Speakers
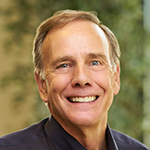
Don Pearson
Chief Strategy Officer
Inductive Automation
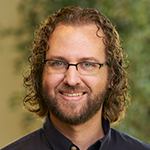
Kevin McClusky
Co-Director of Sales Engineering
inductive Automation
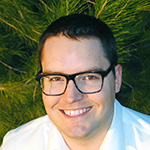
Keith Adair
MES Product Manager
Sepasoft
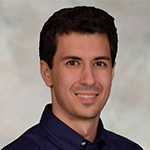
Joseph Dolivo
CTO
4IR Solutions Corp
About this Webinar
When your company’s enterprise resource planning (ERP) system communicates with your plant-floor system, it significantly improves efficiency, quality, data access, and more. For many companies, however, achieving this requires working around tough obstacles like data silos, proprietary formats, and separate domains of expertise.
With a modern software platform, connecting SCADA to ERP software such as SAP doesn’t have to be difficult. In this webinar, experts from Inductive Automation, Sepasoft, and 4IR Solutions discuss why Ignition is an effective solution for connecting operational and business systems, and how a new module makes the process smoother than ever.
Learn how to:
- Get SCADA, MES, and ERP systems working together seamlessly
- Turn data from external business systems into production data, using little or no coding
- Interface between your OS and applications without pricey middleware
- Leverage SQL databases across the enterprise
- And much more
Co-Presenting Companies
Webinar Transcript

0:00-6:18
(The presenter, Don Pearson, briefly introduces Inductive Automation and Sepasoft, and the panelists, Keith Adair, Joseph Dolivo, and Kevin McClusky.)
What SCADA and ERP Systems Do
6:19
Don: Okay, let's go ahead and get started a little bit. Just since our subject today is getting ERP and operational data to work together, let’s get started with just a quick overview of the systems on the plant floor and at the enterprise level.
6:33
Don: The main system on the plant floor is supervisory control and data acquisition, or SCADA, and that's used primarily by plant-floor operators, engineers, and technicians, and it's used for a variety of things. Controlling industrial processes, gathering and analyzing real-time data, recording historical data, keeping efficiency high, and of course downtime low.
6:55
Don: So how does it work? Well you have programmable logic controllers, PLCs, or remote terminal units, RTUs, that are communicating with machines, sensors, and end devices. And then the PLCs send the information to the SCADA software, which processes, distributes, and displays the data through HMIs, so that operators and other users can analyze the data, fix problems, and, of course, make decisions.
7:17
Don: For example, when there is a batch of product with a high number of errors, or when there's a leak in a pipeline, the SCADA system sends that information back to the central site to notify the operator. That way the operator can pause the operation to analyze the issue and take action to resolve it. That helps to keep losses of time or product to a minimum, and gets the regular operation back up and running just as soon as possible.
7:43
Don: Whereas SCADA software is for managing plant-floor processes, ERP software is for managing and automating business processes, such as your product planning, development, manufacturing, HR, financial, sales, marketing, supply chain, distribution, and more. The ERP is used to collect, store, manage, and interpret data from these business processes, and to share data across various departments.
8:12
Don: ERP software uses databases that are maintained by a database management system, or a DBMS. ERP helps to enhance efficiency and to reduce production and transaction errors.
8:25
Don: As a quick example of how ERP works, let's say your company makes dairy products. You get a lot of orders coming in from your customers such as grocery stores and restaurants. Some of the orders are for ice cream, some are for sour cream, and some are for chocolate milk, and so on.
8:41
Don: ERP takes all those orders and consolidates them and turns them into production orders for the plant floor. It checks that the operation has everything that it needs to fill those orders, such as raw materials, packaging, labels, the production machines to run it on, the personnel, the scheduling, etc. And it procures or lines up any necessary resources that may happen to be missing. It tracks the production and delivery of the orders and allows all of these different departments to work from the same data and get a view of the whole process.

