Hatching a Better Incubator: The Evolution of an Engineer’s Personal Project
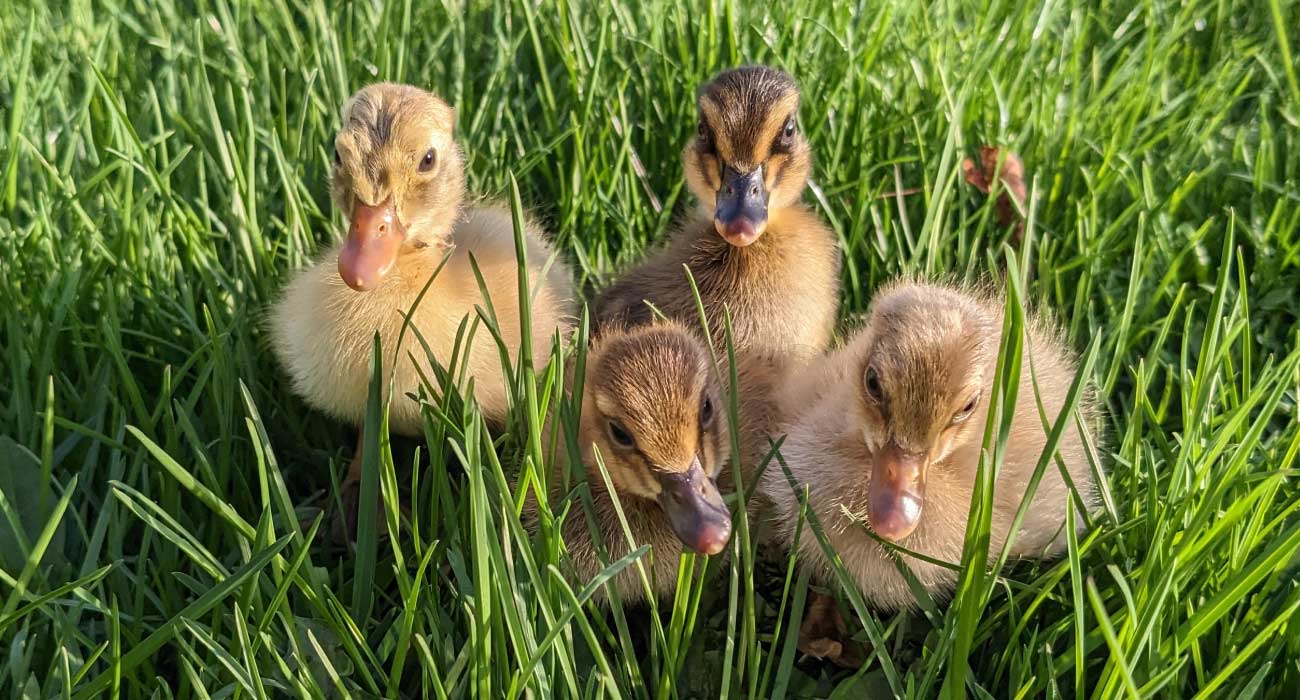
I’ve long been fascinated by incubating bird eggs — to me, it’s like a little miracle every time I see a duckling come out of its shell. This fascination, married with my love of technology and engineering mindset, led me to build my very own automated egg incubator, which I’ve used to hatch a number of different species, including chicken, bobwhite quail, and guinea fowl.
But let me rewind a little bit, to tell you the story of how I got the incubator to where it is today. And to do that, we have to go back about 10 years to my basement workshop in Central Pennsylvania.
