Industry Panel: Driving Innovation and Transformation in Industrial Organizations
49 min video / 41 minute readSpeakers
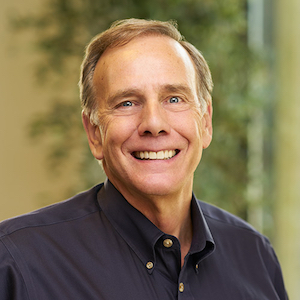
Don Pearson
Chief Strategy Officer
Inductive Automation
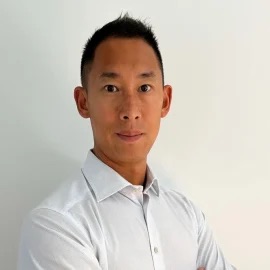
David Lam
Business Development Director
Vertiv
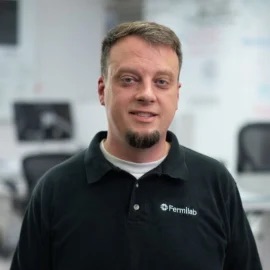
Trevor Nichols
Senior Engineer
Fermi National Accelerator Laboratory
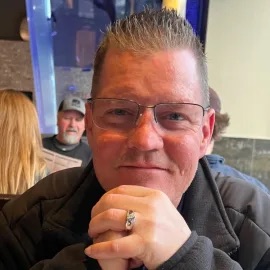
Daniel Stauft
Director, Operational Technology
SugarCreek
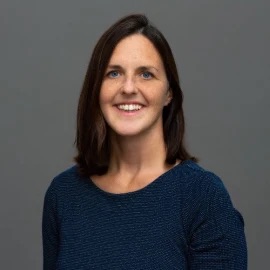
Rebecca Gillespie
Managing Director
Energy Systems Network
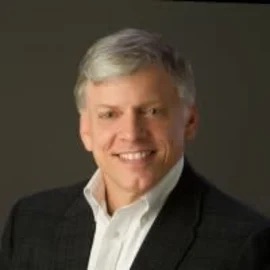
Dick Willis
Shopfloor Digitization Leader
Trane Technologies
Hear from a panel of industry thought leaders and experts as they explore how utilizing data and technology can inspire new ideas, open new opportunities, and drive digital transformation efforts in industrial organizations.
Transcript:
00:04
Don Pearson: So welcome everyone to our panel discussion with the Industry Panel today. The focus is innovation and transformation in industrial organizations. And I think we got a really good panel. I had a chance to meet with them all yesterday and today, and just to get a little sense of what kind of things we're gonna cover. So I really appreciate the opportunity to be the moderator today. My name is Don Pearson. I'm with Inductive Automation, and this is always one of my favorite panels of the conference. First thing I'm gonna do is introduce each of the panelists, and then I'll go back through and have them each give a real better introduction of themselves and a little bit about their company and what they do and how they're actually engaged with Ignition inside their various activities and organizations. And then I have a bunch of questions.
00:50
Don Pearson: We have some seed questions and things, but we also have runners. And really it is your opportunity to ask questions of any panelists. I also noticed in our discussion yesterday, some of the panelists started asking each other questions, so that's open, fair game for that too. Just wanna make this interactive and really a useful time for you to sort of see what they're up to and how it may relate to some of what you're involved in. So first off, I'm gonna start to my right and introduce David Lam. He's the Business Development Director of Vertiv.
01:21
Don Pearson: He's a motivated and detail-oriented professional and a strong communicator and collaborator who thrives in dynamic environments. He has a passion for innovative solutions, a solid sales and business development background in EPMS, automation and control systems, and two years of Ignition experience. His dedication to continuous improvement, learning, and growth has helped him foster strong team dynamics and networks, and he's excited to see how his industry transforms through innovation. So please help me welcome David.
02:00
Don Pearson: And to his right is Trevor Nichols. He's an Electrical and Controls Engineer at Fermi National Accelerator Laboratory, where he designs and supports control systems for the cryogenics on particle physics experiments. Inspired by best practices found in industry and other laboratories, he developed a library of function blocks for PLC programs with corresponding UDTs, templates, and popups for Ignition, providing an object-oriented framework for control systems design. This approach has been implemented on newer experiments that employ sophisticated liquid argon cryogenic systems to study neutrinos. Now, I learned a little bit about neutrinos earlier today with Kevin. Maybe some of you already knew all about it, but we learned a little bit about it earlier today. It's a class of elusive fundamental particles, and it was a presentation as a Firebrand Award winner that was talked about earlier. Very glad to have you on the panel. Welcome Trevor.