Connecting SCADA with ERP
9:14
Don: If you can connect your SCADA and ERP, you can cross-reference information from the business level and from the plant floor. There are a lot of benefits that can result from that, such as making better decisions, specifically to make decisions that are informed by what is going on at other levels of the organization, preventing downtime by better understanding the causes of downtime, making your operations more efficient and transparent, complying with regulations more easily, improving quality control and quality assurance, increasing and accelerating data access. The list goes on of the benefits that come if you can get SCADA and ERP systems working together.
9:51
Don: So that serves as a little background there, but I'm going to ask our panelists just to give their perspective, and open this up a little bit, and your thoughts about the benefits of connecting SCADA and ERP, and why it's so valuable for companies today. So Keith, why don't you start first.
10:12
Keith: Sure. At Sepasoft, we've always had MES as our focus, and so I think about MES use cases like retrieving operations schedules, retrieving work orders, material data, reporting back results, and kind of having that communication back and forth with ERP. Like I said, I came up through Support and QA, and I frequently heard requests from customers about how to get our work orders from ERP, and how to get them going in Ignition, and that was always a priority for our customers.
10:45
Keith: We frequently received requests for software solutions that ease that communication, and we really see the impact and the benefit of keeping those schedules, work orders, material configuration all in sync.
10:59
Don: Thanks Keith. All right Joe, how ‘bout you? Give us your perspective on the importance or benefits of connecting SCADA with ERP.
11:05
Joseph: Yeah, absolutely. I think there's a whole set of capabilities, which Keith referred to as MES, that kind of sits between the level of SCADA and ERP. Beyond what's on the screen too, there are some other areas that a lot of value can be added to your company by having this connectivity.
11:19
Joseph: And one of those is clarifying data ownership. So you have a single source of truth for data. You have your financial data within your ERP system, you have your process and control data within your PLCs and your SCADA systems. So that avoids situations where you have duplicate sources of data which can create a lot of problems, especially for audits and for regulatory purposes.
11:39
Joseph: And again, given that ERP systems are kind of focused on being accounting-based systems, it really gives you the ability to have some financial context to your plant-floor data. So you can do things like tie dollars to downtime and scrap rates, which is a very powerful statement, so you know how much money your downtime is costing you.
11:55
Joseph: So there's a lot of value in doing it, and certainly is something that we encourage everybody to take a look at, and we hope we have some solutions to help make that easier for you.
12:03
Don: That's great Joe, thanks a lot. Kevin, your thoughts?
12:06
Kevin: Sure. So in addition to everything that Keith and Joe said, I would just add to that that there are a couple of benefits that I've seen folks have that can be pretty significant. One of them is streaming real-time data back into an ERP. So for example, inventory back-flushes can happen on a continuous regular basis. So folks who are taking a look at the ERP side of things, if they are taking a look at a production run, in addition to seeing that it's started or that it's finished, you can actually stream information back so they can see we're 23% of the way through.
12:41
Kevin: Some ERPs support that type of thing, some don't. But for the ones that do, it can provide a lot more information, a lot more real-time information, at the same time for folks who are in that position and taking a look at that.
12:55
Kevin: I'd also echo what Joe said, again, about the single source of truth, being able to pull from common inventory lists, being able to pull from common sets of nomenclature for pieces of equipment. You don't end up with five different lists of things, even site names for example, you don't end up with all these different lists if you're share information back and forth between these key critical business systems.
13:20
Don: Thanks, Kevin. I think with those comments, it's not hard to establish the importance or the value of actually connecting SCADA systems and ERP. And it isn't that ERP systems can't connect, they can be connected to the plant floor. But there are several factors that make this difficult.
13:40
Don: SCADA is part of OT, Operational Technology, and ERP is part, traditionally, of Information Technology, IT. And OT and IT are like different worlds with different languages, different data and different formats. OT data is hard to get to because it's proprietary formats, proprietary historians, as equipment can be very, very old, 40 years old, different protocols.
