Using MES Powered By Ignition To Accelerate Lean Manufacturing Goals
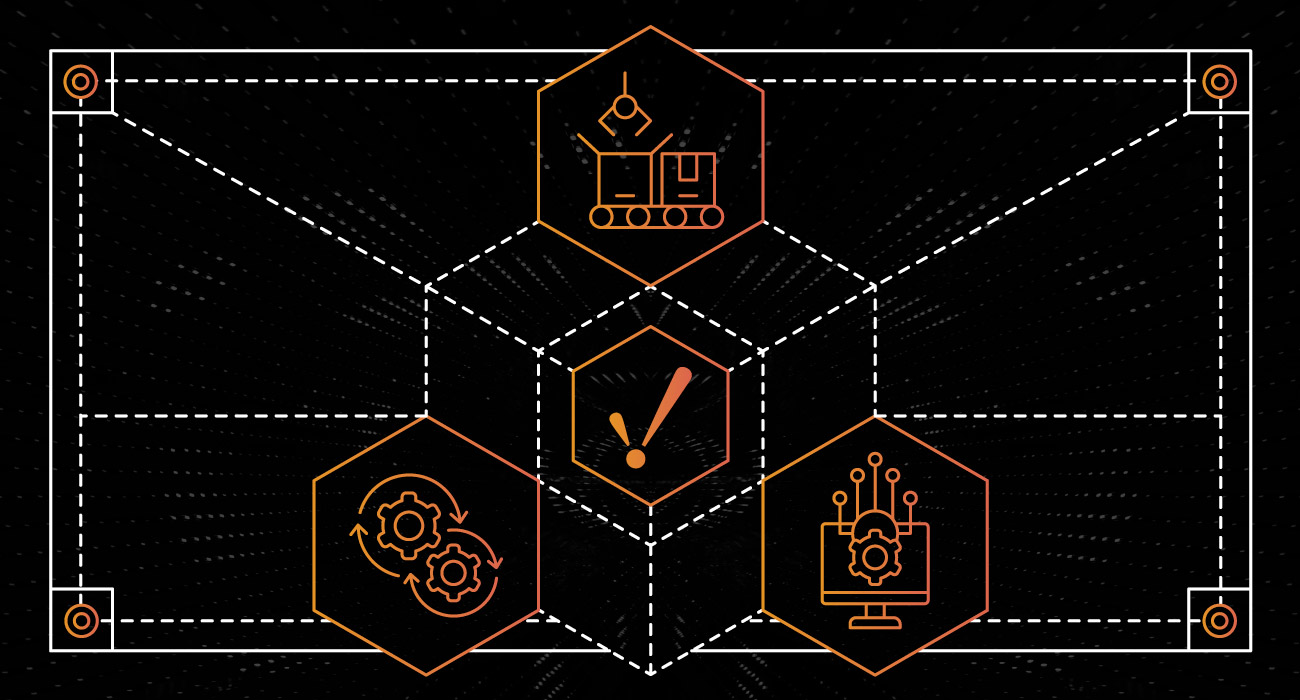
Staying competitive means manufacturers constantly seek ways to enhance operational efficiency, minimize costs and waste, and maintain the highest standards of product quality. Whether a manufacturer is just beginning to explore manufacturing execution systems (MES) or looking to optimize an existing MES infrastructure, and whether they use Sepasoft’s MES modules for the lean manufacturing software Ignition or build their own custom MES solutions, Ignition MES offers manufacturers a versatile solution to streamline production, improve visibility, and accelerate lean manufacturing initiatives across the factory floor.
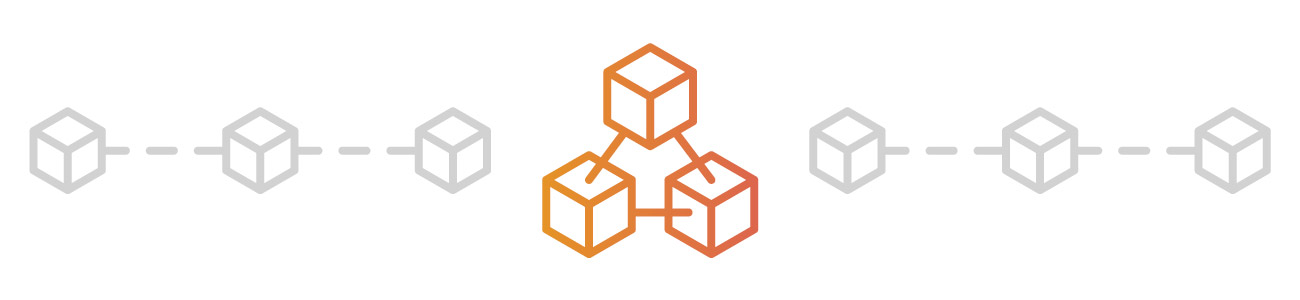
Current Trends In MES Driving Technology Adoption
Driven by advancements in Digital Transformation and the adoption of Industry 4.0 technologies, MES solutions enable real-time data integration and enhanced automation, significantly improving production processes and promoting lean manufacturing. Manufacturers adopting MES solutions have reported improvements in operational efficiency of 15-20% and reductions in production lead times of 10-15%.
Some of the key trends in MES driving manufacturers to adopt new technology include:
- Predictive Maintenance: MES technology helps manufacturers anticipate equipment failures before they occur, reducing downtime and maintenance costs.