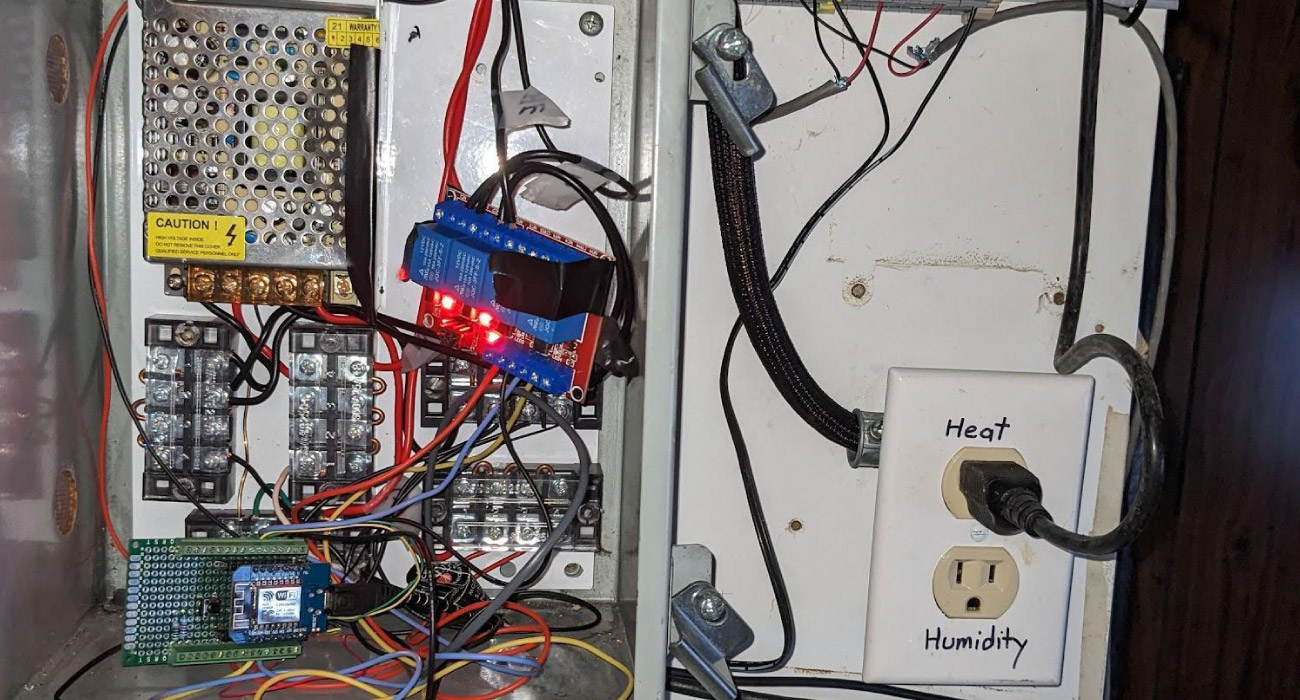
How It All Began
It started with a desire to overcome the barriers of low-cost, off-the-shelf incubators. It’s hard to control temperature and humidity with these types of incubators, there’s no airflow, no way to rotate eggs, and they need to be checked on frequently.
I was determined to build a better mousetrap, so to speak.
So I set to work and built my first version: a styrofoam incubator with manual controls and zero logging capabilities. From there I upgraded to a dorm room refrigerator with an Arduino-based control system and a Visual Basic UI. This version worked decently well, but I wasn’t satisfied with the clunky UI. I improved the incubator significantly in its third version with a Blynk-built mobile app, but it still lacked a lot of the functionality I envisioned.
Then one day, at work as a process engineer at a graphite manufacturing plant, an integrator introduced me to an industrial application platform called Ignition. It was the software I’d always imagined, and from that moment on, my life as an engineer and innovator would never be the same.
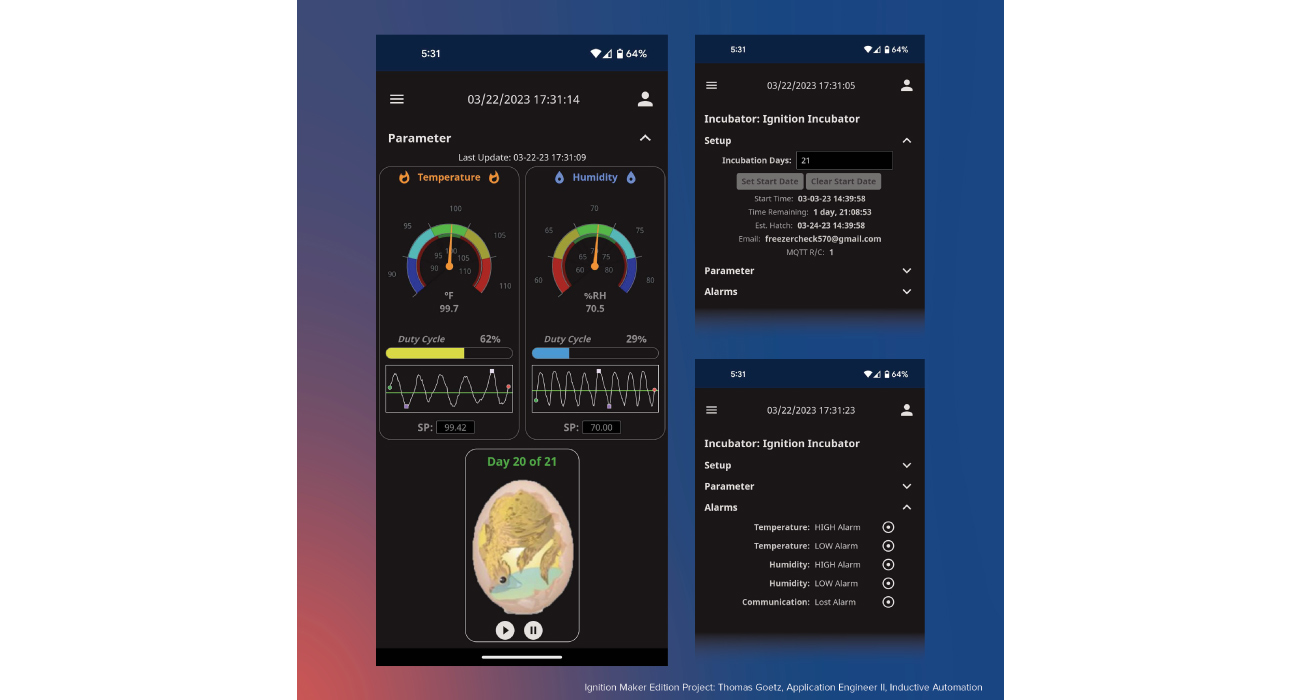
Building Incubator 4.0
