Unlocking Greater Efficiency: The Why and How of OEE Implementation
57 min video / 46 minute read Download PDF
Speakers
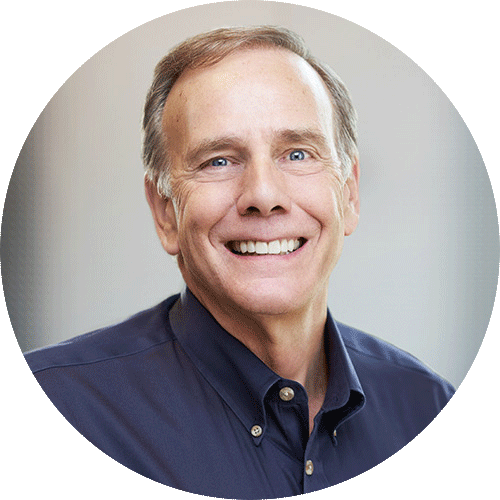
Don Pearson
Chief Strategy Officer
Inductive Automation
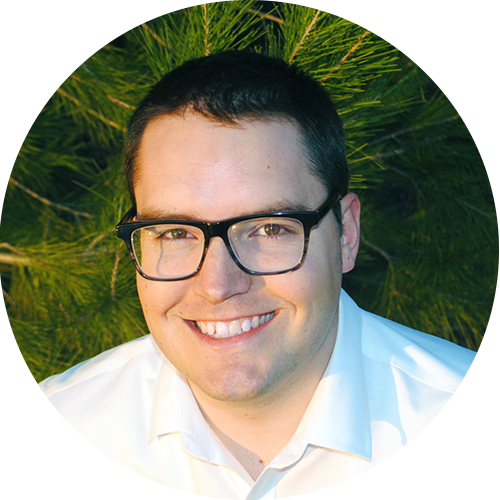
Keith Adair
MES Product Manager
Sepasoft
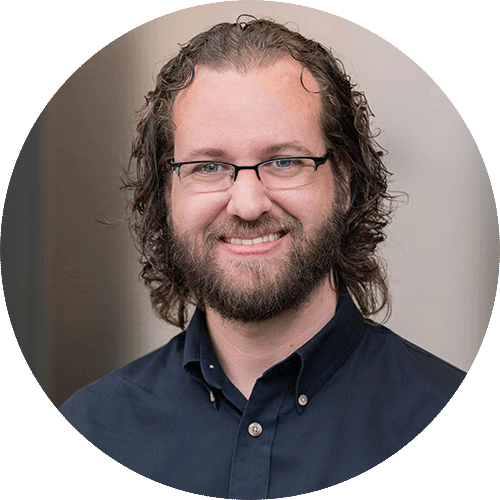
Kevin McClusky
Co-Director of Sales Engineering
Inductive Automation
Overall Equipment Effectiveness (OEE) is a metric that has helped many industrial organizations achieve real manufacturing gains and significantly increase profits. OEE has been proven to work but that doesn’t mean that simply calculating your organization’s OEE number or installing OEE software will cause the results you want to materialize. Ultimately it’s not just OEE data that makes a difference — it’s what you do with it.
In this webinar, experts from Inductive Automation and Sepasoft will share compelling insights about why OEE is so valuable and what it takes to implement OEE successfully. No matter which industry your organization is in, this informative presentation can help you get this year off to a more efficient start.
- Learn why you should consider using OEE
- See how OEE can help reduce downtime
- Get guidelines for implementing OEE effectively
- Discover real OEE success stories
Co-presented by:
Webinar Transcript
00:00
Don Pearson: Welcome to our webinar today, Unlocking Greater Efficiency: The Why & How of OEE Implementation. My name is Don Pearson, I will serve as the moderator for today's webinar. Just a quick look at our agenda today before we get into it. I will introduce Ignition and Sepasoft, and then I'll introduce today's speakers. We'll discuss why your organization should look at implementation of OEE, how to see the big picture of plant performance, and how to identify constraints in your process. We'll present a demo, we'll talk about how to take action, then we'll have a discussion to wrap things up. Those of you new to Ignition, just a bit of information on Ignition by Inductive Automation. It's a universal industrial application platform for HMI, SCADA, MES and IoT. It turned 10 years old last year and it's used by 54% of Fortune 100 companies for implementation as well as, I think, 30-32% of Fortune 500.
