12 Batch Implementation Design Considerations
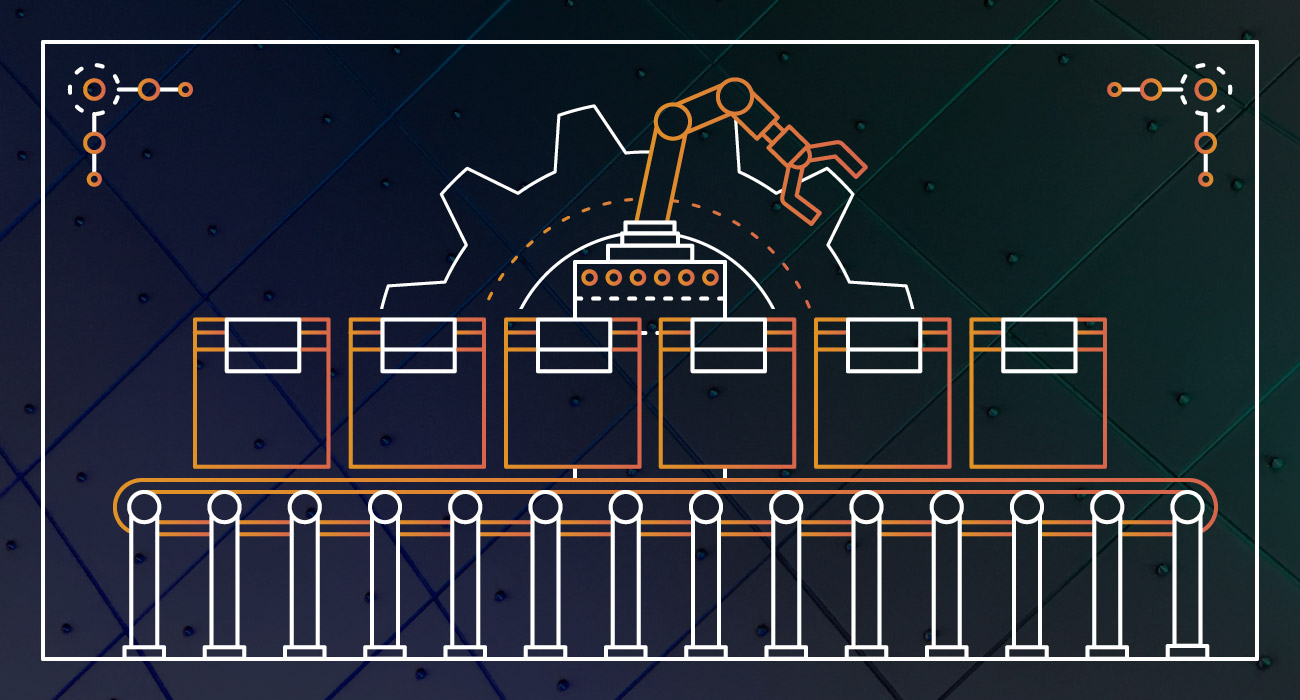
Batch systems are used for maximizing quality control, minimizing cost, and reducing loss by manufacturing smaller batches compared to a mass production model, which is why companies in the food and beverage, pharmaceutical, and chemical industries rely on them. The audience of a batch system is varied, and therefore the proper implementation of a batch system needs to consider many factors. From the Plant Manager, Operations, Engineering, and Maintenance to the Operators, all these personas have unique needs that must be considered.
The best practices dictated by standards such as ISA 88 and ISA 95 provide a great guideline or starting point, but these standards do not prescribe how to implement the details of a solution. Therefore, the following is intended to highlight some of the considerations for a system design.
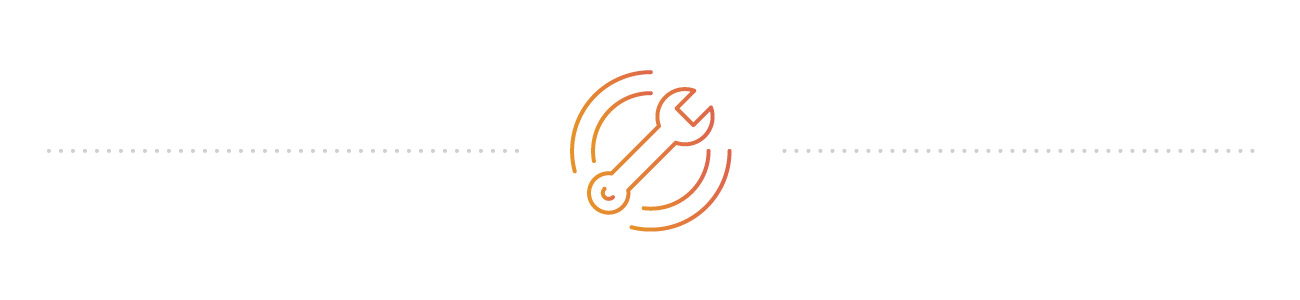
Creating a Robust Equipment Model for Optimal Plant Performance
A plant’s capabilities of what and how products can be manufactured there reside in the capabilities of its equipment, materials, and personnel. These capabilities are captured by the Equipment Model as defined in ISA 88 & 95. Once you capture these capabilities, they are exposed to the recipe author to define how to execute the product manufacturing workflow, which is detailed in the ISA 88 Procedural Model.
Having a well-defined Equipment Model is paramount to enabling the plant’s maximum capabilities while providing the recipe author and operators with an intuitive experience. The Equipment capabilities definition should include the activities that the automation controls system can perform (i.e., Add Water) as well as the activities performed by the operators and other personnel (i.e., Manual Additions, Lab Sample Data, etc.).
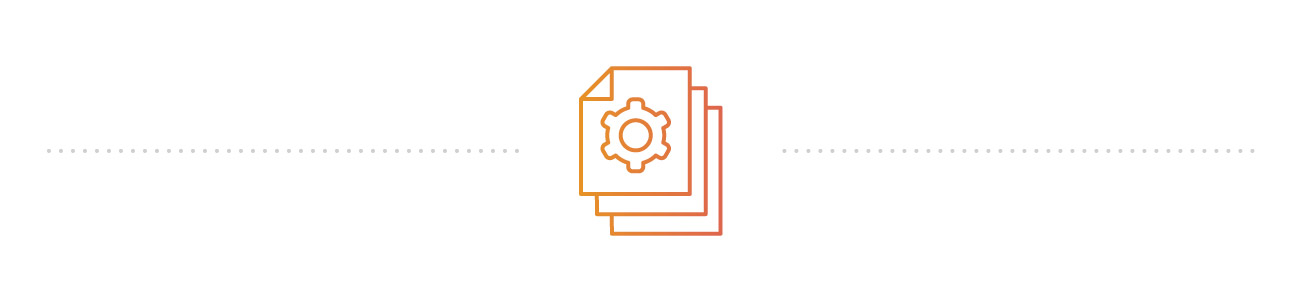
Suggested Steps for Designing a Batch System
The process and instrumentation diagrams (P&IDs) can define many capabilities, but other capabilities will not show up on these documents. You can define these by understanding what the operator’s activities may be. The following approach has served me to methodically focus on the different design considerations:

