Driving Efficiency and Visibility at rPlanet Earth
Combination of Kanoa MES and Ignition Creates Foundation for Smart Manufacturing
7 minute read Download PDF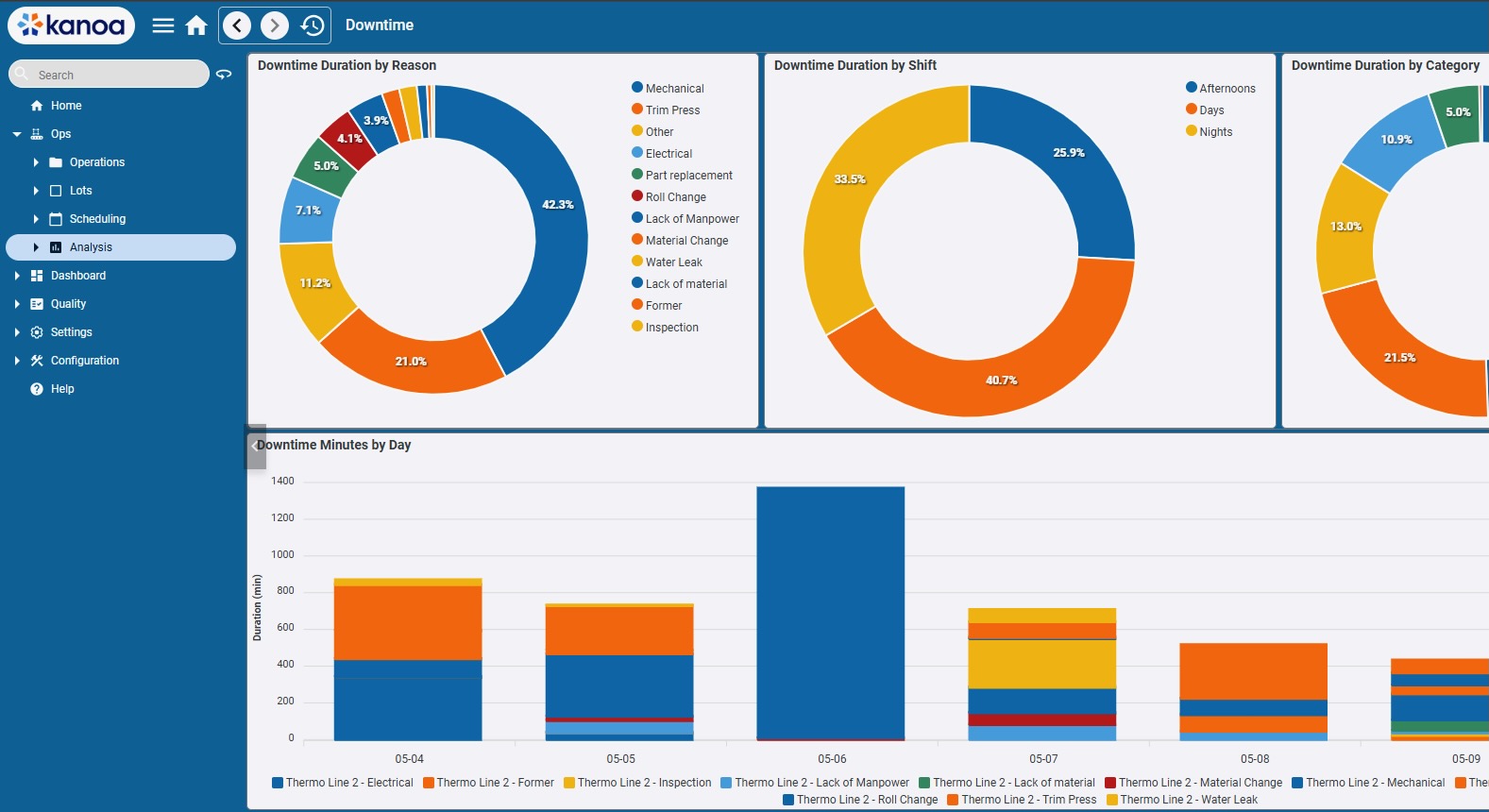
rPlanet Earth sets itself apart from traditional recycling facilities through its fully integrated recycling and packaging plant located in Vernon, California. Their innovative 300,000-square-foot facility uniquely combines recycling and manufacturing processes under one roof. Unlike conventional recycling plants, which typically involve multiple locations and intermediaries, rPlanet Earth directly transforms curbside-collected post-consumer PET into FDA-approved, food-grade packaging products. This streamlined approach enables the company to produce sustainable products such as Enviro Cup® cold drink cups, Enviro TF™ containers, Enviro PF® preforms, and Enviro PET® roll stock — using up to 100% recycled content.