03:01
Don Pearson: To his right is Dan Stauft. He's the Director of Operational Technology for SugarCreek. He spent the first 21 years of his career in manufacturing engineering for automotive assembly plants where he specialized in process automation, data visualization, and analysis. In 2013, Dan was hired by SugarCreek. It's a large privately held food manufacturer, and he was hired to lead their Digital Transformation. Over the past 10 years, Dan has led a team of engineers who utilize Ignition to enable decision makers access to real-time production data and historical analytics. In 2017, SugarCreek won a Firebrand Award for their initial MES project, which monitored six manufacturing sites. Currently, SugarCreek has over 20 Ignition gateways and edge tag providers that monitor over a quarter million tags and host over 30 projects utilizing both Vision and Perspective. All of SugarCreek's Ignition development has been done and completed in-house underneath Dan's leadership. Please welcome, Dan Stauft.
04:12
Don Pearson: And to his right is Becca Gillespie. She's been the Managing Director for Energy Systems Network since 2023. Prior to that, she worked as the New Products and Services Lead at Duquesne Light Company, the electric utility for Pittsburgh, Pennsylvania. Before that, she was Sales Director and Product Manager at UniEnergy Technologies. It's a low battery startup in Washington. She was also an Energy Analyst at the Federal Energy Regulatory Commission, and a Production Engineer at NASA. Becca has a Bachelor of Science and Engineering degree in Mechanical and Aerospace Engineering from Princeton University and a Master of Science degree in Public Policy and Management from Carnegie Mellon University. She also holds a patent for a nitinol valve for in-space propulsion systems. So please welcome Becca.
05:12
Don Pearson: To her right is Dick Willis. He was educated and trained for 30 years to be an industrial software tool builder from PLC-based control systems to OEE monitoring systems to full-stack MES in an automotive factory. He helped create the OEE software engineering services company after that. The software platforms they use range from RSLogix, Visual Basic, Wonderware ArchestrA, .NET, and now Ignition. He points out that he's not yet certified but working on it. So that's good. Thanks. But working on it. At Trane, his responsibilities include connecting legacy equipment to their data network and creating tools that collect, monitor, alert, and notify and escalate to reduce the amount of time spent searching for data so that the time can be spent problem solving and making changes instead. Please help me welcome Dick.
06:10
Don Pearson: I do wanna start by, I gave an introduction to a little bit of their backgrounds, but I've asked each of them to talk a little bit about what they do, where they work, and how they're involved with Ignition, and there's a lot of people at different states of the journey, and I was really pleased also when Becca could join us because she works in the public sector, but they work with a lot of manufacturers in Indiana and I'm very excited about the program they're doing. There's another session on it. You'll be with Benson, I think tomorrow, but we got a variety of talent here. So with that, David, I'm just gonna start left again and give you an opportunity to talk a little bit about what you do, what you're excited about it, how's it innovative, how's Ignition fit into it?
06:51
David Lam: Sure, sure. So good afternoon everybody. So David Lam from Vertiv. Originally, I spent, prior to my time at Vertiv, I did 10 years at Schneider Electric in the software business and Ignition was a very, very big, it still is a very big competitor to Schneider. So I came over to Vertiv to see what this is all about as they've been using it for the last five years. So Vertiv is a OEM manufacturer of MV, LV, and bus duct electrical equipment. And as part of that, I lead the BMS and EPMS controls and automation business globally. So we primarily deliver into enterprise and data centers. So we take everything from the source, i.e., renewables and utilities, and we deliver all the manufacturing switch gear into data centers. And then we overlay the BMS and EPMS solutions on top of that to essentially make the invisible visible so we can control, analyze reports. And we predominantly use Ignition now as our go-to platform.
08:09
Don Pearson: Good. Thanks. Good introduction there. Trevor.
08:12
Trevor Nichols: Hello. I'm Trevor Nichols. And so I work at Fermi National Accelerator Laboratory, which is United States' most prominent lab for particle physics research. So my background is in electrical engineering. So before I came to the lab, I actually worked in aerospace for 10 years working on electronics for the Boeing 787. So then I came to the lab as a controls engineer. And so I work on control systems for the cryogenics, primarily on our neutrino experiments. About five years ago, I was introduced to Ignition because it was used on a dark matter experiment that a colleague of mine was collaborating on.
08:58
Trevor Nichols: So when the pandemic came along, we all got sent home to work remotely and there was sort of a lull in our work. And so that was when I really got to work on trying to build something that I'd be able to use across multiple experiments. So I started building libraries both for our PLC code and on the Ignition side. So a function block instance on the PLC corresponds to a UDT instance in Ignition, and those are strictly one-to-one. And so this library, this framework for developing control systems, I've now been able to implement it on three experiments, and we have a couple more on our roadmap. So I'm looking forward to using it on a even bigger project.
09:42
Don Pearson: Great, Trevor. Thanks. Dan.
09:45
Dan Stauft: Hi. Dan Stauft. Excuse me. Happy to be here. You know, as Don said, for the first 21 years of my career, I was with General Motors Toyota Nissan, which has been doing what we're doing, you know, for the past 30 years. And learned about lean manufacturing, data collection analytics. As he said, I joined SugarCreek in 2013, and quite frankly, they didn't have a job title for me. They just knew that I could do something. So my first job was to write my job title. Shortly thereafter, we were looking for a machine data collection system and I had 10 different, Don loves this, I had 10 different applications we were looking at, none of which were Ignition. Wonderware came in and gave us their spiel. We asked how much it would cost, they said, "Two million bucks."
