The Best Time to Begin Your Digital Transformation is Now
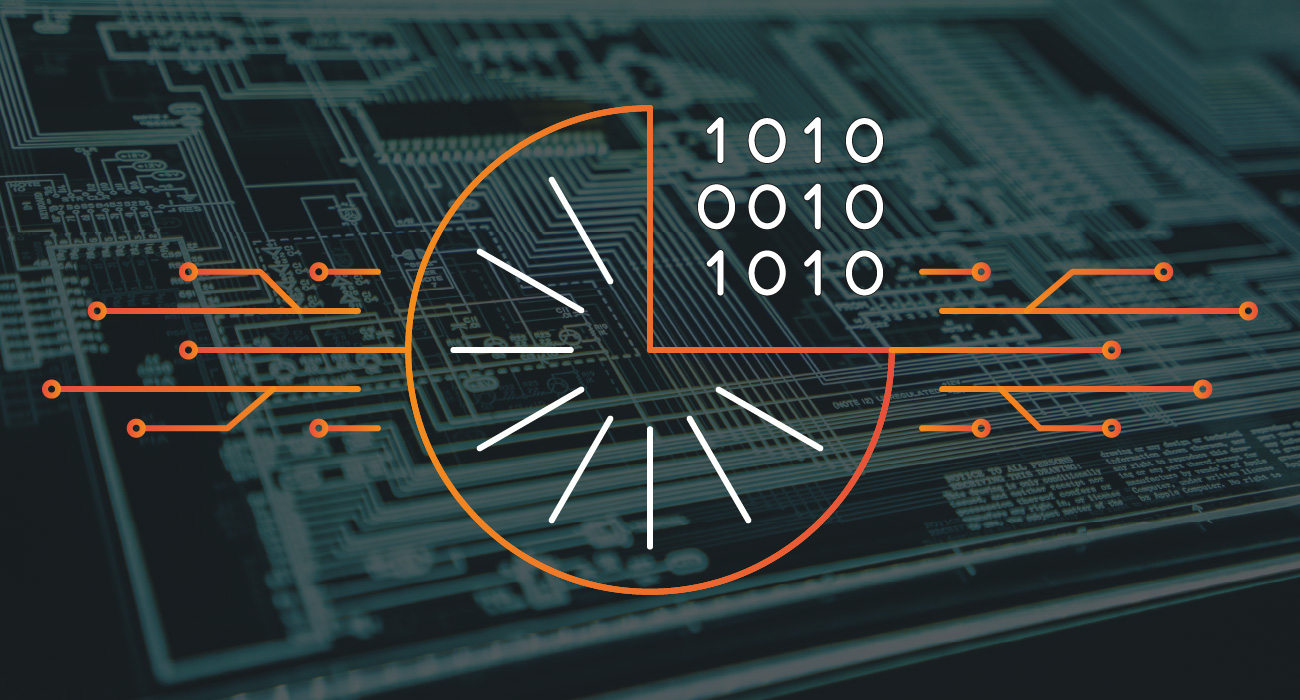
“The best time to plant a tree was 20 years ago. The second best time is now.”
I'm asking you to humor me while I apply the core message of that popular Chinese proverb to the area of Digital Transformation:
“The best time to start your Digital Transformation was years ago. The second best time is now.”
Advances in technology and availability of new hardware and software platforms have made Digital Transformation of your business simpler than ever. Rather than assuming you need to engage in a lengthy and costly consultation process with an outside party, I'm proposing you begin connecting your facility now. And getting started doesn't have to require a huge investment of time or money.
A Digital Transformation Solution Doesn’t Have to be Complicated — Anymore
The early days of industrial automation tended to be rather laborious. It required extensive experience in ladder logic and proprietary automation languages. Seeking efficiencies often meant manually triggering real-world processes to discover gaps in functionality or opportunities to improve workflows. If you wanted to know how quickly you could install a rivet before shifting to the next rivet point, you had to trigger the machine to rivet and shift, rivet and shift, over and over again until you felt the risk of error outweighed the benefit of additional throughput. And unless you were dedicated to watching the machine at all times, forget about recognizing long-term trends in performance.
As industrial automation embraced modern computing, building visualizations of your facility required layers of software and more coding. And even after those steps were taken, identifying trends and enabling remote visibility over your operations were still complicated affairs.
Your facility likely already has a number of PLCs or RTUs that are relied upon to monitor and control the operations of your systems. However, in many facilities, the data that is flowing through the PLCs or RTUs doesn’t flow far from the source. The data being generated is not available for remote viewing or monitoring of your processes. Nor is it being recorded to be analyzed for production efficiencies or predictive maintenance.
I should know. I started my career on the floor of manufacturing facilities, manually monitoring processes, materials, and machinery. I wish I had the capabilities offered by modern Digital Transformation hardware and software. And I’m here to say, getting started doesn’t have to be complicated — anymore.