By consolidating these processes, rPlanet Earth achieves significant operational efficiencies and environmental benefits. Their integrated model drastically reduces greenhouse gas emissions — 22% fewer compared to conventional rPET products and 60% fewer than virgin PET. This operational excellence aligns closely with their overarching mission of sustainability, pushing them to continuously innovate and enhance the efficiency of their plant operations.
Striving to continue this approach of operational efficiency, rPlanet Earth partnered with Kanoa to implement Kanoa MES — a modular, composable manufacturing execution system built specifically for Inductive Automation’s Ignition platform. Ignition is an industrial automation platform for SCADA, MES, IIoT, and more, widely adopted for its ability to connect, visualize, and manage industrial systems through a unified and extensible architecture.
Manual Systems And No Visibility
Before implementing Kanoa MES, rPlanet Earth relied on siloed, manual systems. Production data was recorded using paper logs and Excel spreadsheets. The process was time-consuming, error-prone, and limited the organization’s ability to drive continuous improvement.
More critically, there was zero visibility into what was being produced on each line or how lines were performing. Supporting departments such as Supply Chain, Warehouse, and Quality had no real-time insight into the plant's operations. Managers often had to physically walk the floor just to find out what was running.
To solve these challenges, rPlanet Earth needed a solution that could:
- Seamlessly connect to real-time equipment data
- Provide user-friendly interfaces for manual input
- Automate data processing and visualization