01:06
DP: It's got an unlimited licensing model, cross platform compatibility, IT standard technologies, scalable server-client architecture, it's web-based, web-managed, web-deployed designer and clients, modular configurability, which of course gives you the opportunity to just buy what you need and grow and scale as you need to, and of course, rapid development and deployment tools. This sort of modular nature of Ignition that I mentioned, and it really allows you to build the exact type of system that you need. There's a full suite of powerful Ignition core modules and third-party modules available for Ignition. If you look at our software stack here, it really allows you to easily develop customized industrial applications that fit your unique processes instead of the other way around. And as you can see here, Sepasoft is a strategic partner of Inductive Automation. Just a quick slide on Sepasoft. It was incorporated in 2003.
02:06
DP: They developed and provided support for a suite of MES modules for Ignition, as well as modules for ERP connectivity. Hundreds of companies in many industries rely on Sepasoft's MES software every day, worldwide. They have more than 600 MES implementations and more than 50 MES certified system integrators. And Sepasoft is certainly the best authority to speak about today's topic, which is OEE. So, we have a pretty good guest presenter today, Keith Adair. He's the MES Product Manager at Sepasoft. And we'll also have Kevin McClusky joining us as a panelist. Kevin is our Co-Director of Sales Engineering here at Inductive. So, rather than me doing introductions, I think I'd like each of you to take a moment to tell a bit about your background and your roles in your organization. So Keith, how about you first?
02:58
Keith Adair: Thanks so much, Don. My name is Keith Adair. As you can see here, I am the MES Product Manager for Sepasoft. I've been with Sepasoft now for five years. I began in Support and worked with folks who were going through troubleshooting problems and going through continuous improvement. I spent some time in QA and led our QA efforts for a time, and then recently, I've been the MES Product Manager where I work carefully with our internal team, especially our development folks, to work on new products and perform improvements on existing products and really try to deliver the best software we can to help folks throughout their process of improving their efficiency and their performance. So thanks, Don.
03:45
DP: Thank you, Keith. Alright, Kevin, introduce yourself.
03:48
Kevin McClusky: Sure. My name's Kevin McClusky. As Don said, I'm Co-Director of Sales Engineering, and as you can read on the slide that's right there. Chances are, if you've been part of one of these webinars in the past or several of them or the other ones, you've probably heard my voice or seen my name around. I've been with the company, Inductive Automation, for about 10 years, actually a little over 11 years at this point, and it's been quite a journey becoming one of the major players inside the market like we are now, starting from a much smaller company when I was part of it. That was still multi-country and we still had a significant presence but nothing like it is today. So, it's been a fun ride getting here. I'm on the technical side with Inductive Automation. So in sales engineering, my division does a lot of architecture recalls, a lot of working with specific customers who are doing OEE implementations and other project implementations as well. I've personally been involved with talking to and providing guidance for hundreds of companies, a good number of them doing some sort of OEE and MES capabilities through Ignition. So it'll be good. Answering questions here, Keith's really the star of the show. Keith has fantastic experience along these lines but I should be able to add a few things here and there from the Inductive Automation standpoint and possibly answer a few questions along the way.
05:23
DP: Thanks a lot. Totally appreciate you being here today, Kevin. Today, we're gonna be talking about OEE, as I mentioned at the outset, Overall Equipment Effectiveness, and we found, actually, that a lot of people in the industrial space have heard of OEE and are interested in it. We also found that there are some misunderstandings of OEE and a lot of questions about what's the best way to implement it, if you decide you do wanna implement. So we'd like to tell you about what OEE really means, and really why it's something you should consider implementing and how to go about it. So, as Kevin mentioned, Keith is the star of the show. So with that, Keith, we are turning it over to you.
06:07
KA: Okay, thank you so much, Don, for the wonderful introduction. And I'm excited to be able to share with you folks a little bit today. For this webinar, we're really trying to avoid this being sort of a sales pitch. I'll share a little bit about our tools for identifying ways to improve equipment availability and performance, but I'd really like to communicate what I've learned and what we at Sepasoft have learned from working with people who are all along the spectrum of digital transformation, what enabled not just successful automation and Ignition projects, but real improvements on the plant floor. And I thought it only fitting to start with a definition of what OEE actually is.