14:06
Don: On the other hand, IT prefers to use open standard space technologies rather than proprietary ones. And another big difference is that SCADA data is in real time, while ERP is a transaction-based system that processes data in batches. Also, ERP systems are database-oriented, while traditional SCADA systems are not. So that makes SCADA system data kind of hard to transfer and get over into the enterprise into those ERP systems.
14:36
Don: So how do you solve it? Well, you can try to manually move data across to different systems, but that's very time consuming and often requires scripting. You can try to implement solutions that integrate the two systems, but that gets very costly and could take months to finish.

Connecting Data Through the Ignition Platform
14:51
Don: The best way to accomplish this is to find a platform that works with both OT and IT, and as you might guess, I'm slightly biased here, but what I'm talking about is Ignition. Ignition was really made to facilitate the OT-IT convergence. So to tell you a little more about how that works in the context of today's topic, I want to turn it over to Kevin McClusky. So, Kevin?
15:17
Kevin: Sure, thanks Don. So if we take a look at this slide here for just a moment, I'll walk you through how we view Ignition as a platform. So Ignition sitting right there in the center, and you can think of this as a single Ignition server and Ignition gateway, or you can think of this as 20 different gateways that are all connected across multiple different plants into the Ignition platform.
15:43
Kevin: The platform enables connectivity to a lot of different things just out of the box. And if you're taking a look at that in that context, we're talking about SCADA here, and we're also talking about MES. So Ignition paired with Sepasoft's MES modules provide a full manufacturing execution system, that is what we're taking a look at in the center.
16:06
Kevin: So if we just jump through a few of these items, the touch panels, PCs, mobile devices, are front-end access, visualization screens, reports, graphics, LIMS devices, or the Lab Information Management Systems. That is device connectivity for devices that might be serial devices, or scales or measurements.
16:29
Kevin: In the bottom right, you have OPC, different data protocols allow you to communicate to a lot of different types of devices that might have OPC built in, or might be OPC DA, tunneller, historical access OPC HDA. Without getting too deep into the technical, all of those are standard industrial communications protocols, so very much on the plant side.
16:55
Kevin: Then we take a look at connectivity to databases. Ignition, one of the key platform features is very easy connectivity into any SQL type of database, any relational database. Ignition connects to PLCs very easily. We have a variety of built-in drivers that will go to PLCs. RTUs as well, as Don mentioned earlier.
17:19
Kevin: Ignition can connect out over to web services, and this has become one of the common ways to communicate out to external software systems. Right now, and traditionally, you may have thought of web services as a great way to connect to ERPs. And in the past that has been true, that that's been one of the options for connection to ERPs. But little bit of a spoiler here, you're about to hear about some other very exciting things that coming down the pipe. So I won't spend too much time on that.
17:56
Kevin: MQTT is around IIoT, so Industrial Internet of Things. It's one of those protocols, it's one of the most common and most popular Internet of Things protocols that exists today. If you're not familiar with it, it's good to get familiar. That's a topic of a completely different webinar, we've got some recordings that are back-cataloged that you can take a look at there, but we're very excited about the Industrial Internet of Things, and Ignition has connectivity built right in.
18:25
Kevin: And then other communications out to ERP systems are possible from Ignition as well. Now focusing on the communications to those ERP systems, traditionally inside Ignition it might've been a project where you'd take a week and you'd write some scripting, and you'd have someone on the ERP side set up a special interface for that communication back and forth. It might even be longer than a week, you might have to pull a specialist in.
18:53
Kevin: Here today on the phone, as they've been introduced already, we have a couple of folks who are going to be able to talk a bit more about exciting new options along those lines. So without further ado, I am going to turn this over to Keith to present on his side as well, so thank you Keith.

Introducing the Business Connector Module
19:18
Keith: Thank you so much, Kevin and Don. We're really excited to share with you the Sepasoft Business Connector Module, which we really think will make it a lot easier to connect your plant floor with your ERP system. The Business Connector Module enables seamless communication and integration between enterprise systems and Ignition-powered manufacturing floors.