- Eliminate redundant entry and support better decision-making
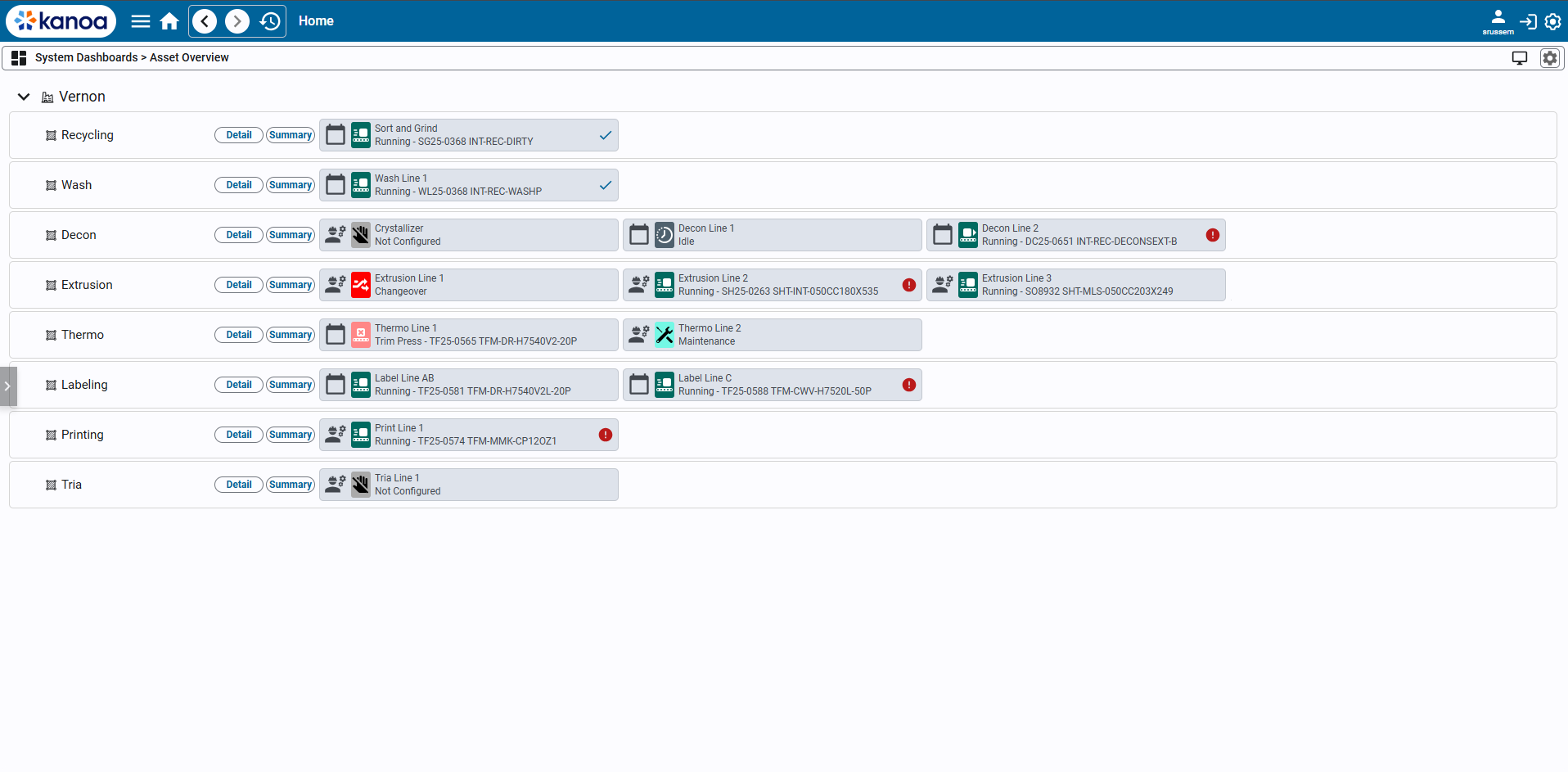
A Central Data Platform With Kanoa And Ignition
Kanoa MES is engineered to harness Ignition’s powerful capabilities and bring them to life in manufacturing environments through its integrated solutions: Kanoa Core, Ops, Trace, and Quality. This deployment at rPlanet Earth began with Kanoa Core and Ops, providing the foundation for a centralized operations management system. Kanoa Core delivers essential services like user roles, navigation, and language support, while Kanoa Ops enables real-time tracking of production performance, machine utilization, and material consumption. Together, they established a flexible, scalable data infrastructure — capable of transforming raw machine data into meaningful, actionable insights for continuous improvement.
The Ignition platform provided robust integration with plant-floor PLCs — including those from Siemens and Allen Bradley — and with rPlanet’s ERP system, Vicinity. Ignition Perspective’s mobile-responsive screens enabled user-friendly data input via desktops and tablets. Although Ignition had previously been used at rPlanet Earth for building and utilities trending, this deployment marked its first deep integration into core manufacturing operations. With Kanoa MES layered on top, Ignition became the foundation for real-time communication and decision-making across the plant.
Kanoa Ops acted as the central hub for production data, tracking machine performance, downtime, waste, and materials usage — all structured by Batch Ticket (Production Order). The system automated scheduling, OEE calculation, ERP reconciliation, and real-time dashboards, delivering role-specific insights to every level of the organization.