10:41
Dan Stauft: We said, "Haha, no thanks." And they said, "Well, if you can't afford us, there's this little startup in California that you might want to consider," and the rest is history. Our first project was an MES project. We put six sites on MES, I forget how many lines it was. It was around 20 lines. That took one person that was me and we tripled our OEE in two years. And it wasn't Ignition that tripled the OEE, it was Ignition plus a continuous improvement group, which composed of one guy who went to all of our sites and taught them how to identify opportunities, break down problems, identify solutions, implement countermeasures. So that pretty much paid for itself. I mean, I think that probably would've paid for Wonderware. When I joined the company, we were doing around 300 million in sales. Last year we did 1.2 billion in sales, and that was not through growing plants. Some percentage of that, probably 30% was growing plants. It was from our OEE improvement and tripling our capacity.
11:55
Don Pearson: That's great. And just a point for you and for David. You guys, they are wearing Ignition socks, so they get extra credit for wearing their socks today. It wasn't a requirement to be on the panel, okay?
12:07
David Lam: They match my shoes.
12:10
Don Pearson: Becca.
12:10
Becca Gillespie: Right. Thanks Don. Yeah. Thanks everyone. Yeah. I work for Energy Systems Network and we're a consulting shop that works, as Don mentioned in the public sector working with the state of Indiana to help them implement energy-related projects. The particular program that brought us to working closely with Ignition is called Energy Insights. And the purpose of that is kind of dual goal. On the one hand, it wants to help small-to-medium manufacturers just take that first step into their digital journey and start that first pilot program. We happen to say that pilot program should hopefully have something to do with energy, but we really let them be a little bit free there. And then the second goal is to expose them to their energy consumption and start them understanding how they may be able to use energy efficiency measures or data collection measures to improve their energy... To decrease their energy consumption.
13:07
Becca Gillespie: We do that with... We give each of these manufacturers basically hardware, which is our partner, Opto 22, which I'll be speaking with tomorrow, software, which no surprise is Inductive Automation. And then about half of the grant goes towards time with an integrator because we understand small-to-medium manufacturers can't necessarily use something out of the box. Everyone's processes are so unique that they actually need time with that integrator to develop it. And so basically the goals at the end of the program, what the state wants from each of these, is that they just have the capacity to take the next step in their digital journey, whatever shape that might mean. So we just want them to see that ROI so they can say to their boss the next time they want to actually pay for it themselves, "Hey, look at this pilot project."
14:04
Becca Gillespie: "Here's something we did and it had an ROI and now can we invest in the next opportunity?" And we also want them to get that sort of on-the-job training, which in Indiana's opinion, is kind of the best way to train a manufacturer. By letting them do a thing. So that basically brought us to Inductive Automation. I mean, there's a lot of software out there that can take energy data and zoink it to the cloud and give you energy dashboards, but that's not what we wanted. We wanted something that was scalable, modular, reconfigurable, all the buzzwords to say that, you know, this is your beginnings of your smart manufacturing platform, and yeah, you're starting with energy, but you can do anything. So we thought Inductive Automation is a great fit for small-to-medium manufacturers and it's a great fit for being scalable. And that's really what we wanted to give them to get started.
14:58
Don Pearson: That's great, Becca. Okay, over to you.
15:00
Dick Willis: Yep. About five years ago is when Trane Technologies divested from Ingersoll Rand and there are 50 factories. I work for the residential and the Thermo King factories now, and what we inherited was each of the factories had a wide range of thickness of their SCADA layer. Some machines were still not connected to the network. Some of the engineers on site did have Ignition skill sets and built some pretty significant things. One of our sites had a Ignition developer who'd been doing it, you know, for 10 years and it was his full-time job. Most of the other sites didn't have that experience, though they had an engineer who was dabbling in Ignition on-the-job training, did it as he, you know, found, you know, time and availability. But even then, in the first couple years of that development, we had some really good successes.
15:48
Dick Willis: We put in Sepasoft to two of our plants to monitor OEE. We then let the engineers develop their own faceplates for some of their equipment. And one of the... And there are two successes that came to mind, where in one of our machines was monitored by Sepasoft, the operators were putting in notes about what was the problem with the downtime. And one operator was pretty fastidious about that. And she was putting notes that says, "I'm down because I don't have any empty carts to put my material in when I'm finished." Nobody knew that. And all of a sudden we realized that a lot of these issues that we were running into and nibbling at us were productivity and keeping our OEEs low, were things we could easily solve. We just hadn't seen it. So again, making the invisible visible is a big part of it.