19:39
Keith: In addition to allowing you to bring in ERP data to your Ignition's SCADA system, it can also tie in directly to our MES modules, our Sepasoft MES modules, which would enable you as a user to bring in schedules, work orders, material configuration data, and more from your ERP provider. It's fully integrated with the Ignition ecosystem, and it really follows the Ignition pattern of easy-to-use, affordable, standards-based, and open solutions to problems faced by industry.
20:06
Keith: And at Sepasoft, we frequently interact with customers who have need of bringing in that ERP data for Ignition, for both MES and SCADA applications. So we're often asked what is the best tool for retrieving that essential ERP data? Up to now, the answer has really been via a complex set of scripts. I've talked to actual customers who have thousand-line long scripts for making these sorts of communications happen.
20:31
Keith: That's a problem. It reduces the ability to see and understand and model the flow of business communications. So with the Business Connector Module, we've chosen to follow a key idiom laid out by the folks at Inductive Automation. Even complex processes should be easy to use. As such, we've developed our interface to be easy. We've replaced reams of script with a drag-and-drop interface for developing business logic, transforming your data from raw ERP output into your desired format, and sending and receiving data from almost any kind of business system.
21:07
Keith: I think I'm getting some feedback over from the IA side here, I apologize.
21:13
Keith: Okay, part of that is a really easy-to-use mapping tool. It makes it simple to transform data from raw business system output into the format that your operation requires, and we do so visually and intuitively, making it easier to retrace your steps and make adjustments should those be necessary. We have the aim of reducing the friction of these communications, because that friction comes with a real price in dollars and time. You shouldn't have to hire a team of engineers just to make communication simple, and you shouldn't have to rehire them all if something wasn't quite executed right the first time.
21:49
Keith: So how does this work? Well, it consists of three modules working in tandem. First is the Business Connector Module itself, that's where the business logic lives, where the sequencing engine is, and the mapping functionality. But how to actually talk to the systems? Well, we have a pair of modules there as well.
22:08
Keith: The Interface for SAP Module allows the Business Connector to talk directly to SAP systems. In addition, that module purchase includes a set of pre-configured templates for the most common several use cases with SAP. In addition, we have a Web Services Module, which allows the Business Connector to communicate with ERP systems and other business systems that use REST and SOAP APIs, so that really enables a lot of different ERP systems.
22:39
Keith: I know for a fact that Oracle and Microsoft Dynamics and many others have REST or SOAP APIs that you're able to tap into with the combination of the Web Services Module and the Business Connector Module.
22:54
Keith: We really want the Business Connector to act as a powerful tool for your global enterprise, via the Ignition gateway network, which connects your Ignition gateways that are placed around the world, you are able to distribute data retrieved from your ERP and transformed by the Business Connector to all the Ignition gateways that make up your global operation.
23:15
Keith: And if you are a user of the Sepasoft MES modules, the new MES enterprise functionality built into our OEE Downtime, Track and Trace, SPC, and Recipe modules will enable you to distribute essential MES and production data all through your global operation. This enables you to make enterprise decisions on a real-time, well-informed basis.
23:38
Keith: I'd like to turn a moment over to Joseph Dolivo from 4IR Solutions to describe a bit more of the value proposition offered by the Business Connector suite.
23:48
Joseph: Thanks Keith. So I'll kind of break this down by modules. So the Business Connector is built on standards. Dedicated middleware tools have been around for a really long time, and so developing the Business Connector, a primary goal was to not only build on best practices and open standards where appropriate, but to also take advantage of lessons learned from implementing these kind of integrations the hard way, whether that was through other middleware solutions or through programming.
24:11
Joseph: And then regarding standards, the Business Connector leverages B2MML, which if you're familiar at all with MES and ISA 95, it's an XML-based implementation of the ISA 95 object models. B2ML enables us to structure data in a form that is agnostic of any particular ERP system, whether that's SAP, Microsoft Dynamics, Oracle, or something else.
