How Meister Cheese Uses Ignition to Streamline its Manufacturing Operations
6 minute read Download PDF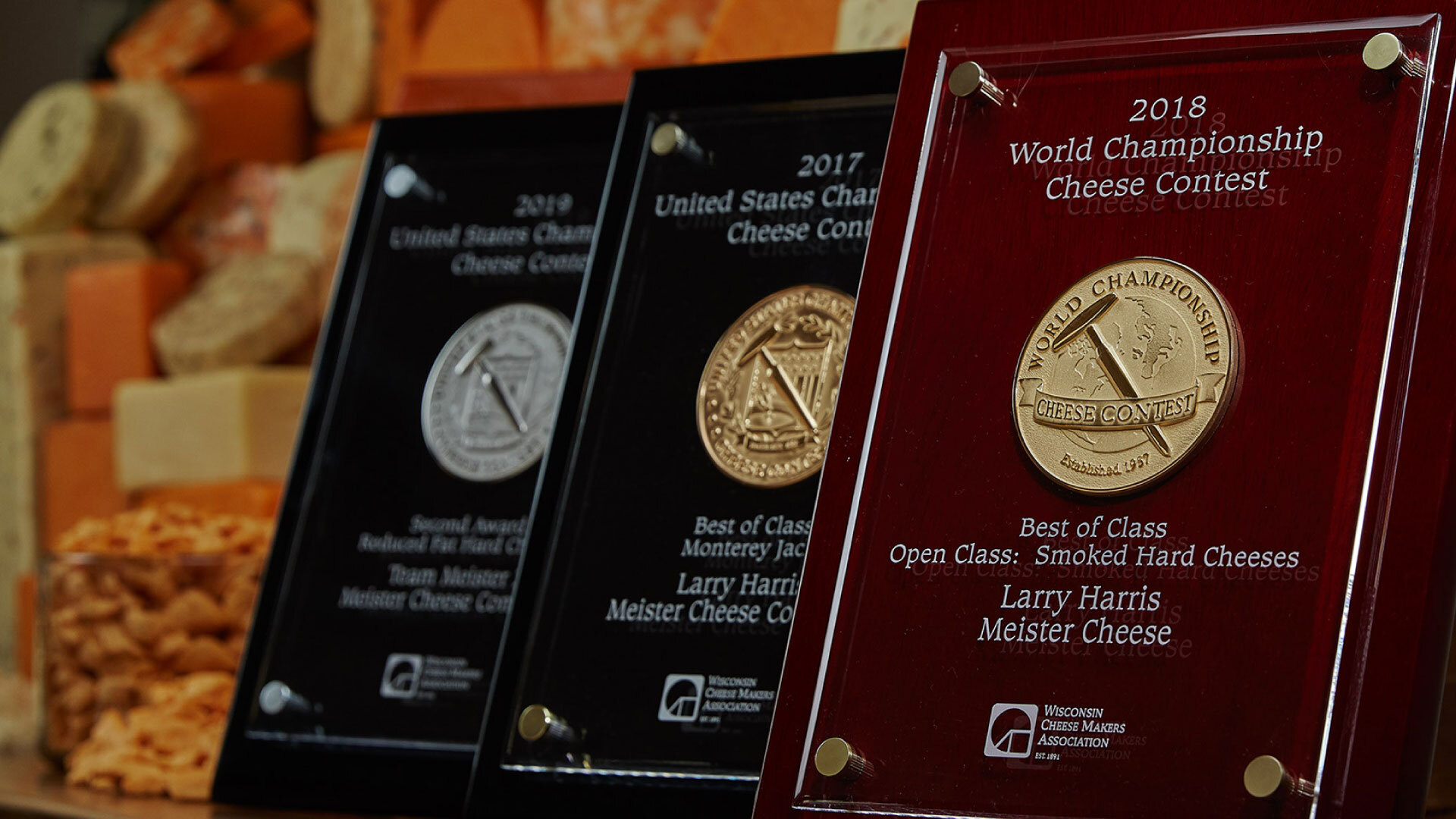
Meister: Outstanding Cheese Made with Great Care
Meister is an award-winning cheesemaker in Muscoda, Wisconsin. The company has been in business since 1916 and is currently in its fourth generation of family ownership and leadership. Over the past 100 years, Meister has grown into one of the top makers of premium cheese and whey products in the world.
Meister partners with Wisconsin dairy farmers who combine the best traditions of farming with the best animal husbandry practices. Each year, Meister converts 225 million pounds of milk into final products.

Evolving Customer Requirements
Even though Meister has established a trusted reputation as an outstanding cheese-maker, over time, customers have increasingly desired more information from manufacturers. Customers want information about product quality, traceability, security, and transparency.
In order to satisfy customers and retain the trust that Meister has built over the years, it is important to be able to show customers that Meister’s outstanding products are manufactured through consistent, high-quality, data-driven operations.