16:32
Dick Willis: And same with one of our sheet metal stamping presses. An engineer made a faceplate for himself to keep track of what the photo eyes were doing over time. Realized that again, one of his outages that was eating his lunch on that machine was because a photo eye was tripping a little bit earlier than everybody thought when they wrote the PLC program. He fixed the PLC program, availability went back up, and all of a sudden we're heroes. So we had really good local success, and we were getting more and more need for Ignition, but we didn't have enough local, you know, site developers. And we're still struggling with that. Our journey is now to go past, just thicken. We wanna uniformly thicken our SCADA layer so that everybody has OEE that's geared towards problem solving. To Dan's point, it's not just OEE the number, it's what it feeds to your problem-solving team.
17:21
Dick Willis: That's the key. You know, we don't pretend that having an OEE system gets you better numbers. You have to have OEE system that's credible that your people will then use. And then we also have a SCADA community that we're building. We have a SCADA governance team that we're building. So again, we can all have uniform capabilities. One of the important things we talked about this morning in the keynote was the value of this community. This is one of the reasons why I think we made a good choice when we picked Ignition for Trane Technologies, is because of the breadth of the community and all the help that we're currently getting. Now, our main challenge is to take this monitoring system, which has been showing a lot of good local results to make it uniform across all of our plants, and then take advantage of the alerting and notification capabilities to say, "I don't want you to watch the screen. I want you to go do your work. The SCADA system will tell you when the pattern you're looking for is a problem. So do your work and let SCADA help you as much as it can." So we expect that that's gonna yield even better results for us in a very short period of time once we get that uniform layer developed.
18:26
Don Pearson: Great. Thanks Dick. I think I'm gonna start with the questions. Maybe come back to you Becca. 'Cause yours is a little bit unique also. Many people already know this, but I learned it when I started going to Indiana when the program was first getting started. There's almost... Is it approaching 10,000 individual manufacturing companies in the state of Indiana? Yeah. Kind of a busy place.
18:48
Becca Gillespie: I don't know how you measure it. Yeah.
18:51
Don Pearson: But why small and medium business? We talk a lot about the first step, the journey, and Travis and Kevin were talking about the sophistication levels of deployments that you start someplace and you wanna go somewhere. Tell a little bit about why the target of the small and medium business, how it's going, what are some of the challenges of getting that entrance point going with those folks?
19:17
Becca Gillespie: Yeah. I think the entrance point for small-to-medium manufacturers, I mentioned a little in my intro, but it's a real one. It's that first cost hurdle. It's that ability to describe to a CEO of a company that's been running and running well for 50 years and manufacturing parts well for 50 years that looking at data can help them save money. That can be really difficult to explain. It can be difficult to articulate without a lot of hand-waving. And so the state says, we see the writing on the wall. Smart manufacturing, SCADA systems, data collection, this will keep you competitive. A lot of people within the small-to-medium manufacturers also see the writing on the wall. This is what's gonna keep us competitive. But they have a hard time getting that first investment and getting people to sign off on this kind of difficult-to-explain-and-it's-different-in-every-plant value proposition of data visualization, data analysis, and then, again, notifications. It's hard to know what those gem of a use cases are gonna be until they've happened. So that's one thing. But it's more than just money. I think a different problem in the small-to-medium manufacturers is that information gap.
20:31
Becca Gillespie: It's a very busy space out there. I understand that, frankly. I feel like I'm the filter for them of all of the IIoT and software and SCADA solutions that are there. And I feel that burden on myself, and I'm glad that I can take that off of their shoulders for this first implementation, 'cause there's nothing better than getting your hands dirty, starting a project, getting the pilot going, and building from there, especially with a reconfigurable or open platform like Inductive Automation that you can continue to use in some ways and bring on other pieces. But that's the beauty of it, that they don't have to dig into the world of all of the vendors at first. They can just get started with something. So we think that's a really good one. And then they also have the issue of they're starting to... Need to understand their energy, 'cause energy prices are going up. A lot of big manufacturers are levying greenhouse gas requirements on them, and they definitely don't know where to get started.
21:37
Becca Gillespie: It's coming from above. They hear this new accounting principle is now greenhouse gases, and they can't necessarily measure it. So they get this feedback, and the Indiana state says, "We wanna help you with this. We know this is important. We know it's hard to justify. We know it's a difficult space to get started in. But we think that if we can just give you this pilot, you'll be able to grow and scale and figure out, chart your own course, essentially, from there."
22:05
Don Pearson: Thanks. Thanks. I wanna turn to you, 'cause David, you guys are doing a lot of innovative things with 3D view, Digital Twin, things with the technology. Can you talk a little bit about that journey, what you think about that, where you think it's going, both in terms of making products and in your products... I mean, the manufacturing of it and the product itself?
22:19
David Lam: Sure. So Vertiv. We entered the Discovery Gallery this year. Vertiv has quite a wide range of manufacturing facilities. So we perform self-delivery with Ignition in our facilities, as well as being a systems integrator and selling to our clients ourselves. So first of all, we adopted Ignition in our own facilities, 'cause we have quite a wide range of manufacturing. Everything from heavy industrial electrical manufacturing of switchgear, right down to sensitive batteries and UPSs for the mechanical side. So we first deployed that, and a big thing when it comes to trying to cascade the right message and the right solution of what we can offer as an organization for something that inherently, electricity is invisible, is quite a hard sell. And no matter how many presentations or slides that you give out, nothing is better than actually walking the talk and seeing the true simulation or a demo. So we showcased our manufacturing facility using Ignition. We used Ignition Edge in all of our facilities, and it goes up to a main Ignition head-end using Perspective.