24:31
Joseph: And then in line with the Ignition platform, both licensing and support costs are far less than with other middleware solutions, often by as much as a whole order of magnitude or more. Plus the Business Connector builds on existing Ignition skillsets, which significantly reduces the learning curve and labor costs to develop and maintain a business system interface.
24:49
Joseph: And then being built as an Ignition module enables really deep integration into the Ignition ecosystem. The Business Connector takes advantage of this and leverages familiar concepts like drag and drop, tag binding, and Ignition's scripting engine rather than trying to reinvent the wheel.
25:03
Joseph: By itself, the Business Connector is already a powerful tool for exchanging data between Ignition and various business systems, but it becomes even more valuable when it's coupled with other components of the MES suite from Sepasoft. As Keith mentioned previously, the Business Connector can automatically create MES objects like production schedules and materials, which can synchronize bidirectionally across an enterprise as part of the MES Enterprise 2.0 platform with almost no work from the user.
25:28
Joseph: Regarding the interface for SAP, minimal configuration is one of the goals. Outside of user account setup, no configuration is required on the SAP side for the null SAP installations. And even for SAP systems that have been customized, the time and effort to get set up is significantly reduced versus installing and having to maintain another middleware product.
25:48
Joseph: The module will be undergoing certification by SAP's integration and certification center, which involves rigorous testing to ensure that the module is reliable and can scale up as connectivity requirements change and grow in the future.
26:01
Joseph: And finally, we're bundling the module with a number of built-in templates that you can use outright or customize for your particular SAP landscape. And these templates provide for common data flow scenarios, and when combined with the MES object synchronization that's handled automatically by the MES Enterprise 2.0 platform, you can easily replace over 1,000 lines of code with an interface tool that is visual, that's intuitive, and still flexible to work with.
26:24
Joseph: I'll pass it back over to Keith to show you the modules.

Business Connector Module Demo
26:28
Keith: All right, thanks, Joe. Now we're on to the live demo part of our presentation here, and let me toggle over to my Ignition designer.
26:37
Keith: So here we are in the Ignition Designer looking at the Business Connector. And I hope you get a sense of what we're looking at here. This is what we call a Business Connector chart. You can see that it involves several steps. Let's start with the very simple one here, this one's called output materials, and it involves a start step, a step where I'm communicating with an SAP BAPI and an end step.
27:01
Keith: Let's follow these a bit more closely. In this start block, I'm able to configure chart parameters that allow me to keep track of data that I find and recover and receive along the way. It also allows me to set values ahead of time when I call this chart. Then that's followed by the SAP BAPI block. The SAP functionality here enables you to really navigate hierarchically or alphabetically through the various BAPIs or Business APIs that SAP provides for us, from attendance to equipment to functional locations.
27:41
Keith: In this particular chart, I'm looking at the BAPI called Material Get List, and what I'm trying to do is retrieve a list of materials that I can then throw up on a screen on the Ignition side. So I'm able to communicate via sequential RFCs, transactional ones, queue-based. We support all of these sorts of idioms that SAP specifies.
28:08
Keith: Now I want to walk you through this particular block here. As you can see, there's an input tab and an output tab down here. On the input tab, the Get Materials endpoint here requires some endpoint from me as the user. In this case, it wants from me my maximum number of rows. And so as you can see, I have mapped in a max rows value, so when I call this chart I can say, "Give me 20 materials."
28:37
Keith: And let's show you how that looks over in Ignition. On the other side, we get an output table called Material Number List. And this is kind of in this raw SAP output material description, and we're going to transform that again into this nice format that I've pre-configured with just name and description. And then that comes out of this chart for use in an Ignition screen.
29:03
Keith: So I head down to my screen here, I'm able to call this chart and fetch all those materials from SAP. I'm able to scroll through and see all of those material names, which are these great leading zero material names, and these descriptions. And then I'm able to select these in turn, and it will go query SAP again for more data about these.