I used Ignition Maker Edition to build the most recent version of my incubator, and with the software’s ability for data visualization and improved communication, my project was able to truly evolve. The incubator runs a C++ based language (Arduino IDE) and now has automatic egg rotation, communication via a Hive MQTT broker, and a user-friendly UI with setpoint control, alarm notification, and data monitoring.
The alarm notification feature relieves me of the anxiety that something might go wrong without my knowledge, since I now get notified if the incubator loses communication, as well as if temperature or humidity gets too high or low. When there was a power failure a while back, the system immediately alerted me via my mobile device, and I was able to solve the issue in 25 minutes. Without the alarm I wouldn’t have checked on the eggs for six to seven hours, at which point I likely would have lost them all due to the cold.
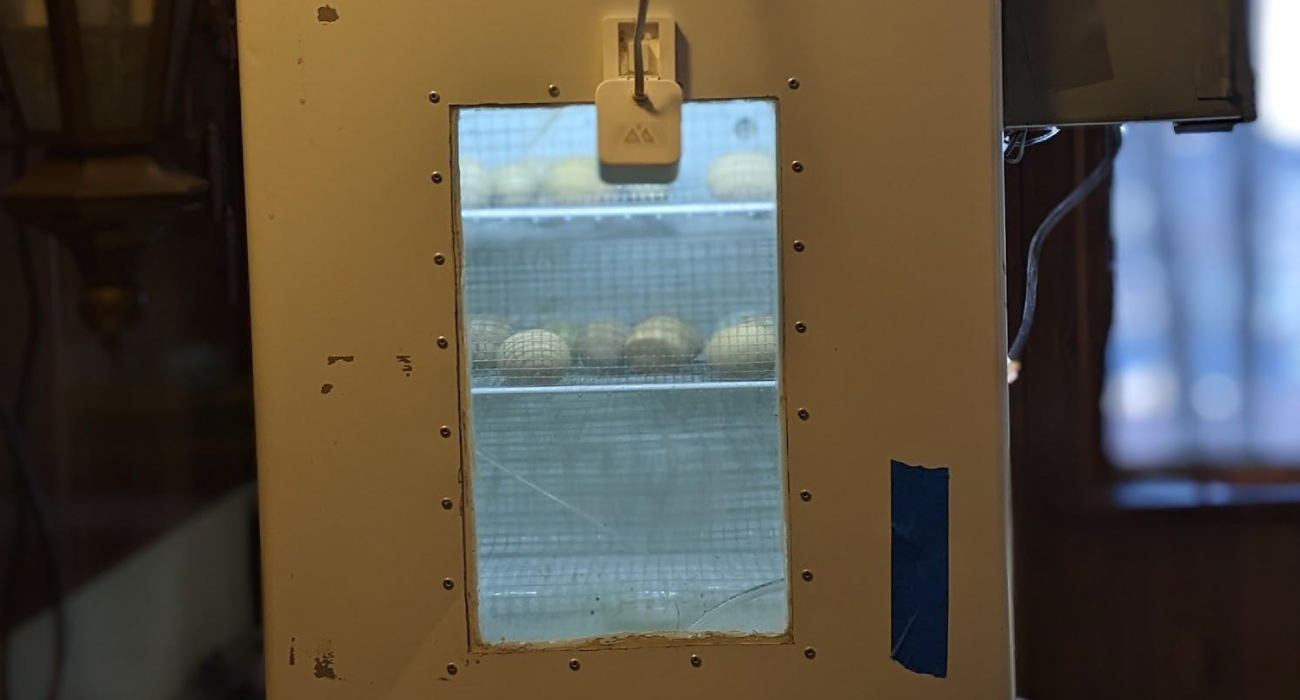
Incubator Hardware
A major goal for this project was to keep it as low-cost as possible, and I was able to achieve that, having spent around $150 for the current version of the incubator. I built a lot of the equipment myself and used a 3D printer for many elements.