06:53
KA: It consists of what are generally called the Three Factors of OEE which are as follows. Availability is, roughly speaking, the amount of time your line or machine or area or site, etcetera, spends in a running state compared to total time spent in production. It's expressed as a percentage as are all of these in fact. So, if in a five-hour production run, your line spends a half hour in an unplanned downtime state, your availability score will be something like 90%. Performance on the other hand is parts started divided by ideal parts started over a period of time. So, if over the course of an hour you start 85 parts when you hoped to have started 100, your performance is 85%. Finally, quality is good parts divided by total parts started. So, if over the course of an hour, you reject 4 out of 100 pieces started and produce 96, your score is 96%. And after all of that, you multiply those three percentages together to get your OEE score.
08:06
KA: So if your availability is 90%, your performance is 85%, and your quality is 96%, as in our simple examples here, your OEE would calculate out to 73.4%. Now, that value, that 73.4%, is an all-encompassing value that represents a real view of how well your equipment or line or whatever are performing. And what's great about that value is that as you make any improvements in your plant, reduce the occurrence of machine faults, minimize rejects, accelerate production, your OEE climbs in turn. And so, it becomes a measuring stick for almost anything you do in your plant to increase performance. So, the first question I'd like to ask is, "Will you benefit from OEE?" So, at Sepasoft, I have the pleasure of working with a ton of folks who are considering ways to help their machine, line, plant, enterprise accelerate to the next level. Now, we make software aimed at helping folks take those next steps. When I speak with people at all levels of those organizations, I've asked them questions that are really trying to understand why they've reached out to Inductive Automation or to Sepasoft regarding downtime analysis or KPIs or what have you.
09:30
DP: And when I say, "Will you benefit from OEE?" I don't mean necessarily from our software in particular but will you benefit from doing the leg work required to calculate your OEE score? From those experiences, I've pulled out these questions that seem to be a common through point. So number one, do you sell everything you produce or is your line producing goods that are ending up in your warehouse? Are you producing for sale or are you producing for inventory? Are orders always filled on time without fail? Do you know your top reasons for machine and line downtime or are you kind of winging that? Is overtime required frequently to meet your commitments? Do you need to increase your profit and your profitability in revenue? Do you need to improve your capacity? Are you sitting on a lot of unused inventory? It should be pretty clear, but if you answered no for any of one through three or yes for any of four through seven, you might really benefit from determining your OEE score and understanding your line availability, your performance, your part quality.
10:46
KA: These questions are the ones that are gonna guide you towards implementing OEE and trying to get a sense of what's happening there. So to add a little more fuel to the fire, I wanted to share a sense of what others have been able to achieve by implementing the OEE at their plants and in their enterprise. These are pulled from a few case studies on our site or maybe they're on Inductive site, they're in some webinars, and they're also in articles in Control Engineering and Automation World. So these are publicly available information, most of these are. The first one, a major chemical manufacturer, was notably able to reduce its work week from seven days to five. Now, how were they able to do that? Well, they used the OEE tools and the knowledge and the insight gathered from OEE to increase their efficiency such that they were doing in four or five days what they previously took all week to achieve. And so, instead of running for seven days at a higher efficiency, they chose to run for five days so they could give their employees a weekend, increase employee morale, all those good things that come from having a weekend, we love our weekends.
12:03
KA: Swedish Match Tobacco, they described that they were able to get real time information and visibility, that the solution and the process of gathering their OEE score exceeded their expectations. They were able to increase their schedule rate by 12.5%. Now, what that means is that a production order or a schedule that would have taken them an hour now happens 12.5% faster. They were able to reliably and continuously produce goods more rapidly and more accurately such that they were able to increase that by 12.5%. Pretty cool. Hunter Industries, they make at least my sprinkler automation system at my house, they saw $300,000 in savings in 2019 alone, and they described that they saw an 8% increase in OEE across all their buildings. Now, you can see here how Hunter is using OEE as that metric, just like we described. So they were able to see that huge improvement, 8% increase in OEE. That's a big deal.