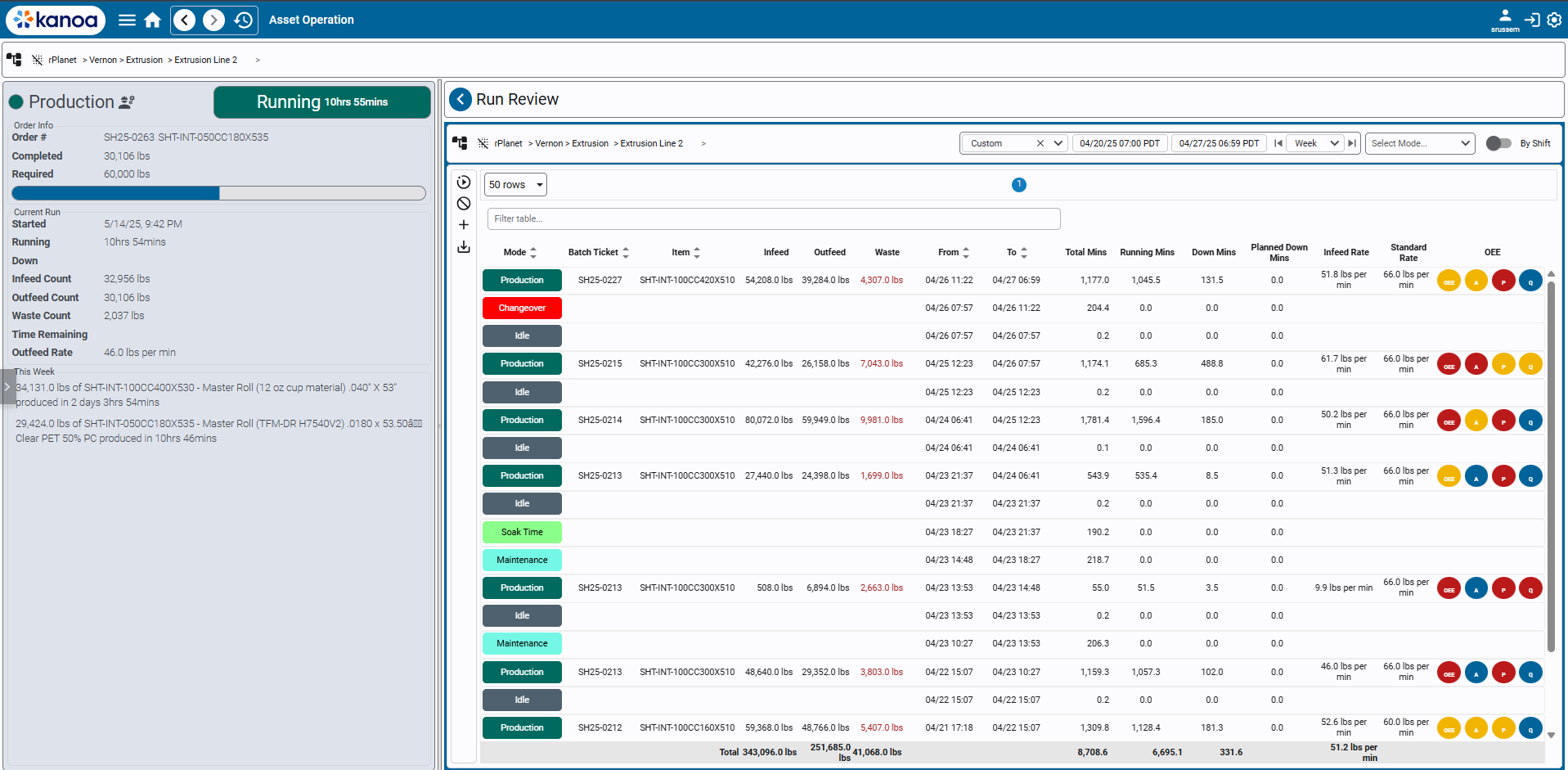
From Pilot To Plant-Wide Adoption
Kanoa MES was deployed to an on-premise Ignition gateway, connected to a Microsoft SQL Server database. The rollout began with a focused proof-of-concept on three extrusion lines, selected for a number of strategic reasons: these lines already had some machine connectivity in place, allowing for automated data collection. They were also operated by a highly knowledgeable team that, while very busy, was ready and eager to collaborate, helping the Kanoa team identify opportunities where software could streamline or automate key processes. Operator engagement and feedback played a critical role in shaping the implementation.
Importantly, the extrusion area was also a point in the production process where improving data accuracy and timeliness would have meaningful downstream effects. For example, processes like thermoforming depend on extrusion data to proceed, meaning any delays in manual entry could slow overall throughput. The decision to begin here created an ideal environment to validate the system’s value and lay the foundation for broader adoption.
The pilot deployment of Kanoa Ops enabled rPlanet Earth to:
- Monitor each line’s state, work order, item, and performance in real time
- Initiate and close production runs
- Automatically log infeed material
- Track and validate downtime events
- Generate end-of-shift and batch reports for ERP integration
One standout innovation born out of the pilot was the Smart Scale project — a direct response to inefficiencies experienced by extrusion operators. Previously, recording the plastic sheet rolls produced was a highly manual, repetitive process involving standalone scales, handwritten notes, spreadsheets, and redundant ERP data entry.