23:36
David Lam: From there, we were able to use it as a data center demo to serve our data center segment as a main client. From there, obviously, we live in a world that's extremely digital now. A lot of this is done remotely... Meetings, video conferencing, Teams, Google Meet, is all done remotely and virtually. So some of the innovations that we started to see in the video, we are able to do augmented reality using the Apple Vision Pro. We're able to generate 3D images from CAD images that were already created, and we leverage the designs off of our 3D switchgear models, embed that into Ignition. And then apply it to an augmented reality, and it allows engineers from anywhere in the world to come and test and see the actual device through the goggles and interrogate it and see the reports live. So it demonstrates efficiency, and that innovation going forward is perfect for training and upskilling new talent that's coming into our industry. It's a great way to see things live without having to travel all over the world to do live testing in a factory.
24:52
Don Pearson: Thanks, David. So, Trevor, I'm gonna go to you 'cause I know Kevin shared some of his excitement about what you're doing and where you're going and the whole work with Fermilab, but how do you, I mean, that's a unique application. How did you go about selling the idea of Ignition or a newer technology, if you will, to address some of the challenges you had with argon, with whatever the difficulties were in getting things going?
25:16
Trevor Nichols: Yeah. Okay. Yeah, I can speak to that. So I'd say one of the keys is being objective about it. I mean, it's great to walk in and be really enthusiastic and tell them, "Oh, it's great" and everything, but if you have some data you can point to, that's better. So in our case, we kind of came up with a set of criteria that was the basis of comparison. So we looked at Ignition and we looked at a couple of Ignition's competitors and we also looked at a homegrown tool and we came up with a set of criteria. We were looking at things like, is it commercially available? What does the support look like? Is it object-oriented? Is it modular? What does the licensing look like, the cost? And so we were able to compare different platforms on this basis and then I got it all documented in an engineering report that then gets released into our engineering document repository. So that way, it makes this comparison readily available 'cause you can imagine this conversation is gonna come up over and over and over again, you know, "Why do you wanna use this new product? We've never heard of this."
26:35
Trevor Nichols: So this gives you an easy reference, something that you can go back to and easily point to that, you know, this is documented, it's been reviewed by, you know, some of our subject matter experts, stakeholders. And then I also wanted to kind of jump off of something that David said 'cause David was talking about demonstration, which that's also really important. So in my case, I built a small demo project in a simulated environment that gave us enough confidence to use it on a smaller experiment. And once it kind of proved itself on the smaller experiment, then we were able to take it to the big scale and use it on something really big and something that gets, something that the lab has a lot more publicity for. So that was sort of the progression of it.
27:28
Don Pearson: That's great, thanks, Trevor. So, Dick, I wanna move over to you with a question that relates to, I know that you mentioned when we chatted yesterday, the day before yesterday, that there's, you're at a stage of the journey, not at the level that, say, Dan is with SugarCreek in terms of the 10 years of history, but you're also using internal and external sources, so you're using integrators. You had some comments on that that I think are worth maybe sharing of how do you make decisions or how do you balance who you work with outside, who you work inside, how you build your individual team, where does that balance lie?
27:56
Dick Willis: Right. And that is a significant challenge, right, 'cause we, Ignition is the kind of toolkit where you are expected to be able to launch it in the afternoon and have something running the next day. And that's true. I mean, like I said, that faceplate that the engineer built, he built it by himself, for himself, for his own purposes, and it worked great and yielded results pretty quickly. One of our concerns, though, was the next guy, right? How is he gonna hand that off, or is it something that we could take that pattern and replicate system-wide? And there was a lot of doubt about that. We'd already, as everybody in the building knows, you inherited stuff from the previous guy and you don't know how it works, and if it breaks, you don't know who to go to, and maybe he's dead, maybe he's gone, you know, there's a lot of things that get in your way. Or you wish he was dead, one or the other.
28:43
Dick Willis: I wish he was dead. So we pretty quickly realized we had to have two things, a SCADA community that was an internal resource for us inside the buildings, and then a SCADA governance group, which was trying to say, "Have you thought about this? Here's your standard, you're not quite standard, what's your game plan to get to standard?" And that also highlighted we didn't have enough subject matter experts in the building. So we are still looking for a way to increase the strength and depth of our bench. So I'm here this week also trying to figure out who can partner with us, who can show us what good looks like, but the goal is, I'm gonna say goodbye to you in a couple years 'cause you've taught me, and now I can design and maintain on my own.