29:32
Keith: How does that work? Well if I head back up to my charts, there's another one called Get Details. And that takes in a material name and gets more detail about it. So if I look at this here, you see how I'm able to map in all of that data from, again, that raw ERP output into this format that I want. I'm able to exclude the things I don't want. I'm not interested in the container, the storage conditions, the temperature conditions. I just want my name, description type, division, and group.
30:06
Keith: So I map those in in a very drag and drop functionality, and that powers this screen. I'm able to quickly get a list of data and hop between them and understand really what I have over on the SAP side. So I know that my Ignition installation, my SCADA system, and my ERP system are all in sync.
30:30
Keith: I'd like to show you a more involved use case. Like I said before, at Sepasoft we make the MES modules as well. And so a common use case is wanting to retrieve materials, operations, schedules, work orders from your ERP system. So I have a pair of charts that retrieves materials and save them into what are called MES objects.
30:54
Keith: The first one is called Get MES Materials, and it looks not dissimilar from that first chart in that it has a start block, an end block, and a Get Materials step. But you see we have a new block called saved MES Objects. So let's walk through these here.
31:11
Keith: Again, we start with the start block with a max rows parameter, and in this Get Materials block, again I am just retrieving that material number list table, and I am mapping that over into what's called B2MML. That's the format that Joe described a moment ago. And I am getting a material ID, a description, and the material class. And as you can see, I'm not actually getting a class from SAP, so I'm actually providing one myself.
31:49
Keith: We have this nifty way to modify and create functions. In this case, I'm simply setting that class to be materials. In addition ... I'm sorry, there's one more step here. So now that I have mapped this data, I can go on to this save step, where I save the output from the previous step. So what does this give me? Well, it enables me to save my MES materials.
32:15
Keith: So let's go down to a screen where I can show this in action. If I had what's called my MES Object Editor, you can see that I currently have no materials. If I click my Get Materials button, it will call that chart and retrieve those materials. And I provide a row count of 20, and so I only retrieve 20 of those materials, and they're all sorted into that materials class. And if I look at the settings, you can see I got the name and I got the description.
32:44
Keith: Now, I have one that says Get Classes. So if I hit that, I'm also going to retrieve the SAP group name. So you can see how not only do I have the materials, but I also have the classes. So if SAP gave me an SAP group for that material, I'm able to sort the materials into those classes.
33:05
Keith: How does that work? If I head back up to my chart, this one’s called Get Materials From Class. And in this chart, I'm again getting that list of materials, but instead of just simply mapping out and saving right away, I am iterating over those materials one by one. I'm iterating over that material number list, and I'm going into this Get Details step where I am retrieving the group name.
33:33
Keith: So if I expand these both out, you can see how I'm mapping into the material class, as well as to the material definition. And if I make this full screen here, to make it a bit more apparent, you can see how I've mapped again from that raw ERP output, including that material group name, over into my desired material format. And if I hop between these, you can see how it highlights for me very nicely which connection I'm working with.
34:05
Keith: We're really trying to make this easy to use, so you don't have to require sophisticated skilled code writing engineer to do this. You can have someone who understands these things conceptually. So in this case, I am retrieving my materials and classes, and I'm able to of course go into a decision block. And this decision block allows me to specify a class name and say I really only want materials that are in this class. And then I get, of course, if it fits that class, I save the MES object, and then I go on to the next material.
34:40
Keith: And I loop over this over and over again until I run out of materials and I am done, and I progress to my end block.
34:47
Keith: So let's see that in action here on this screen. Here's my object editor, and again, if I clear these out, I get my materials, retrieve them all, and then I can call again that chart, loop over all of those, and get those classes. So you can see how really quickly, in just a few minutes, including with me talking over it, I'm able to really retrieve that data and use it in either an Ignition context, on a screen, on a table, maybe put it into a database table, or I'm able to retrieve them for use in my Sepasoft MES solution.
35:22
Keith: We really hope we're showing here that we're enabling more users to get into understand those ERP to SCADA and MES communications, really democratizing that flow of data, not requiring so much expertise to make this possible.