13:14
KA: A very recent webinar we were able to perform in tandem with Chris McLaughlin over at Vertech was for AriZona Beverages. And AriZona described that they were empowered to keep their 23-ounce can product at a 99% price point. That was their goal that they put in place in order to evaluate whether their OEE project was successful. "Are we going to be able to keep our famous 23-ounce bullet can of tea or juice at that really affordable price point?" And they felt they were able to at the end of that process, that article is in Control Engineering. You should look that one up, it's a good one. Daimler Trucks, they felt that they were empowered to optimize their operations and to benchmark and compare production volumes in real time, so they were given that real time visibility. And then Samtec, we have a case study with them, they used the OEE module to monitor their rate of gold consumption on a daily basis, line by line, operator by operator, part number by part number, and they saw massive reduction in their gold usage.
14:24
KA: So they make connectors for computer parts and those heavily use gold for its various qualities, and they were able to very much reduce their waste and their usage by implementing OEE and our OEE module. Now, this is what people have actually been able to achieve by understanding the things that OEE can teach us. OEE helps us understand what equipment is failing, why it's failing, sources of waste, which lines are hitting their ideal rates and which are not and much more. These particular folks, they did use our OEE module but we've only picked these due to our... I've picked these due to my personal familiarity with these companies and their results. I'm confident that a well-organized effort to implement OEE with any of a variety of tools will enable similar results, but we're obviously proud of the tools that we've built for this purpose. So how do you begin on the path towards collecting your OEE score and making those improvements?
15:32
KA: Well, in talking with the folks at those organizations and others, plant managers and operators often explain that they get bogged down in the nitty-gritty of running a plant, running from crisis to crisis. "Why is this work order late? Why is this machine down? How long will this inspection take?" Etcetera, etcetera. So I have kind of a cheeky metaphor here, this lovely mural of the late great Leonard Cohen can be found in his hometown of Montreal, Quebec. This particular view of this mural can be found a few blocks to the west of this particular building from an elevated vantage point on top of another building in Montreal. However, from street level, here is what you might see. Now, same building, same mural but now old Leonard, you can't really get a good look at him, you're not sure what's really happening on that side of the building. Similarly, in your plants you might find it difficult to get the big picture when you're right in the mix of things, always watching for the squeaky wheel.
16:38
KA: Just as with this mural of old Leonard, you might need to take a few steps back to see the big picture. To start getting a sense of that bigger picture, a good place to start is by listing out the possible sources of inefficiency at all manufacturing plants and at your manufacturing plants. So one, machine centers are frequently blocked by downstream problems or starved waiting for raw materials. Is your flow of material down the line frequently stopped and started because equipment is going up or down? Are you having unexpected shutdowns for inspections or safety reasons? Are things occurring that require stoppages for inspection at times you don't expect? Are there injuries on your line? That's obviously a source of inefficiency as well as a safety risk. Are there frequent machine faults? Potentially, overcomplicated procedures can be a source of inefficiency.
17:40
KA: Can you make a part twice instead of three times? Can you use a different painting process or what have you? Can you simplify your procedures? Another possible source of inefficiency is whether material flow is intermittent or otherwise not ideal. Are you seeing big waves of parts and then they slow down? Do machines not work at continuous rates? If machines work at varied rates, are they limited by the efficiency of the slowest cell? It almost helps to think of your plant as a one-lane road or a two-lane road and you're limited by that slowest car that's causing traffic to back up for miles. Another possible metaphor here is a set of hikers, and they're all progressing together towards a destination. Such a group is often constrained by their slowest member. If you don't want to arrive without the guy in the back there, you have to walk at his pace and that's very similar to our production plants. Do you have too many rework cycles? Are you having to rework and redo and redo parts before they can come out and be ready to go? That's obviously a source of inefficiency.
18:53
KA: Is your rate of rejects too high? Maybe a bigger picture, are your goals unclear? Remember AriZona's goal was to keep their 23-ounce can at that 99 cent price point, that's a very clear goal. If you don't know what your goals are, you'll never hit them. An unset goal is never achieved, so you have to set clear goals in production requirements. Are your operators perhaps undertrained? When a crisis occurs or an equipment downtime that happens, are they equipped to handle it? So these are possible sources of inefficiencies that we've seen in working with customers. Yours might be different. Make a list, list down what things slow your plant down. And that's a really, really good place to start. It will help you to get a place to jump off and make improvements, and you should do that. However, one of the things that I've picked up is that it might help to look at your plant in terms of its constraints.