The initial deployment of Kanoa MES improved this process by replacing Excel with structured, validated forms that automatically generated metadata like shift, material, and roll naming. But the team took it a step further.
rPlanet Earth implemented a fully integrated Smart Scale solution using off-the-shelf, hardware-agnostic components connected to Ignition and Kanoa MES:
- A network-connected smart scale that automatically captures roll weight
- A Samsung Android tablet running Ignition Perspective, allowing operators to quickly select the Extrusion line and roll status (good or scrap, including reason codes)
- A Zebra label printer that prints QR-coded labels in real time for each roll
This enhanced workflow:
- Eliminated all manual data entry
- Created a real-time data pipeline from scale to MES to ERP
- Reduced errors and lag time
- Enabled better visibility and responsiveness from both operators and management
It’s a prime example of how rPlanet Earth is using Kanoa MES not just as a reporting tool, but as a platform for operational innovation and continuous improvement.
Following the pilot's success, Kanoa MES was expanded to 14 lines across the plant — giving operators and managers one unified, real-time platform for production control and analytics.
From Data Gaps To Total Operational Insight
The implementation of Kanoa MES and Ignition didn’t just change how data was collected, it transformed how the organization operated. Conversations that began during implementation led to standardizing processes, aligning floor practices with management expectations, and uncovering previously hidden inefficiencies.
By actively involving operators and engineers in the rollout, rPlanet Earth fostered a culture of collaboration and continuous learning. The result was rapid adoption, improved transparency, and measurable gains across the facility.
Linda Veliz, Process Integration Manager at rPlanet Earth and key stakeholder for the Kanoa MES project, has been impressed by how the Kanoa MES has been able to adapt to rPlanet’s unique requirements: “Kanoa MES provides us with a personalized solution, customizing its system to meet the unique needs of our plant. As our processes evolve, so does the Kanoa system — adapting in step with our growth. The Kanoa team works closely with rPlanet to develop solutions that enhance both data collection and accuracy. Over the past year, Kanoa has transitioned our data collection from scattered Excel spreadsheets to a centralized, integrated system. This flexible platform supports a hybrid approach, combining both manual and automated data entry to suit our operational requirements.”