29:28
Dick Willis: That's our goal. Whether it's practical, still to be determined, but that is our goal, is to become more self-sufficient than we are right now. But it's a wicked balance. We've been doing this for a few years now, and there's still a backlog of needs that we haven't finished.
29:44
Don Pearson: Sure. Yeah. I wanna reiterate what I said at the beginning, and I'll have to have some help with being able to see, but this is your time, I wanna give folks a chance to get acquainted with you a little bit, but any questions you have, we have folks running with mics, and you raise your hand and they will see it probably before I will see it. Also try and catch people up in the top. But any questions you have, raise your hands, a mic will be there, I'm gonna ask Dan one, and then I'll shift over to somebody in the audience who wants to ask one.
30:12
Don Pearson: But before, I wanna put you on the spot. I know a few years ago, about the time you won a Firebrand, we did a more extensive case study on SugarCreek, and there were some pretty good... We had good interviews all the way from your CEO all the way down to finance people and stuff, and I think one of the things that's really important about Ignition is, how do you have the justification throughout the organization for ROI? You mentioned some numbers on OEE and OEE change, for some reason or another, those people were all ready to go on camera and say how cool Ignition was, and they all have different metrics they're looking at. So how do you work up and down the organization to get the agreement, and what metrics are you using, and how are they going?
30:48
Dan Stauft: Yeah, for us it's pretty easy, because SugarCreek, even though we're a large food manufacturer, we're owned by one guy, his name's John. I saved John a ton of money in the first two years of the project. So it was pretty easy, but when we started out, I learned quickly that... My background, in the automotive industry, everybody at all levels, from the line operators all the way up, they are drilled with continuous improvement teams, so you've got a very, very well-trained audience. At our facilities, we didn't, and we hadn't had to. It's a 59-year-old company, second generation, now run by the third, but they were running things like when they started in 1965, they didn't realize what the potential was. So what we did is, we taught them that if we did an initial measure, and we were meeting our standards, and our standards were dead wrong, and we proved that right out of the gate, because our standards were based on tribal knowledge that had been passed generation to generation to generation, not based on the capability of the machines that were on the lines.
32:08
Dan Stauft: They'd upgraded the machines, but they hadn't upgraded the standards, but they were still held to the same standards, so they built to the standards. Easy, right? So I took a line where our productivity sucked, I put Ignition on it, and now everybody could see that our productivity sucked, and they could see that it sucked in real time. I love saying that. So the next phase, and it happened very, very quickly, 'cause we said your OEE is 27%, and they said, you know, they didn't believe it. But we were based on what the capability of the machine is on that particular line. You know, it's a microwave bacon line, and the bottleneck's the microwave, and a certain number of kilowatts can only cook so many pounds of bacon. So we did the math and said, "For this SKU on that line, we should be able to produce this much," and they said, "You're lying." And that's when Craig came in. Craig came from Conagra, and Conagra's got a good automotive style of thinking. So he taught the team leaders.
33:13
Dan Stauft: He created something called the SugarCreek Performance System that dovetailed into our Ignition platform to where we showed the data, they reacted to the data, he trained the operators, and then he got a daily cadence of meetings going. As soon as you start seeing incremental growth, we went on one line, the first line we did, in two months, we went from an OEE of 28% to 78%. So in two months, with no, I mean, very little investment. And then we did it across every other line in the company. So it's really easy when you start saving that amount of money, especially when it's all coming out of one guy's pockets, what John would say is, "Well, if we can't change the culture to match a continuous improvement culture, we will change the managers and get managers in that will agree with a continuous improvement culture." So we've been so far along in this that we're doing just super oddball stuff. I've got a great group of programmers with me now, ask me, and I'll tell you all the cool stuff. We don't have time.
34:23
Don Pearson: Yeah. Well, good. Thanks. So I appreciate some of that detail. That's great. There's got to be a question out here. Who's got the microphone first? Alright. Right here. Yeah.
34:35
Audience Member 1: Yes. Hi. This question has kind of become, I guess, an annual tradition for me. But whether it's Ignition-related or digitalization, many of the presentations today and what the panelists have talked about involve a lot more connections between the plant floor and the business level. And so I always ask, you know, what kind of cybersecurity best practices are each of the panelists using? And, how do those dovetail with the connections you made?
35:03
Don Pearson: Your annual question. That's good. Appreciate that. So everybody doesn't have to answer that, Becca, if you're not dealing with that with your customers at that level. But let's get a couple of answers to that. We'll start over with you, Dick.
35:22
Dick Willis: Yeah. I don't know how detailed you want that question, but this past year, all of our sites in the North America region have gone through an OT security segregation. So we now have VLANs. We now have firewalls. We have Ignition and its related pieces in what we call the DMZ. We've gone through a thorough review. We have appliances on the network that are scanning and detecting and sniffing, notifying us when rogue devices have been added to the network. So we've gone through a lot. It's been a lot of engineering network, you know, the secret network where the guy runs his own cable. We got plenty of that and it's gone. So we think we're much more robust, but it's still a journey for us as well. Big, big, big effort.