Step 1: Understand the scope of the project.
On the vertical scope, is the solution going to receive orders from an ERP system? Or is the operator going to initiate a control recipe and start it? On the horizontal scope, does it include the receipt and management of raw material all the way to finished product storage, packaging, or shipping?

Step 2: Identify the process cells and units.
In defining the ISA 88 equipment model, you need to identify the process cells and units. To determine which units exist, we need to keep in mind that recipes as per the ISA 88 Procedural Model or workflows are executed against a unit, such as a pre-weigh vessel, mixer, reactor, cooker, liquefier, fermenter, or similar.
Other locations where workflows may need to be specified via instructions may be manual pre-weigh areas of minor and micro ingredients, material receiving, and shipping areas, etc. Keep in mind that a unit does not have to have the physical form of a vessel and that not all vessels are units. Included in the design may be equipment that needs to be cleaned or sterilized separately from the main processing vessels, such as transfer lines.

Step 3: Focus on the ISA 88 phases in each unit.
Once the units are identified, focus on the ISA 88 phases belonging to each unit. Note that it is best to focus on the actions (verbs) and not on the phase details at this time (i.e., what parameters you use, what information you will capture for reporting, etc.). We don’t focus on which equipment will be used to perform each action, also keeping in mind that the name definitions of the phases are what you will present to the recipe author to construct the recipes that specify the workflow.
In this step, we will only focus on the flow of material coming into the manufacturing process equipment, how you transfer it between units, and how you remove it from the manufacturing process. For example, we may identify these phases as Truck Receiving, Material Add, Manual Material Add, Transfer Out from a Unit, Transfer In, Unload to Storage, Transfer to Packaging, Load Truck, etc.

Step 4: Focus on the phases within the unit.
Next, we’ll focus on what phases exist within the unit. Common phases are Agitation or Mixing, Heat, Cool or Temperature Control, Pressure Control, Check Equipment Readiness, Check Equipment Cleanliness Status, Clean in Place, or operator prompts such as Take a Sample, Prepare Equipment, etc.

Step 5: Identify unit information you can use to determine recipe transition conditions.
Examples of unit information that can be used to determine recipe transition conditions include vessel weight, level, pressure, temperature, pH, or other instrument information. The recipe author can use these values to make recipe decisions, and to define when a step should start or end.

Step 6: Determine equipment arbitration.
In this step, we define which equipment is used for each phase and determine what phases are shared among multiple units. Note that a resource can be shared by more than one unit or phase.