- Digital Twins: Manufacturers use digital twins to create virtual replicas of manufacturing processes and equipment, enabling manufacturers to simulate and optimize operations without physical testing.
- Reshoring and Local Production: With supply chain disruptions and the need for resilience, some manufacturers are reshoring their operations to reduce the reliance on overseas suppliers and enhance supply chain flexibility.
- Sustainability and Carbon Neutrality: Environmental, social, and governance (ESG) initiatives push manufacturers to adopt sustainable practices, such as reducing emissions, using renewable energy, and adopting eco-friendly production processes.
- Industrial Automation and Robotics: Manufacturers integrating robots and AI enable more autonomous and smart manufacturing processes, improving productivity and precision. This trend also extends to collaborative robots (cobots) that work alongside human employees to streamline operations.
- Advanced Data Analytics and AI: Utilizing data analytics and AI to monitor production, improve quality control, and predict maintenance needs is becoming increasingly important to optimize processes and make data-driven decision-making.
- Cloud Computing and IIoT: Adopting cloud solutions and Industrial Internet of Things (IIoT) technologies, manufacturers can connect machines, systems, and processes for better data sharing and real-time monitoring.
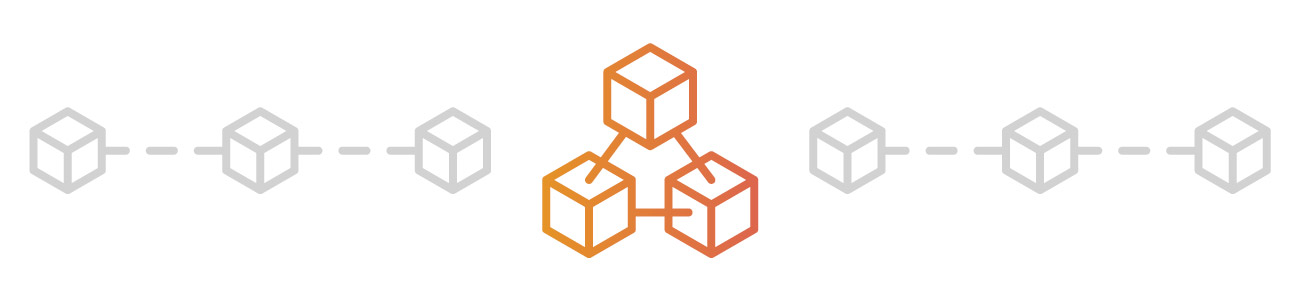
How Ignition MES Addresses Trends In MES
Ignition MES software is designed to align with and support the key trends, like lean manufacturing, shaping the MES landscape:

1. Reduce Downtime And Delays With Real-Time Equipment Monitoring
Ignition's data-driven architecture enables manufacturers to integrate real-time data from machines and sensors to continuously monitor equipment performance. By using advanced analytics and machine learning models, Ignition can predict potential equipment failures and trigger maintenance activities before breakdowns occur, ultimately reducing unplanned downtime and maintenance costs, and enhancing overall equipment effectiveness (OEE).

2. Respond Faster To Market Changes
As manufacturers look to localize production to reduce supply chain vulnerabilities, Ignition's flexibility and scalability enable easy deployment and expansion of MES functionalities. It allows companies to quickly set up operations in new facilities, providing centralized control and visibility across multiple sites. This facilitates a smoother transition to local production and helps companies respond more quickly to market changes.

3. Support Sustainability Efforts With Real-Time Data Analysis
Manufacturers can track energy usage, emissions, and resource consumption to identify inefficiencies and implement operational improvements on the plant floor. Additionally, the software’s reporting capabilities can help companies adhere to environmental, social, and governance (ESG) standards by providing insights into production processes and their environmental impact.

4. Advance Smart Manufacturing Strategies With Automation
Ignition supports OPC UA, MQTT, and other industry protocols, making it possible to connect and control robotic systems and industrial equipment. This connectivity helps manufacturers automate repetitive tasks, optimize workflows, and implement smart manufacturing strategies that enhance precision and productivity.
An example is integrating a Digital Work-in-Progress (WIP) solution within an MES. By digitizing the work-in-progress workflow, manufacturers can replace cumbersome paper-based processes with automated workflows and detailed, real-time tracking capabilities. Capturing and managing data at every stage of the process, a Digital WIP solution ensures a complete view of production status, enabling better decision-making and quicker responses to changes on the shop floor. The result is enhanced production accuracy, reduced lead times, and improved product quality.

5. Move To A More Data-Driven Approach To Decision-Making
Ignition’s built-in analytics tools allow manufacturers to leverage data from production systems for advanced analytics. Its scripting capabilities and third-party integrations enable AI models to analyze vast amounts of data, providing predictive insights for maintenance, production optimization, and quality control.

6. Easily Connect Devices And Systems Across The Factory Floor
Manufacturers can deploy Ignition MES on-premise, in the cloud, or in hybrid environments, allowing for flexible data storage and access. This connectivity enables real-time monitoring, remote access, and data sharing, ensuring that manufacturers can build interconnected, smart factories.
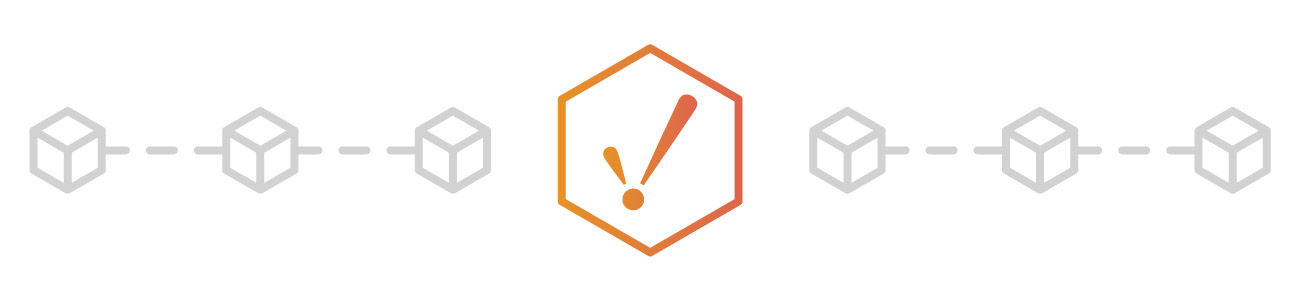
Leveraging MES Powered By Ignition In Your Manufacturing Operations
Ignition MES stands out by embracing the latest MES trends driven by Digital Transformation and Industry 4.0. By leveraging Ignition’s capabilities, manufacturers can accelerate Digital Transformation, enhance production visibility, and optimize operational efficiency, aligning with the current trends like lean manufacturing and shaping the MES landscape.
NeoMatrix specializes in MES solutions that allow your team to focus on core manufacturing activities and optimizing your MES system for maximum productivity and efficiency.