Automating Manufacturing and Data Collection
Like many manufacturing companies, Meister realized it needed to automate aspects of its operations. This led Meister to automate the majority of its cheese-making and whey processing operations, tightly integrating the operations to be recipe-driven and supply-oriented yet flexible enough to accommodate daily changes in customer orders.
In conjunction with automating its operations, Meister found it necessary to increase the depth and accuracy of the information gathered. Initially, Meister tracked this data manually, using Excel. However, this process was slow and time-consuming, and it was difficult to produce reports and conduct audits. Traceability of the manufacturing process was completed using forms and paper logs.
The company’s forward-thinking director of operations, Larry Harris, realized that Meister’s manual data collection processes were not adequate. To deliver on customers’ need for consistent and outstanding product quality, he championed automating the data-collection process and having a central platform to aggregate all operational data.
In particular, Meister wanted to be able to automate collection of batch-level data, which is more complex than time-sequence data, with event-driven PLC triggers to initiate new lots and batches, without increasing the workload for its operators.
Implementing Ignition
To achieve the vision of a centralized platform, software engineer John Fingerson recommended Ignition, an industrial application platform from Inductive Automation. Prior to joining Meister, John had worked for a system integrator where he had been introduced to Ignition. When first introduced to Ignition, John had been skeptical. He had been a programmer for a long time and had seen numerous products, most of which didn’t live up to expectations. But Ignition was the exception. He found it to be a very cohesive product that was simple for developers to use. Based on his previous experience, he thought it was the perfect solution to meet Meister’s needs.
Initially, Meister was already using Wonderware for its control screens but started using Ignition for more data-centric purposes such as gathering data about batches. For example, for each batch Ignition could track information about a host of parameters such as the times when the batch started and ended, the exact recipe used, and the temperatures. Based on the positive experience with Ignition, Meister decided to replace all of the control screens with Ignition throughout both the cheese and whey plants.
“I think where Ignition excels is that the platform was built to be data centric.” John Fingerson, Software Engineer, Meister
How Meister Is Using Ignition
After initially using Ignition to gather automated batch-level data, Meister has now completely converted its manufacturing operations to Ignition.
The manufacturing processes on Ignition include:
- Milk receiving
- Microfiltration
- Pasteurizing
- Cheese vats
- Cheese tables
- Cheese towers
- Bulk packaging
- Retail packing
- Clean in place (CIP)
In addition, Meister is using Ignition to report on and augment its inventory management system with mobile Android barcode scanners, to automate the transfer of data from a variety of different LIMS (laboratory information management system) systems directly into its batch data, and has used Ignition to enter, track, and report on environmental quality data.
Meister’s platform now has more than 50 active clients, including clients on the manufacturing floor to monitor and control processes and clients in the company’s offices. Meister has separate control screens for each of the different processes in the plant. An example is shown below.
In reflecting on the importance of Ignition to Meister, John said, “Everything in our plant is being run off of one moderately-sized server ... I still haven’t found anything that I can’t do with Ignition simply and efficiently.”
Features and Benefits of Ignition
Meister depends heavily on Ignition for its online recipes, forecasting, scheduling, lot traceability, reporting, SPC charts, historian, and auditing. In Meister’s experience, the most important features of Ignition include:
- Having a single platform for machine control, data entry, scheduling, and reporting. Many of Ignition’s benefits flow from automatically aggregating data into a single platform. This is in contrast to a collection of disparate programs by multiple vendors or even the same vendor.
- Having the ability to access, visualize, and share data. Built-in features such as the historian, auditing, ad hoc graphing tools, and dynamic user controls minimize designer time and enhance the user experience. This is because users can access, visualize, share, and manipulate data through filtering, sorting, column hiding and rearrangement, exporting, and printing—all with minimal user effort.
- Being server-based. Since all clients are run from a single server, it is possible to make one change on the server then push it out to every client.
- Increased efficiency. Meister is able to gather and analyze 10 times the amount of data it had before without increasing staffing. At the same time, due to the information and visibility that Ignition provides, it has made it easier for operators to do their jobs. Also, as a developer, John says that Ignition allows him to do his job 50% to 75% more efficiently.
- Accessing Ignition via mobile phones. Using the Ignition Perspective Module, it is possible to access Ignition remotely from a mobile device and implement modern Android hand-held barcode scanners.
- Ignition’s licensing model. Meister likes Ignition’s licensing model, which through one license allows Meister’s plant to have unlimited clients, tags, and developer stations.
“If you’re looking for a platform to manage and display data efficiently, those are the strengths of the Ignition platform.” John Fingerson, Software Engineer, Meister
Ultimately, the most important benefit is that Ignition enables Meister to deliver the transparency and traceability that their customers desire. Ignition builds even greater trust with customers by providing data to demonstrate the most important details of Meister’s manufacturing processes and product quality.
To learn more about Ignition, click here.
This case study is presented in collaboration with ProFood World.
Want to stay up-to-date with us?
Sign up for our weekly News Feed.