Step 7: Define phase parameters and information to report.
In this step, we define the relevant information required to perform the phase (verb). With this information, we can clearly specify how to perform a phase (action). You can specify the complexity of a phase to not only enforce a critical action but also capture any pertinent information that will help determine how it executed each task. Keep in mind that the recipe author specifies all these tag values as information that ends up in the batch record. These are some recommendations:
- Provide meaningful names so the recipe author as well as reported information can be useful, i.e., Amount Setpoint, not just setpoint or just amount.
- Be consistent with the naming convention.
- Capture in a report the value and number of instances if the operator or other logic changed any parameter specified by the recipe, i.e., agitator speed setpoint changed.
- Material addition phases notify the operator if the addition is out of tolerance and allows the operator to select what action to take.
- Material addition phases learn the pre-act value and update future instances according to the learned offset.
- You can configure material dosing phases to specify the amount setpoint for dynamic adjustment to the amount based on the material properties, i.e., adjust the amount of grain to compensate for moisture content and further update the amount setpoint of water required to factor in the amount of water that came in with the grain.
- Each phase that requires the use of equipment should check the status of the equipment required and notify the operator if the conditions are not as required, i.e., is any required equipment faulted or in operator mode.

Step 8: Design the phase so the recipe author must only specify basic phase parameter values.
The recipe author specifies the phase parameter values. There are other parameters that the phase requires that should not be in the recipe parameter but rather as an engineering parameter to perform a task.
Examples include the tuning parameters of a temperature control loop or the amount of material pre-act that a dosing or addition phase requires. Part of the design should be to provide the recipe author with the ability to specify how to make a product without requiring detailed knowledge of how to perform this task, i.e., Add Water, by simply specifying the amount setpoint required.

Step 9: Create report values that provide additional information.
For example, during the addition of a material, the actual amount of material added is typically captured but the phase can also capture the weight of the vessel before commencing the addition and after the completion.
You can use this type of information to perform investigations. For example, if we know what the weight of the tank was at the end of dosing Material A but, during the addition of Material B, the initial weight did not match the final of Material A, there may be something worth looking into.

Step 10: Use report values to gain knowledge about your process and product.
Additional report values can include things like maximums and minimums for flow rates, temperatures, speeds, torque, etc. You can use this information to further understand the process’ performance and its impact on the product quality or throughput.

Step 11: Provide additional parameters to the recipe author.
Since we, the engineers, do not know what procedural action is desired by the recipe author during an execution exception, we should provide additional parameters to give the author the ability to determine the remedial behavior.
For example, if a recipe is placed on hold or paused, what should happen with the agitator speed setpoint, temperature setpoint, or the behavior of a timer? Should it continue or not? Holding behavior could be to continue, hold value, or reset, etc. For this, we provide additional parameters such as Holding Speed Setpoint, Holding Temperature Setpoint, or Timer mode.

Step 12: Check the status of your equipment.
Other phases can include a phase used at the start of a recipe that checks for the health of all the equipment in that unit. This phase will then notify the operator if any piece of equipment in the unit is not ready to be used, so the operator may decide to continue or resolve the issue before the unit’s activities commence.
Other examples may include phases that you can use to synchronize activities between units, ones that keep track of and update the cleanliness status of a unit, and phases that visually inform the operator via the HMI of the current activities taking place in the unit.
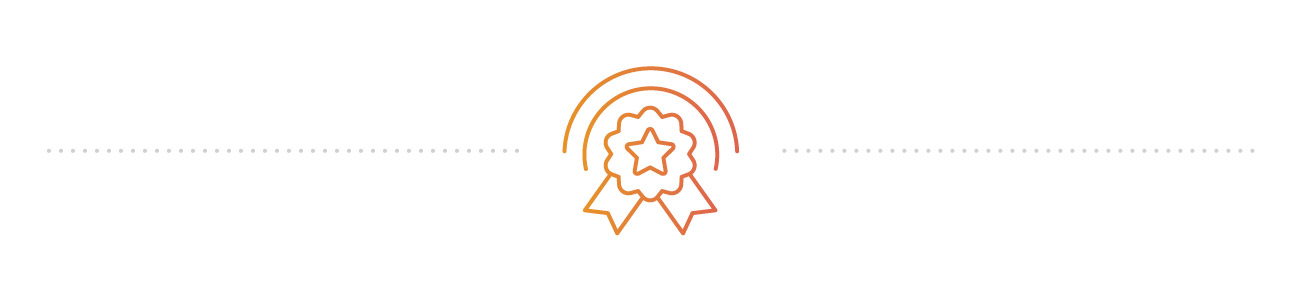
Craft Superior Products by Harnessing Automation Best Practices
Now that we’ve looked at some important considerations for designing your system, here’s another thing to keep in mind: One of the goals of implementing automation is to allow an intuitive way to specify and capture the best practices for manufacturing a product when using the recipe editor. By enforcing the execution of these best practices and capturing relevant information that the system audience can use, you'll allow everyone to understand how the product should be manufactured and how it was manufactured.