19:55
KA: Now, Eliyahu M Goldratt wrote a really good book called The Goal which is intended as a guidebook for improving the efficiency of any business but it is written in the form of a novel, oddly enough, about a plant manager who is attempting to improve a plant performance. Sounds similar to our situation or your situation. And the main point of that book is something called The Theory of Constraints. So, what is a constraint? And what is the Theory of Constraints? Well, Eliyahu says, sorry for getting familiar with the first name there, "A constraint is anything that prevents the system from achieving its goal." In manufacturing, we might define a constraint as anything that slows the rate at which an enterprise or a line or a plant or what have you produces saleable goods. What's slowing you down from making products you can sell? Some folks in plants call constraints bottlenecks, and you likely know what your bottlenecks are. The Theory of Constraints is focusing on improving the constraints, relieving the pressure at the bottleneck.
21:06
KA: That's the claim, is that that's the best way to get your business to be more profitable. So imagine your bottleneck, randomly, is your palletizer. Can you augment your palletizer with another one in parallel? Can you run the palletizer operator crew in shifts ensuring that the machine never stops running? Can you improve flow into or out of that palletizer such that it can always process it's load more efficiently? The Theory of Constraints asks us to think this way about your plants, every process has constraints. The Goal and The Theory of Constraints claims that focusing improvement efforts on those constraints is the fastest and most efficient, effective path to higher profitability. So how do we identify our constraints? How do we know what those constraints are? When folks reach out to us to explore implementing OEE, I make a point of asking what tools they're using to collect data to feed their current KPIs. Frequently, it's something on this list: Manual data entry on paper or in spreadsheets or on chalkboards, they're writing things down, they're maintaining spreadsheets, they're passing things around.
22:26
KA: That's in fact the original MES, Multiple Excel Spreadsheets. Maybe they're winging it, they're using their gut to make choices. Perhaps even they're making, heaven forbid, self-interested decisions, they're marking a machine fault as a clean-in-place or something to that effect. When you have manual data entry and paper records and the ability to do as you will, you can really run into problems. The problems with these are numerous, they rely on human accuracy and honesty, they're often hard to keep up with, and there will always be discrepancies from reality with manually maintained data. So, how do we get around these problems? To avoid the negative outcomes with manual maintenance of data, it's usually a good idea to automate as much of the collection of data as possible. That's not to say that if you are unable to automate data from one machine, you should abandon the effort and stop there. Most of the time, OEE projects end up being a hybrid of automatic and manual data collection to some extent or another.
23:36
KA: In any case, the data points you need to power OEE calculations and thereby identify constraints are largely as follows. Machine count data. How much product is coming in or out of a particular machine? Where are rejects coming from? That's a key data point. How many pieces are you starting and finishing? Equipment state data. Frequently, on pieces of equipment you have a PLC value that represents the equipment state or the downtime code. So one might be running, four might be stopped, five might be a jam of some kind. Equipment state data. Other contextual data. What material are you producing? What work order are you producing against? And much of this data, we feel, can be collected automatically from your PLCs or your other industrial equipment.
24:33
KA: We think that using automation to collect this data and quickly calculate your OEE is by far the best and most accurate way to calibrate and measure improvement efforts. If you use automation as a tool to identify these constraints, you can have accurate recording of downtime to the second. You know when you're down, when you're back up, 'cause your PLC tells you and tells you what time. You can identify downtime causes automatically. You're not guessing, you're not writing them down based on what you're seeing, the equipment tells you why it's down where possible. You're empowered to make improvement decisions based on automatically recorded facts rather than judgment calls. You're minimizing the time that you're requiring your operators to spend managing paper and you're maximizing their time running the equipment, maximizing efficiency that way.
25:28
KA: You're frequently able to reduce the amount of rework because your operators are focused on what's happening in front of them. And finally, you're able to track production against scheduled targets in real time. "How close are we on this work order?" Well, we know 'cause we know how many counts we've produced, and we know how many good parts are on this work order so we can see how close we are to completion. Now, obviously we believe that the best tool for automating this collection and the subsequent OEE calculation is Sepasoft's, our own OEE downtime module with incoming equipment data being provided by Inductive Automation's Ignition platform. If you'll indulge me, I'd love to take a moment and share a little bit about what our tool looks like. Now, I'm showing you here our newest improved components that are taking place in the new or the new-ish, it's been new since last year, Perspective Visualization tool from Inductive Automation.