36:03
Don Pearson: Cool. How about you, David?
36:08
David Lam: I guess we're a bit unique here 'cause serving the data centers, they tend to look after the cybersecurity themselves. So they're very selective. They deal with a lot of the Ignition partners here that are here today, Phoenix Contact, Moxa, etc. So it goes through rigorous testing by those hyperscalers directly themselves. So we're quite fortunate that we don't have to really get too much involved in the cybersecurity pieces. They kind of take on that responsibility themselves.
36:33
Don Pearson: Okay, cool. Trevor?
36:37
Trevor Nichols: So I'm gonna, you know, Dick mentioned the VLANs. That's something that we definitely put into practice. I'll say I'm a bit out of my element, so I kind of depend on our IT folks for that. But I know that we lay out a number of different networks that have different levels of accessibility. So I mean, we definitely got to keep the PLCs safe. And so that sort of, since that's what's actually running the system, and so we use Ignition for monitoring and intervention, not for active control. So you could actually turn the computer off and the PLC will keep the system running. So that's why the PLC has to be the most protected. But we do have a fairly thorough cybersecurity review where they go through things, looking at isolation. They're big fans of multi-factor authentication. And so those are some of the things that we employ in our system.
37:38
Don Pearson: Okay. Go on Dan.
37:40
Dan Stauft: You know what those guys said. Yeah, so we're micro-segmented VLANs. You know, IT takes care of the majority of our security. We're pretty secure. At our latest plant, Cisco Advanced Design Services, whoever the hell they are, they design the entire system. And it's to the point where it's really, really, you can ask Nate, it's really, really difficult to get people into our network.
38:11
Don Pearson: Cool. Alright, we got another question out here somewhere right there. Do you have a mic? Perfect.
38:17
Audience Member 2: Hi, my question's for Becca. Dealing with such a broad range of end users, have you been able to quantify any trends and improved energy usage over that kind of portfolio?
38:32
Becca Gillespie: Yeah, it's been a pretty broad range. I don't know that I can give a specific number. So we would say that the thing we look for in our screening, actually, people often ask, which industry vertical do you most look for? And we don't look for an industry vertical. We look for a human that is the right fit to be a champion, a project champion. So the way we screen it is that. And when we have success, and when we don't have success, it's usually that that person has left the company or disappeared or got pulled into a different task. And so there are cases where that has happened. And then when we do have success, it can range really broadly. So there'll be cases like the sort of one-time savings where a big, there was an over-voltage event from the utility side, and all of the machinery was at risk, and they were able to unplug it and save it. And how can you, you know, quantify that? And then there's others where we'd hope that they're gonna use it for energy efficiency.
39:40
Becca Gillespie: And as a huge energy geek, I hate this, but a lot of times I use it for preventative maintenance instead. But, you know, they quantify that in a totally different way. So they'll say, "Hey, you know, actually, I saw the amperage going up on one phase compared to the others. And it means that one of the coils is bad and my motor," etc., etc. So sometimes the savings are energy-related, sometimes they're not. And even when they're energy-related, they can come as these huge chunks of change versus, I guess, the more sort of run-of-the-mill, which is justifying an investment in a new energy efficiency piece of equipment. So like understanding how much their new line saves versus their old line, or kind of watching a degradation over time and being able to like foretell and forestall those sorts of energy efficiency degradations over time, which is the beauty of data and... Trending it. And so, yeah, I mean, but roughly, oh, yeah, we would roughly say they sort of span the whole gamut of what they work on, but they typically can save some energy as well as sort of implement some kind of other manufacturing use case that is of interest to them at that time.
40:50
Don Pearson: Thanks. Dan, you wanna say something?
40:53
Dan Stauft: Yeah, so somehow we made the cut to get included in that program.
40:57
Don Pearson: You guys are our customers, so.
41:00
Dan Stauft: Right, so our biggest plant is in Indiana, it's about 400,000 square feet. It's ammonia refrigeration, wastewater systems. I think our power bill last month was $360,000. So we are in the program, and we're just now getting around to doing the energy part of the program. We obviously didn't use the integrator, and we're using Benson's hardware for something else, but we are now monitoring all 10 switchgear at that plant. We're trending everything. We're working on an AI system to do analytics, 'cause if we can get a 5% save on a $300,000-a-month bill, that's significant. Obviously, we'd like more, but any little bit, it's definitely worth the investment.
41:47
Don Pearson: Sure, thanks. Next question, back there.
41:53
Audience Member 3: Hi, thanks for your time. It was very, very interesting to know. I had a question because over the years, we've been speaking about IT/OT integration, Unified Namespace now. I'm just curious when new plans or new capacities are being put, is there any executive-level talk among the user, talking like a unified business, which is like reimagined, and are we otherwise consistently looking at continuous improvement? Is there a new generation of plants coming up that from a concept level, a different way it's done so that we are not fixing a problem on the legacy systems? Because some of the customers we have met, we've seen over the last 15 years, they have created new legacies because they could have avoided creating the legacy, you know what I mean. So I'm just curious what happens within companies, the manufacturing companies themselves. Is there any executive-level talk around probably reimagining how to put up new plants or some conversations like a unified business, how to look at it?