Low-Hanging Data
When considering where to begin a Digital Transformation project, some people get paralyzed by choice. How many tags will you need for your entire facility? What data is valuable to collect? What data is not valuable and simply drives up your data transfer costs?
To return to tree-based proverbs, we often talk about “low-hanging fruit” as the thing of value that can be obtained with the least effort, and thereby the first opportunity that should be taken advantage of. I recommend you begin your Digital Transformation experience by collecting “low-hanging data.”
What is the single most important process in your facility? Do you have a new piece of equipment with “smart capabilities” that you aren’t taking full advantage of? What are your current “blindspots,” such as submerged sensors or valves that are difficult to access on a repeated basis?
As you ask yourself these questions, a single system or machine in your facility likely sticks out in your mind. Start by beginning data collection there.
Reduce the Barriers to Entry
By utilizing the free trial version of Inductive Automation’s Ignition software installed on an edge device, you can connect your PLCs or RTUs to the device via Ethernet, identify the amount of “low-hanging data” available to you from existing sensors, assign tags to each data source, and begin to build a visual model of your process.
Once you’ve built your visual models, you can begin monitoring your connected devices to provide a holistic view of your operations and begin making informed decisions based on your observations. You can also feed data to AWS or other cloud platforms to perform more advanced analysis utilizing their treasure trove of available services.
No hypotheticals. No costly consultants explaining how it should work in a conceptual future state. You have begun gaining real-world experience and value that will serve your business well as you scale your Digital Transformation. It can even help you build a case, for yourself or for your stakeholders, to expand or accelerate your transformation efforts.
All of this can be done without any software-related sunk costs thanks to Ignition's free trial model. The trial simply requires a software restart every two hours, rather than restricting your access to certain features. This allows you to prove your concepts, derive value, and gain buy-in from company stakeholders with the same feature set as the fully licensed version of Ignition.
Once you’ve decided that Ignition is right for your application, you’re able to purchase a license from an authorized integrator and apply it to your edge computer for long-term usage.
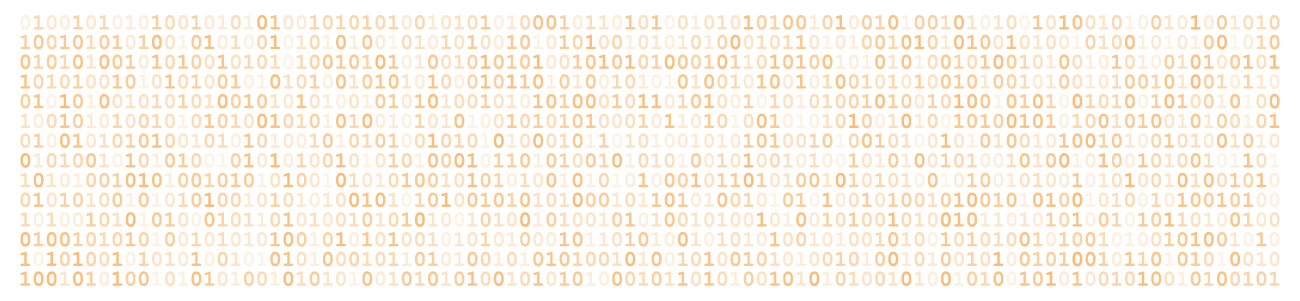
IT-Friendly
Perhaps the most infamous barrier to entry for OT professionals looking to connect their systems to the cloud are complex company IT policies. These policies are in place for a good reason, in part to restrict network connections that could be utilized to harm the business. So how do you transmit outbound data to the cloud without “leaving the door open behind you”? The MQTT communications protocol is a great solution.
Built directly on TCP/IP, the MQTT protocol allows for information to flow one way and one way only: outbound. So you’re able to feed critical data points to your remote monitoring site, server, or cloud, without accepting inbound data which may be utilized to gain access to your network by bad actors.
MQTT also has the added advantage of transmitting data in a lean, secure, and controllable format. So you’re able to save money on data transfer costs versus a constant upload of raw data.
Flexible Hardware
When you’re considering an edge device for connecting your machinery to Ignition software, you’ll want to select a system flexible enough to fit the bill for the majority of use cases. Requirements for dependable long-term operation of an edge computer in challenging locations, such as factories, outdoor enclosures, and warehouses, include:
- Wide operating temperature range
- Variable wide-range DC input
- Fanless and ventless cooling to avoid particulate ingress
- Testing for shock and vibration tolerance standards
Once you’ve determined the rugged features required by your environment, consider an edge device that offers additional capabilities to scale with you. An Ethernet connection is the extent of the I/O you need to connect to most PLCs or other OT devices. That said, serial ports and programmable DIO can come in handy for some legacy applications. And Wi-Fi and Bluetooth capabilities can be a real lifesaver for locations with limited cable runs.