26:28
KA: Now, Perspective lets you use the fully fledged automation tools you know in Ignition right in a web browser or an iPad, and here we're using them in an MES context. So I'm able to quickly drag and array components on screen to empower my operator to see right from their iPad or from a web browser or from the new workstation thick client how well their line is producing. What's my OEE? What are my top downtime reasons? Just from this dashboard that I was able to rapidly create an array on screen, I can see my in-feed count, I can see my out-feed count, rejects, what product load I'm producing, I can start and stop production runs, I can see downtime occurrences and I can override downtime reasons from one reason to another, I can even add notes and annotate why my equipment was down and revert back to the original reason.
27:26
KA: I have lots of power to have real time understanding of why my equipment is down, add context, override reasons, split reasons, these things can now all be done in a really nice visual way in these Perspective-enabled web or mobile clients. Here's my top downtime reasons and here's my OEE in-feed, out-feed, reject count. So, the idea here is you're able to see all this stuff in real time right where you need it, not necessarily back in a terminal, back in the back office but right on the plant floor or on an overhead display. So here it is running on an iPad. So, I can hold this in my hand, tap through my reasons, start and stop production runs, it's all available right where you need it. Also new for this year, we have the ability to install software directly onto Edge devices like this Opto 22 groov EPIC and have those OEE counts run in real time right on the edge of the network using Ignition's Edge product. And here is a tool for producing an analysis data set. So here, I've chosen, from among our many data points that the OEE module provides, I've chosen my line downtime reason and my line state duration.
28:45
KA: Why was I down and for how long was I down? I can filter down to a particular line or area or equipment and then I can group by my line downtime reason, and I can also order by my line state duration. And when I run this report, I'm empowered to see my OEE... Sorry, my top downtime reasons, and that report can be turned into a widget on our screen or put on a dashboard or what have you. So, that's our OEE module and that's how it looks these days. It runs right on your mobile devices, right on a web browser or wherever you want it to run, and that's empowered by that Ignition Perspective component. And we're really proud of our OEE and downtime module. We sincerely think it's the best way to simplify the automation of both the collection of state, count and other data, as well as the generation of your OEE score and other KPIs in real time, and we sincerely believe that installing Sepasoft OEE will bring visibility to your constraints.
29:55
KA: You'll be able to tell what your top downtime reasons are, where your lines are producing waste, what percentage of work orders are completed on time, which operators oversee the most effective shifts and more. But that's a lot of the value in our solution, it's shining a light on what's happening, it's letting you know where you're having problems. But our software, as much as we're proud of it, cannot change your workflow. We can't fix a chronic machine fault or train your operators or reduce rework and waste. That's what you folks have to do as empowered by the knowledge coming out of our software. And so, what I'd like to transition into here now is how do we take action? How do we take the input from these tools and use it to feed our efforts to improve our plant? And so, the first step in our book is to get the right team together.
30:49
KA: Now, at Sepasoft, whenever someone purchases our software, especially a first-time customer, we have what's called a Quick Start Program where someone in our design consultation department gets in touch with that new client to ensure that each project gets off on the right foot. When we have our first call, much of our time is spent asking you folks about the team of people involved in the project. Who is the project's IT contract? Who is in charge of quality? Who is the project sponsor for the customer? The reason why we make a special point of doing this is because, through hard-earned experience, we've learned that OEE and other MES projects only really work when you get everyone involved in a room, or at least a Zoom. We've occasionally taken calls from folks on both sides of the IT OT divide who are considering OEE software for reasons that might be at odds. We've spoken to folks at a plant who are trying to prove corporate wrong about their efficiency or what have you, or folks at corporate who are trying to push down a corporate standard.
