Why Manufacturing Workflow Is Core To MES
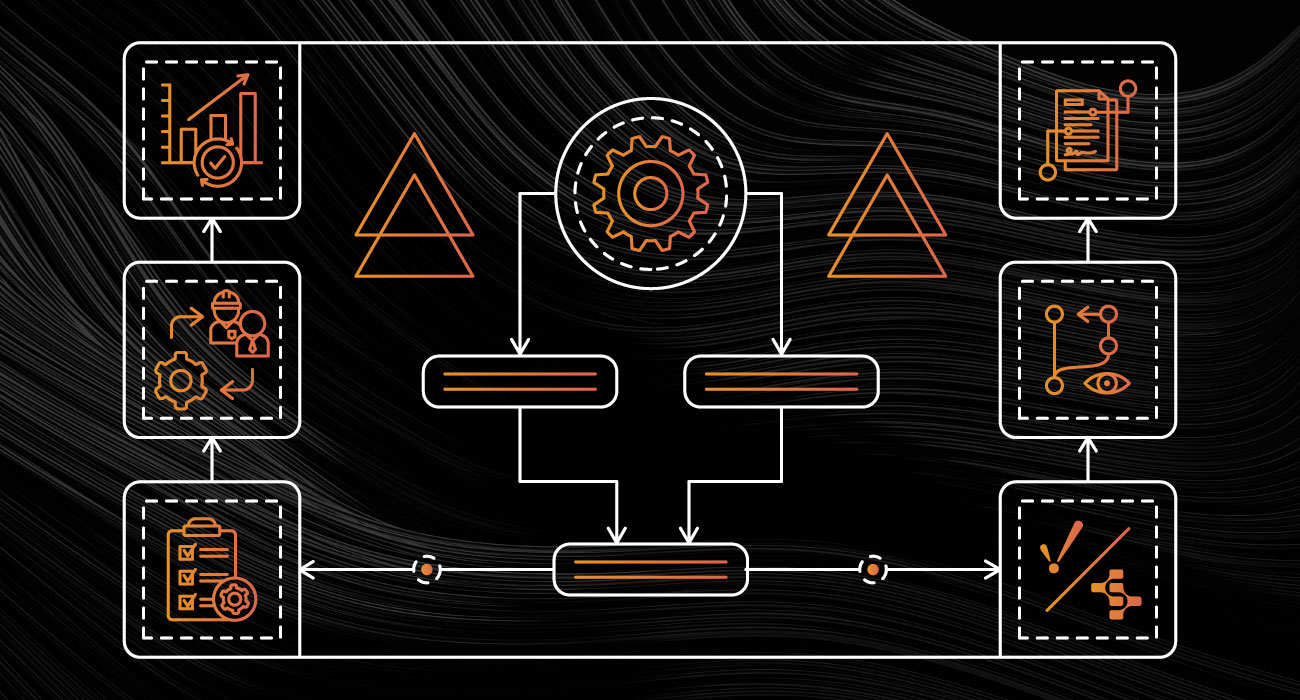
When we think about MES (Manufacturing Execution Systems), certain features tend to dominate the conversation: real-time dashboards, machine connectivity, OEE (Overall Equipment Effectiveness), downtime tracking, and production analytics. These capabilities are the focus of product demos, sales presentations, and improvement meetings because they are highly visible, easy to grasp, and often show immediate value.
But behind these familiar tools lies a quieter, foundational capability that doesn’t always get the spotlight it deserves. At the core of MES is a workflow layer — sometimes called a workflow engine, tool, or management system — that orchestrates operations, serving as a digital model of how products are built, tested, moved, and verified. While dashboards and metrics help you monitor plant-floor activities, the workflow layer translates production plans into step-by-step execution.
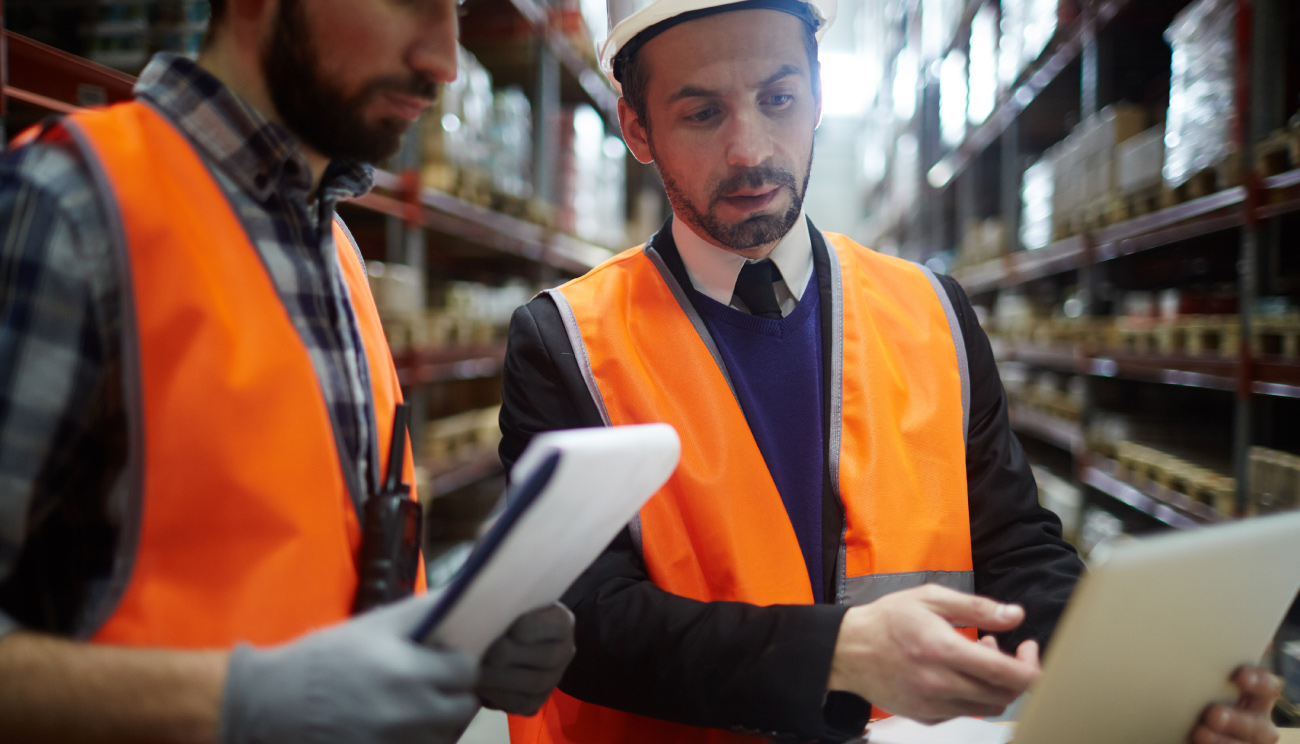
What Is Manufacturing Workflow?
Manufacturing workflow is the step-by-step process that defines how a product gets made — from raw materials to finished goods. While many manufacturers still rely on paper checklists or verbal communication to manage production tasks, a workflow engine digitizes the entire sequence of tasks, making sure everything happens in the right order, by the right people or machines. This digital workflow outlines each step in production, including which equipment to use, what operators need to do, when quality checks happen, and where data needs to be collected. It acts as a central guide that keeps everything coordinated.
In MES, this workflow layer is the backbone of execution. It translates high-level production plans into real-world actions by sending the right instructions to the right systems, stations, and people. Whether you're building one item or running production across multiple facilities, a workflow ensures the process is followed consistently, and alerts you when something doesn’t go according to plan.
To see how this plays out in practice, let’s explore how workflow tools support some of the most critical aspects of manufacturing.