Here’s a list of all the hardware that the incubator contains:
- Dorm Room Refrigerator
- Computer Fans
- WeMos D1 Mini Microcontroller
- 4 Channel 12V Relay Module
- Si7021 Temperature and Humidity Sensor
- 12VDC 4A Power Supply
- 100 Watt Tube Heater
- LGP-1 Gear Pump
- Custom Designed and 3D-Printed “Shower Head”
- Gear Motor
- Custom Designed and Machined CAM system
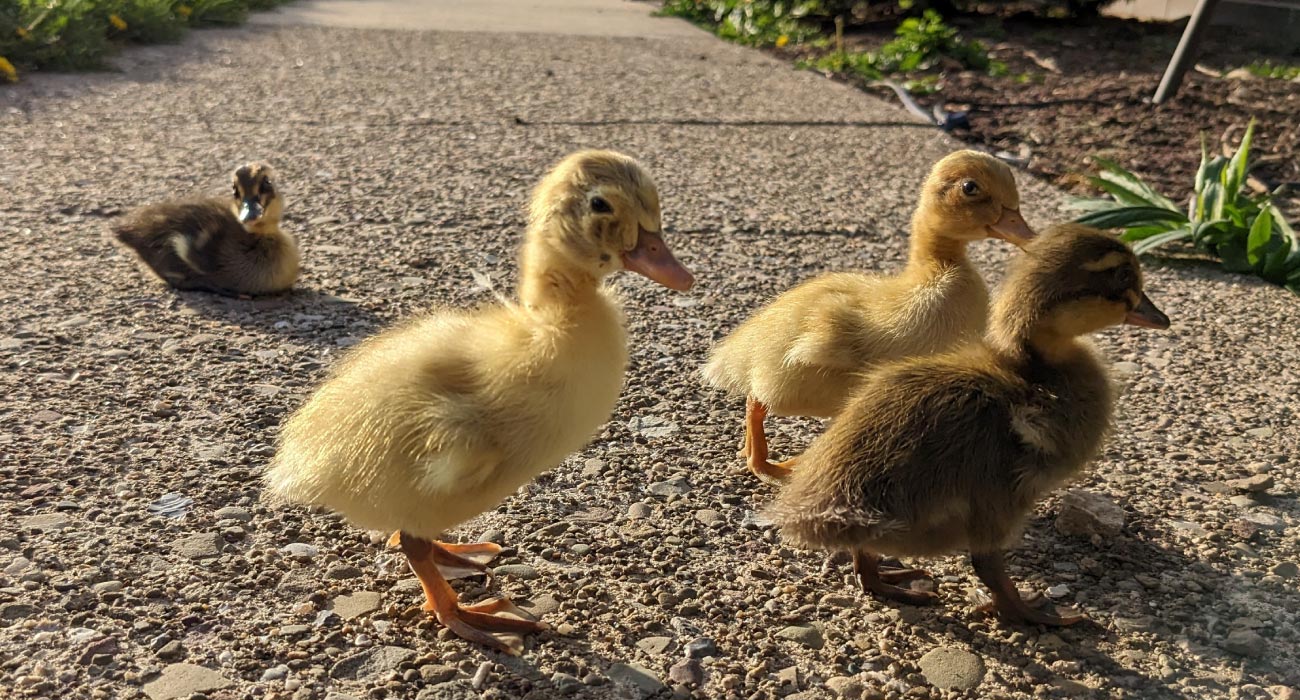
Finding Freedom with the IoT
The IoT element of the system makes my life a whole lot easier. The system publishes and/or subscribes to a number of different topics via MQTT, including temperature, humidity, heartbeat, temperature setpoint, humidity setpoint, and more. And the incubator toggles the heater and humidity pump ON or OFF based on the current value, setpoint, and deadband.