32:00
KA: And those things aren't bad, necessarily, but they're not gonna bring the team together to work together towards those improvements. In your plant or your enterprise, I know there's a team of the right folks. It might be people from operations or maintenance, or management, or quality, or IT, or others. These are just people we thought about off the top of our heads but it could be other folks. You may not need some of the folks in our list, you might need more folks but the point is, you get everyone together across that IT OT divide, across these teams and you get them in the room together to talk about how to make improvements. That's the point of what I'm trying to share here. And once you've gathered that team together, there is a process that Eliyahu M Goldratt lays out in The Goal that successful teams should repeat and something like this... I'm paraphrasing here but that team should meet regularly, get together weekly, monthly, whatever works, some cadence and analyze data to identify and emphasize constraints.
33:12
KA: Elevate the constraint. So, if your data coming out of the OEE Module or your other tools or what have you told you your palletizer is the problem, or that this operator is the problem, or this section or this process is the problem, identify anything that impedes smooth material flow throughout your plant. Identify those things and those are probably your constraints. Find room to make quick improvements based on those constraints, pick the low-hanging fruit and then carefully implement larger changes and measure results as you progress. So, let's say you do say that your palletizing area is your bottleneck, so maybe you add a second palletizer to increase performance, increase your performance score. Maybe you repair a problem in the palletizer such that the recurring downtime reason stops occurring, that's your availability score. Maybe you figure out what's happening there so you can reduce the rejects or the problems occurring and reduce waste at the palletizer, that's your quality score. And if you make improvements on those, you increase your availability, your performance or your quality, your OEE score goes up and that's how you know it's working.
34:34
KA: When you make any improvement, watch your OEE score. Does your OEE score climb? That's how you know if it's working or not. And then, once you've done that, repeat the process and as you repeat the process, you're gonna notice that your constraints migrate up or down the line. You're gonna find that maybe it's not your palletizer anymore, it's your filler or it's your sealer. That's gonna happen as you make these improvements and, again, keep measuring by your OEE score and keep repeating that process and you're gonna see those real actual tangible improvements. So, it's a virtuous cycle of sorts, the more you do, the better it will go. So once you get on that virtuous cycle, that repeated process, there are really a few best practices that you should consider and keep in mind, and I've listed a few of them here, there are more but here's the ones that came to mind first.
35:34
KA: One, have that clearly defined criteria for success, keep your can at 99 cents or achieve 95% accuracy on your due date estimates for your work orders, or whatever, an OEE increase of 5% this month. Have a clearly defined criteria for success and that way, you're striving towards something and you can measure your improvements in light of that criteria. Include all applicable departments in that process, get that team together. Start small with a pilot, don't try to roll out OEE to your entire multinational enterprise. I mean, by all means, please do but really, with success in mind, pick a line that you feel is the most impactful, start small, don't over-complicate and you'll be able to rapidly identify the sort of ROI you can expect via of this project, and you will learn so much on that first line. When you go on that first line, your assumptions will be challenged, you'll learn that the things you thought were a problem actually weren't and you'll be able to use that insight to touch the next line and the next line.
36:50
KA: Now, there are ways to do this so it's rapid and it's clear and it's accurate, but the point is, if you start small, you can take off a small bite and feel like you're making progress and then roll out further. Right hand-in-hand with that is the idea of if you use a solution like our OEE Module, use the built-in functionality wherever possible, use the ready-made components that the solution provides rather than complex custom solutions where possible. We pride ourselves and the OEE Module on the solution's customizability, right? When I worked in Support, everyone I talked to, just due to the nature of Ignition and Sepasoft, their stuff would look a little bit different and that's good. Everyone's needs are unique but our software and other solutions have rich built-in functionality that you can take advantage of rapidly, roll out quickly, learn what improvements there are and then customize, and then find places to improve and enhance your solution.
37:51
KA: In software development, we call it a minimum viable product, kind of like a pilot. You start with a small thing, you figure out what benefit it brings you and you use that to feed a future effort. Track machine utilization, not just uptime versus downtime, not just rejects and waste, track: Are you doing the right things with your equipment? Are you producing stuff you're selling or stuff you're storing? Is your equipment idle or in change-over or in production? Track that utilization in addition to uptime and downtime. So, in summary, the point of this is to say that the best way to improve plant performance is to work with your entire team to orient improvement efforts towards your constraints or your bottlenecks. The best way to measure those improvements is via how much of a difference it makes to your OEE score, preferably as calculated by a tool like our OEE Module for Ignition. Okay. Thanks, Don. Back to you.