1. Order Execution
ERP systems might schedule production orders, but it’s the MES that turns those high-level plans into concrete actions. A production workflow defines the exact sequence of tasks needed to execute each batch or unit, such as machine instructions, operator prompts, quality checks, and data collection.
Without it, these steps are often scattered across SOP documents, embedded in custom scripts, or passed down through tribal knowledge. With a digital workflow in place, procedures are no longer left to interpretation — they’re clearly defined, repeatable, and built into the system itself. That’s especially important when something goes wrong or when someone new is learning the ropes. Standard workflows can guide experienced operators through uncommon situations and help new hires perform tasks accurately without relying on verbal instructions or guesswork.

2. Hybrid And Manual Processes
Not every manufacturing step can — or should — be automated. Tasks like inspection, weighing, scanning, and verification still rely heavily on human involvement. Traditional MES platforms often fall short when it comes to handling this mix of manual and automated work.
By supporting automated, manual, and hybrid steps, the workflow engine reflects real-world processes rather than forcing operations into an unrealistic mold.

3. Consistency At Scale
As manufacturers expand across production lines, shifts, and facilities, inconsistencies naturally begin to surface. Teams develop their own workarounds and habits, leading to variation, inefficiency, and quality drift over time.
A well-designed workflow tool helps prevent this by embedding standardized procedures directly into the system. Best practices become part of the process itself, ensuring every operator, on every line, follows the same proven steps, regardless of location or shift.

4. Compliance And Audit Readiness
In regulated industries, it’s not enough to deliver the right result — you also need to prove how you got there. A workflow system captures detailed execution data at every step, automatically recording who did what, when, and how. It can also enforce sign-offs and require approvals for deviations, ensuring that any non-standard actions are reviewed and documented in real time.
This creates a complete, time-stamped history of production without relying on paper records or manual logs. When auditors come calling, the documentation is already in place: organized, accessible, and audit-ready.

5. Visibility And Agility
Defined workflows make it possible to track progress in real time. You can see exactly where each order stands, identify which tasks are in progress, and spot bottlenecks before they become bigger issues.
When it’s time to adjust a process, a flexible workflow engine makes those changes simple to implement. Teams can update procedures quickly without writing code or reengineering the system.
What To Look For In A Workflow Tool
If you’re evaluating MES platforms, a solid workflow engine should check a few key boxes:
- Handles both manual and automated tasks with ease
- Provides real-time status updates on active processes
- Enables changes without complex development
- Automatically captures execution details as work is completed
- Generates Electronic Batch Records (EBR) to support compliance and review
- Scales across lines, products, and facilities
Built On Ignition. Driven By Sepasoft.
Ignition by Inductive Automation is the ideal foundation for orchestrating complex production processes, offering real-time device connectivity, rich visualization tools, and a modular architecture that scales with your operation.
Built on Ignition, Sepasoft delivers a powerful workflow solution for batch, discrete, and continuous manufacturers. It’s designed to digitize and standardize complex procedures, whether coordinating automated equipment, guiding operators through manual tasks, or synchronizing activities across multiple sites.
Learn more about Sepasoft's approach to workflow management.
See how a biopharmaceutical manufacturer is leveraging Sepasoft’s workflow solution.