Select hardware that can grow with you, and you’ll be able to utilize that initial investment to scale more quickly and efficiently when the time is right.
Phone a Friend
During the first steps of your Digital Transformation, it can be helpful to connect with an expert to get your project headed in the right direction from the beginning. Though we’ve extolled the virtues of avoiding excessive consultation phases, as they can result in long delays to beginning your project, receiving technical guidance by an experienced integrator as you walk through the first steps is a smart idea. Establish a resource and be prepared to spend an hour or so walking through the initial setup process for your data collection deployment.
Still feeling intimidated? Inductive Automation has a dedicated community of Ignition integrators who are able to provide installation, service, and guidance from day one of your Digital Transformation.
Once you’re off and running, you’ll be amazed at what you’re able to build and achieve without the need to write a single line of code.
Build Your Digital Knowledge
By completing the first stages of your Digital Transformation project, or working together with an Ignition integrator, you’ll gain real-world knowledge and experience that will serve your business for decades to come.
Increasing efficiency, quality, and quantity of output is a cornerstone of business improvement. Regardless of industry, finding opportunities to increase efficiency, predict maintenance, recognize trends, and analyze data is vital to any business seeking growth. With the right combination of hardware and software, you’ll be able to get there. By being involved in the launch, you’ll be ready to recognize new opportunities as they arise in the future.
Really, Start Now
Don’t be intimidated. Begin your transformation now. Learn how your systems operate in the real world by gaining knowledge through digital visual models. Be prepared to scale with hardware designed to scale with you. And transform your newfound knowledge into long-term business benefits. It may just be easier than you think.
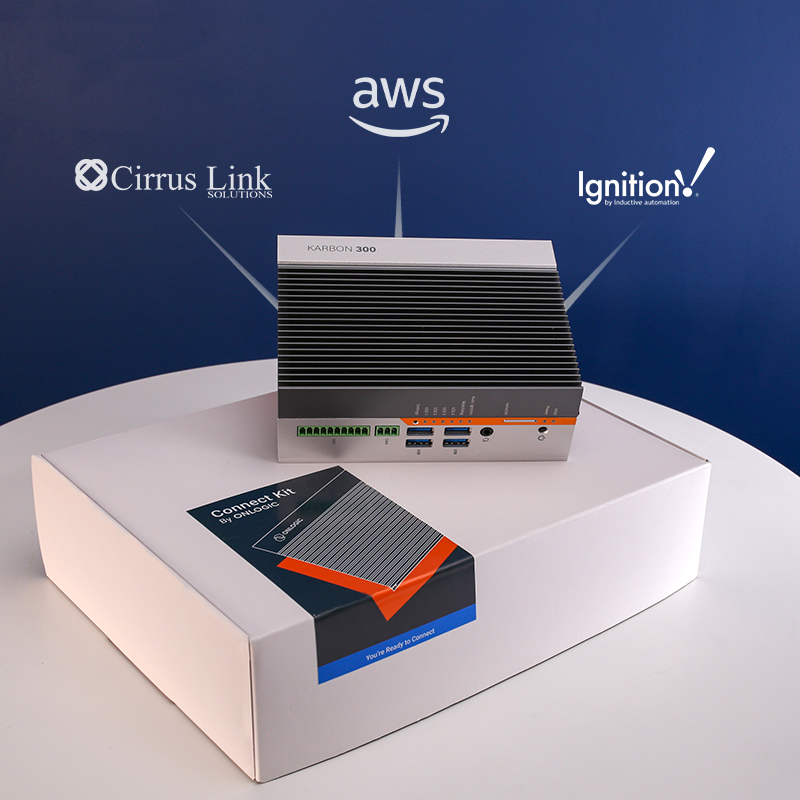
The Prologue: A Shameless Plug
If you’re looking to start your Digital Transformation, check out the Connect Kit by OnLogic. We’ve pre-imaged a custom-configured AWS IoT Qualified rugged edge computer with Ignition trial software. We then combined the system with a premium cable bundle, DIN mounting hardware, and an hour of consultative expert guidance from Cirrus Link Solutions to help you quickly and simply begin your Digital Transformation.
We recently hosted a live online event to unveil the Connect Kit. Our guest for the event, Arlen Nipper from Cirrus Link, shared some invaluable advice that speaks to a lot of what I referenced above.
“At the high-level view – it looks complex! People wonder where to start. But you don’t need to build a rocket ship to go to the grocery store. The Connect Kit brings it down to the operational level. We can help you keep it simple by connecting portions of your facility quickly and simply. The Connect Kit gives you the ability to start simply and prove immediate value in the real world. No coding required,” says Arlen Nipper, President and CTO of Cirrus Link Solutions.
The Connect Kit is based on a hardware and software stack that has been used to connect Fortune 500 companies to the cloud and begin their Digital Transformations. Now you can get everything you need to begin your Digital Transformation in one box from OnLogic.