35:42
Keith: And with the demo concluded, I'd like to pass this back over to Don to continue the presentation.

Closing Discussion: “It’s A Game-Changer”
35:49
Don: Thank you very much, I appreciate that, Keith. And as we are looking at going into Q&A session, I just want to say from a closing discussion standpoint, that, Keith, are there any comments you want to make? I know, very good job on the demo, very interesting. Wrap it up with any thought on how you think that this Business Connector Module with Ignition is going to help industrial organizations. I want to give you a chance to comment, and then our other panelists.
36:17
Keith: We really think it's a game-changer. Thank you Don, we really think it makes more folks able to see into this interaction, to participate in this communication of data. We think it allows folks to be more successful, to have more visibility, to make these communications more stable, more understandable, more secure standards-based SAP-certified. We think that's a unique offering.
36:43
Keith: We're always having folks tell us, "Well, my scripts to retrieve my schedules isn't working. Please help me debug this," and we're having to read into what other engineers have left behind, and it's frequently been a pain point. We're trying to relieve that pain point, help our users be successful, and get them on the way to implementing this data, using it in both SCADA and MES contexts.
37:06
Don: Thanks Keith. And Kevin from your viewpoint as a sales engineer, you're working with customers all the time and building out their architectures, trying to get access to data, doing the things that this Connector helps do. Your thoughts on it?
37:17
Kevin: A high percentage of our customers are already connecting up to SAP and other ERP systems. I think that the high value for those customers is that this makes it so much easier. You can take a look, and as you saw there, there's about 100 properties in SAP for any given endpoint that you have going back and forth that are optional. Let's say you have the four points that you're syncing over to Ignition, and you want to make accessible. And then you later want to come in and add another one. You don't have to go back and reprogram the interface and change things, you drag another line from the left to the right to connect those through, and then you throw that into a database and you're good to go.
38:01
Kevin: So I think it really opens up a lot of flexibility and a lot of ease of being able to simply play with the idea of pulling in different information, sending other information back without a significant investment in engineering resources and time to make those things happen. So I think it really facilitates that communication a lot easier than it has been in the past.
38:26
Don: That's great Kevin, thanks. Hey Joe, your thoughts?
38:29
Joseph: Yeah, I think Keith really nailed it when he described it as a game-changer. I mean again, we've been doing this for a very long, and for SAP as an example, we've been using SAP MII, we've been using SAP PI, we've been using IBM WebSphere. There's a whole bunch of other middleware tools that really have their own set of skills you have to learn to be able to manage those. A lot of time it's something that maybe an IT group or an SAP basis group is going to restrict access to.
38:53
Joseph: We're really democratizing that and making it available to you, who are users of Ignition, or hopefully soon users of Ignition. It really lowers the required skillset to be able to do a lot of this. It takes a lot of scripting out of being a core requirement. It is still there from a flexibility standpoint if there's things you want to do, but most of the things you're doing you're kind of building and constructing and modifying these flowcharts. And so it becomes very accessible to modify these in a visual way to become very intuitive.
39:19
Joseph: And the biggest gain, especially for working with SAP for example, is a lot of times even if you're using another middleware tool, you're starting from scratch. You're basically having to build out all of your data flows, understand what BAPIs or what IDOCs or what have you do I have to subscribe to an SAP. Now we're distributing this with built-in templates that are going to take care of probably 80% to 90% of your typical use cases.
39:41
Joseph: So we're going to have templates for downloading materials. We're going to have templates for downloading production schedules. We're uploading your production confirmations for doing goods movement. The templates are going to be coming with the product, and so you're going to have to maybe use those outright or tweak those, but it really, really lowers the barrier to entry and the amount of engineering time to get a working system in place. So we're very, very excited about it. It really is a game-changer.
40:01-55:29
(The speakers answer audience questions for the remainder of the webinar; please go to the webinar recording to hear the Q&A.)
Want to stay up-to-date with us?
Sign up for our weekly News Feed.