Key Results:
- 18% increase in inventory accuracy due to more reliable, automated data
- Standardized operations across 14 production lines using Kanoa Ops
- Real-time plant visibility via universal dashboards accessible to every department
- Reduced admin overhead, freeing staff to focus on process improvements
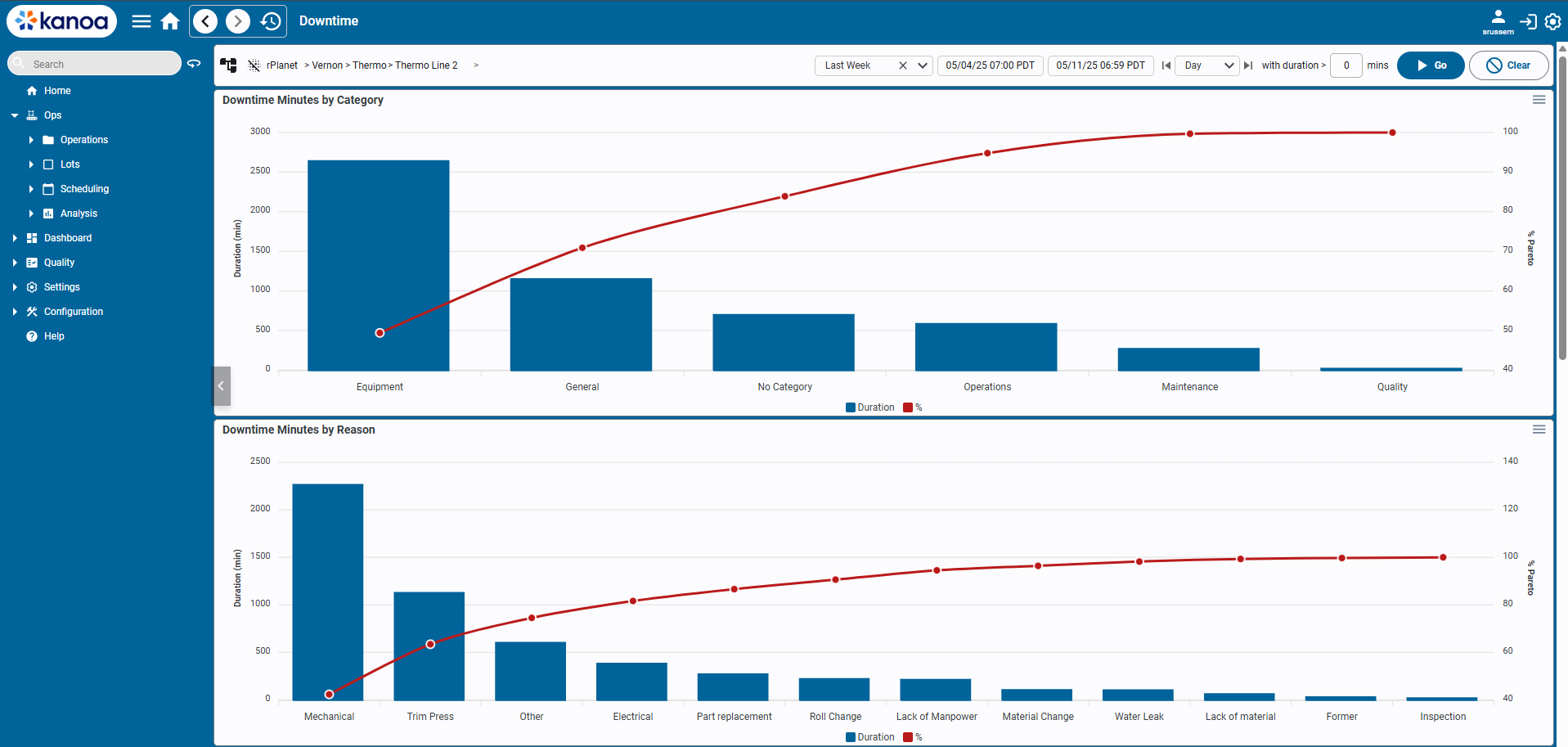
Future Enhancements
In 2025, rPlanet Earth will continue its digital transformation by implementing two additional modules of Kanoa MES: Kanoa Quality and Kanoa Trace.
Kanoa Quality will integrate quality checks directly into the manufacturing workflow by leveraging real-time data from Kanoa Ops. For example, when a new production run is initiated, the appropriate quality checks will be automatically triggered — ensuring critical validations occur at the right time, without manual coordination.
Kanoa Trace will establish full end-to-end material traceability across the plant. By tying together raw material inputs, machine data, production parameters, and quality results, rPlanet Earth will gain complete visibility into how every end product was made. This enhanced traceability supports compliance, accountability, and faster root-cause analysis, elevating both product quality and customer confidence.
A Foundation for Smart Manufacturing
Kanoa MES has helped rPlanet Earth modernize its operations, unify its teams, and make smarter decisions with real-time data. What began as a pilot project has evolved into the backbone of a fully connected, insight-driven manufacturing operation.
By eliminating guesswork, increasing visibility, and supporting continuous improvement, Kanoa MES has become more than a tool — it’s a core part of how rPlanet Earth runs its business.
Project Scope
- Start date: December 2023
- Deploy date: March 2024
- Tags: 846
- Screens: 581
- Clients: 20
- Alarms: 0
- Devices: 20
- Architectures: Basic
- Databases: 1 Microsoft SQL Database running the KanoaCore database
- Historical data logged: 50 tags for trending
Project Information
Project For: rPlanet Earth
rPlanet Earth is a leader in sustainable packaging solutions, specializing in high-quality products made from recycled materials. By eliminating steps in the traditional plastic recycling process, rPlanet Earth creates higher-quality rPET products that produce 22% fewer greenhouse gas emissions than conventional rPET preforms.
Want to stay up-to-date with us?
Sign up for our weekly News Feed.