43:02
Don Pearson: Anybody wanna take a shot at that as you go forward? I guess it's the greenfield world maybe of where you go with plants into the future with all that exists right now, if I understood the question correctly. You wanna say something, Dick?
43:15
Dick Willis: Sure, yeah, we did have a greenfield plant come online over the last two years, and we did try to take some of the learnings from before we did start with Ignition. We started with Kepware and it's gonna become Ignition, and we have an MES stack, and we tried to imagine it from the point of view of problem solving right off the bat. I'm not sure we were always completely successful 'cause we ran into some snags, but it's certainly the approach that we talk a lot about Digital Transformation. It's one of our key milestones for the company. We've got a lot of effort and workshops going on to say how do we make that real even in our existing facilities, nevermind the new ones that we bring online. So I think it is changing, but it's, getting it proven out has been tricky.
44:00
Don Pearson: Okay. Yeah. Okay, any last comment, David?
44:03
David Lam: I think so, certainly in our segment with data centers, everything we do is greenfield, and obviously it's speed to market and getting online as quickly as possible. So where we're seeing now is we embed, we try to embed everything. We create a design philosophy with that client, and they will roll it out pretty much to all their data centers and then data center campuses. So it's speed to market. We can do all of the commissionings. We have all the UDTs specifically designed for that client. It'll roll out with all of the switchgear, with all of the thermals, and all of the cooling, and then they can decide to come and test in person or using the latest sort of innovation that we've been doing with augmented reality. They don't even have to come.
44:50
David Lam: They can just sit. We're talking about developers and people, techies that can be anywhere in the office or in their home, working from home, and do that testing from there, and then the equipment goes straight to site and it's powered up quick, and that's one of the beauties, I guess, of Ignition is the speed to market.
45:08
Don Pearson: We got maybe time for one more question. Is there a microphone in somebody's hand that wants to ask a question out there? Over here. Go ahead.
45:20
Audience Member 4: Hi, and thank you again for all your time and your feedback. Do any of you have any thoughts on the future integration of using an AI or general artificial intelligence in the industry and where that might fit in best?
45:38
Becca Gillespie: Yeah, I mean, I guess I do. I'll just add one to that previous question as well. I think we do try to standardize the tools for small-to-medium manufacturers, which is really bizarre, but we wanna give them all of the same replicatable things but it's the way to meet in the middle between making a bespoke energy system and giving them something scalable that has that. But with respect to AI, I have a pretty short answer, I guess. It's not your first project, and that we learned the hard way. Yeah, it's not the first project. So we do find that looking at the data, sort of getting human eyes on it and starting to have them see and uncover their first findings is really important. But there's certainly a role to play in the future and I'll let you guys, I'm sure you're already using it and finding success there.
46:32
Don Pearson: Anybody else want to comment?
46:33
Dan Stauft: I think probably the, not full-blown AI, but automated anomaly detection is something that is very valuable and pretty reliable right now. Whereas AI models, garbage in, garbage out, it takes a PhD almost to define what goes into the model, what the context is, how it's formatted, what you're looking for, what are the key variables. There's a lot more than just simply saying AI, but anomaly detection definitely.
47:04
Dick Willis: Yeah. We've got a couple of things on the burner where we're trying to look, when people are putting in notes about what's going on with their machines, we're trying to look for a current spike. Like all of a sudden we're complaining about this and trying to use AI to say what's noise, what's signal, and trying to see if we can get a quicker response to a problem that's just now popping up on the shop floor. And we also have some very complicated engineering problems in terms of managing yield. And a lot of what we're tempted to do is just throw everything into the AI and see if it can predict that on Tuesday at 10 o'clock we're gonna have a yield crash. So we're trying some of those things out, but we need a much thicker SCADA layer to be able to get any kind of correlation out of that.
47:48
Becca Gillespie: I mean, I think that, well, I'll just add one more thought. Adding context to the data is so important. And so when you, obviously in my case, if we're doing pilots where there's no context, it's just three machines are being monitored within the system. But it's so difficult to add, and yet it's the only way AI can really learn is with those context layers. Otherwise it can find things that just aren't real. So it can uncover that every Tuesday your machine is breaking down. Well, you know what? The only guy that can run that machine has a doctor's appointment on Tuesday, right? Or it's the most bizarre things because you don't have all of the context in there yet. It's capable, you can get it in there. There's ways to do it, but until you have that, you can't really, you can't always learn all those things.
48:36
Don Pearson: Well, as it often happens, we overran our time, but you guys did great, okay? But we're the only people standing between this group and a little activity at headquarters that they may prefer to this panel. But can we take a minute and acknowledge all of our panelists and say thank you?
49:00
Don Pearson: Thank you.
Want to stay up-to-date with us?
Sign up for our weekly News Feed.