I run Ignition Maker Edition on my own server, and use a Hive broker that sits up in the cloud. Because of this, I can communicate with the incubator no matter where I am. And the incubator itself has mobility. Thanks to a WiFi chip on its microcontroller, I can easily connect it to a different network if I need to relocate it. Having such an easy, remote way to communicate with the incubator has been a game changer.
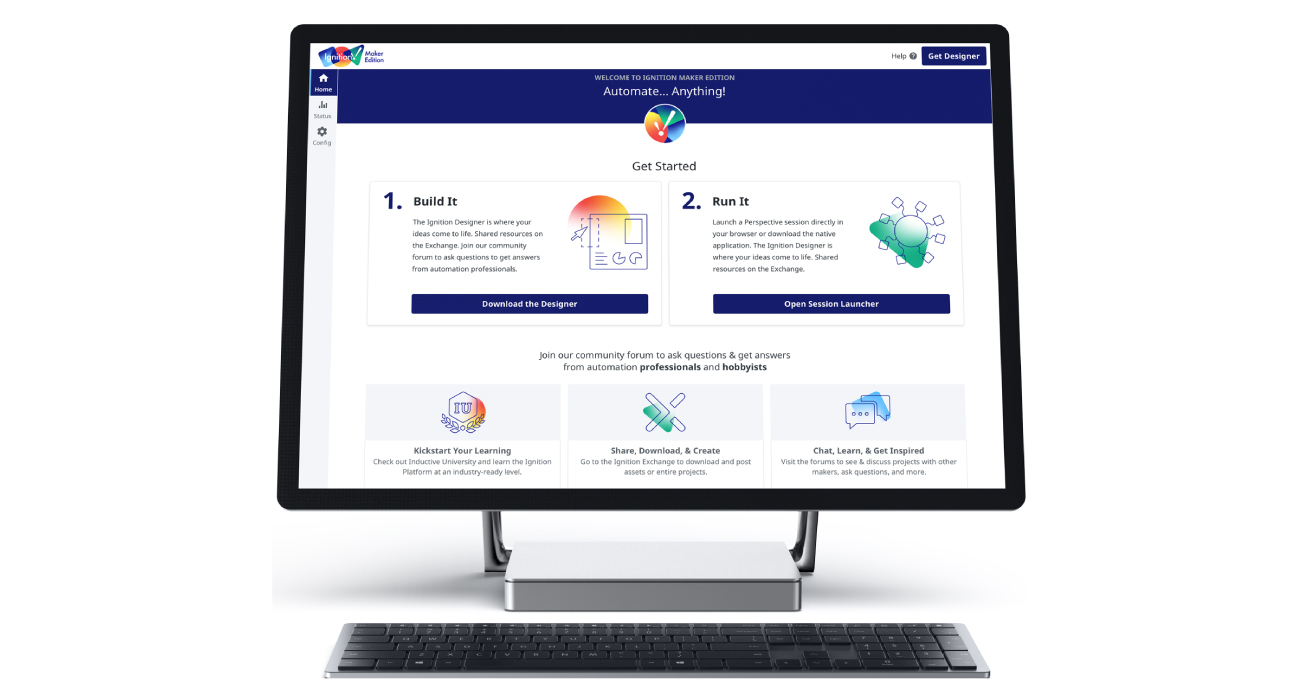
More Innovation on the Horizon
I’m excited about the limitless possibilities the future holds for my incubator. Since discovering Ignition, I’ve come to work as an Application Engineer II at Inductive Automation, the company that created the Ignition platform. The motto here is “Dream It, Do It,” and I’m having a blast turning my incubator dreams into reality.
Some of my main goals for the next version of the incubator include using Sequential Function Charts to control all aspects of the system, incorporating machine learning for temperature and humidity setpoint decisions, and setting up a Hatch Rate UI, but I doubt it’ll stop there! Also, by the end of this year, I plan to share the code and UI for my project on the Ignition Exchange — a place where people can freely share projects with the community.
As a final note, I’ll leave you with this — if you’re looking for software to create your own innovative control systems, whether for home automation projects or something you’re building just for fun, I encourage you to take Ignition Maker Edition for a spin. It’s completely free and incredibly intuitive to use. You’ll be amazed at what you can make with it!