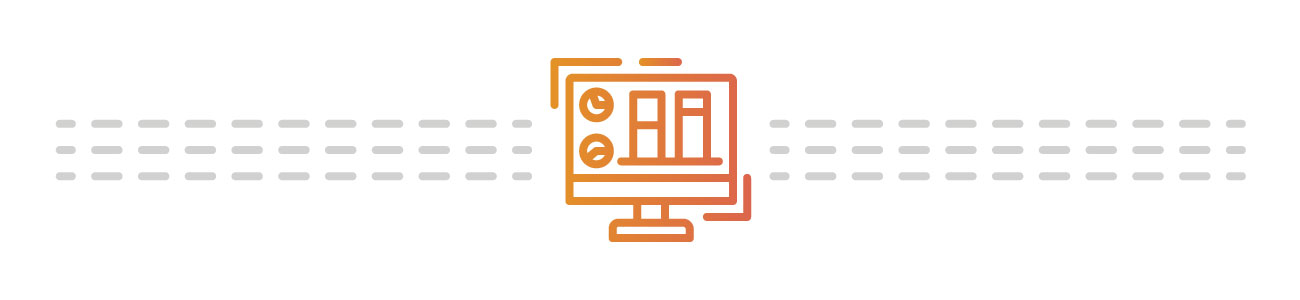
Solving The Middle Miles
The middle miles can be the most challenging due to the numerous subsystems on the plant floor. The average manufacturing floor still relies on (at least some) paper-based processes that make data difficult to utilize alongside existing systems. That’s where SafetyChain comes in as an Inductive Automation Alliance Partner.
SafetyChain is a digital plant management platform for process manufacturers trusted by more than 2,000 facilities to improve plant-wide performance. We unify production and quality teams with data, insights, and tools, and deliver real-time operational visibility and control by eliminating paper and point solutions.
Connecting Quality and Machine Data
For Egglife Foods, quality assurance bore the brunt of first- and middle-mile inefficiencies, with processes still heavily dependent on a mix of paper and spreadsheets. Leveraging SafetyChain and Ignition as its food and beverage manufacturing software, they turned what was once a complex and inefficient process into an automated, agile operation capable of delivering consistent, high-quality results in real-time. VP of Operations and Supply Chain Manesh Paudel emphasizes the importance of consistency: “We’re in a business where you’re rewarded for… doing the same thing day in, day out. That is exactly why SafetyChain and Ignition are so important.”
Egglife’s Journey To A Connected Plant Floor
Egglife Foods, Inc. produces a tortilla alternative that has never been made before. They can’t rely on any prior industry knowledge to inform their processes, so each quality check is a data point to help refine their path toward creating the perfect wrap.
When working with material as sensitive as eggs, any small deviation in product temperatures, wrap measurements, equipment flows, and hundreds of other process measurements can significantly change the product outcome. Their process generated thousands of paper-based and digital data points that were labor-intensive and challenging to align.
Before implementing Ignition and SafetyChain, their manual in-process quality checks left management unaware of failures on the line until after they occurred. Now, they are able to connect thousands of data points across the floor in real-time, and empower their personnel with the insights they need to fix issues in real-time. Egglife Foods Quality Manager Elisabeth Metzger said “I started my career in pen and paper; not having to wait until the end of the day to realize you had a failure on the line is huge.”
But it wasn’t just access to “real-time data” that made the magic happen. The seamless integration of data across subsystems allowed for end-to-end process automation and control. Ignition gave Egglife a tool to visually map data from their processes into SafetyChain’s APIs. SafetyChain’s Module for Ignition delivered real-time information right where users needed it (in the palm of their hands), automated corrective actions, and gave operators end-to-end control of Egglife’s workflow.
Egglife has also improved operator satisfaction by eliminating paper forms, and streamlining their audit processes, making it easier for auditors to understand their workflow from raw material to finished goods.
The Quality, Production, and Maintenance teams are now in a position to make sense and use of all their data.
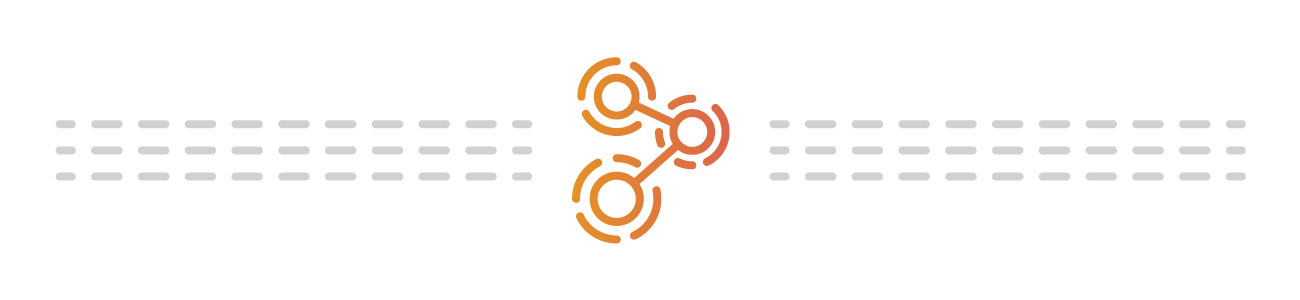
SafetyChain’s Module For Ignition
SafetyChain digitizes plant processes, enabling manufacturers to consume and act on information previously inaccessible in the plant. SafetyChain’s Module for Ignition automates the capture of machine data without a complex implementation, so manufacturers can gain richer insight into what is happening in the plant at any given time without disrupting production or requiring heavy customization. Also, Egglife Foods Team Lead Levi Overmyer likes that “the SafetyChain Module for Ignition was easy to install. We just dropped the file in, and we were able to start connecting machine tag data.”
Machine data that is captured by Ignition can drive actions within the digital plant management platform and automate essential plant processes, such as:
- HACCP Controls
- Acceptable Quality Limits
- Mobile Data Collection
- Production Performance
- Live Downtime Tracking
- Analytics and Reporting
Simply put, SafetyChain is integrated with Ignition to provide deep insight into the product that’s moving in, through, and out of your facility. Egglife’s success story is a testament to the power of this integrated approach.