38:57
DP: Listen, man. I totally appreciate that presentation, it was absolutely fantastic. So, I think I wanted to also then have an opportunity to maybe have a little bit of discussion as far as Kevin getting a little bit of input here. I know that you talked about how it's affecting plant performance, you certainly went over identifying constraints and I think we're in a position where we can absolutely see some of the benefits that can come from that. So Kevin, I know you've also worked on a lot of projects that involved OEE, you have many insights. I wanna open the door for you to share some of those insights you might have to go along with it.
39:35
KM: Sure. And Keith, thank you for laying that all out there so clearly and so nicely for everyone. I've worked with many customers who have not had that high-level view of how to get from A to B, and it's easy to falter a little bit but it's also easy to get started with this stuff and see where you can go with it. So, one of my favorite stories with some of the customers that I've worked with, one of my favorite customers, was a company that does metals recycling. And they had, as part of their process, something that they were doing that they didn't think was a big deal that was once every two hours, they would take two minutes and empty one of their bins along the line, which meant that they had to shut down the line and get a forklift and actually lift it and move it over somewhere and empty it out and put it back. It's about 120 seconds so they had it dialed in. They were very happy that they had a really good amount of time that they were able to do this in 'cause it's a little bit of a complex activity. And when they installed OEE, they were able to see that this two minutes every couple hours actually translates to being about 2% downtime.
40:58
KM: If you just do the math, 2 minutes versus 120 minutes, you can see where that comes from. And that 2% downtime for an operation that runs 24 hours a day, seven days a week, ended up being really significant. They were able to put in other procedures in place, not the folks who were doing the trading out but some of the management who were able to then see this. They were able to swap it out so it had two things that were right next to each other and they had about 30 seconds of downtime, and that reduced it significantly whenever they needed to swap out. And I think later on, they even reduced it down to 0% after they put something else in place there too. 0% from this one activity, which for an operation like theirs, that translates to hundreds of thousands of dollars or millions of dollars in savings over the course of time. And it really illustrates a couple of things that you said there, Keith. The importance of not only getting that information and getting visibility into that information, but also the importance of being able to have an organization that is going to do something about it.
42:13
KM: So, you have to have folks in place who are getting this information, you have to report it back, you have to have the right toolset to do a good job at reporting it, but you also wanna make sure that you have that corporate buy-in. You wanna make sure that you have folks available who are going to be able to act on it. In the example I just gave, if they didn't have... If they saw the 2% downtime and they said, "Well, we're just gonna live with that," If they saw the 2% downtime and they said, "Well, this process, we don't wanna take a look at improving this process," then they would have never realized those savings, they would have never been more efficient, which is the whole point of this. So, having the right folks involved and having the right buy-in, just to re-emphasize what you said there Keith, I think is really a critical piece of the overall picture of this, getting that information, and that can come right at the beginning or that can come down the line. Frankly, you can get OEE installed and set up and get the reports and then enact some of that change inside the organization based on the information that you're getting. It's nice to have that buy-in upfront but it certainly can have it down the road as well.
43:22
DP: Thanks, Kevin. I totally appreciate you chiming in on that. And maybe just one more question before we move into the Q&A, we have some of the folks that have questions here. But I'd like you to both give your closing thoughts about why Ignition and Sepasoft are a powerful solution for OEE in terms of software. Does it facilitate teamwork across the whole organization? I know you said you weren't gonna do a sales pitch Keith, but I think you should do a little bit of one here at least to sell it and Kevin, from the viewpoint of the Ignition platform and the combination. So maybe Kevin, you make your comments first and then, Keith, you and then we'll move forward into some overall Q&A.
44:02
KM: So, [chuckle] it's interesting being so familiar with Ignition and having so many contacts with so many customers with all of this. For me, from an engineering standpoint, one of the things that makes it such a powerful combination, the Sepasoft modules and Ignition, is the fact that it's all built on open tools and openness in terms of the platform and flexibility. As an engineer, that's really important for me to be able to have and design and help other folks design things that are really flexible and things that can adapt, that don't force the business to adapt to your tools, that you can adapt the tools to the business and you can really approach it either way but having the ability and having the flexibility in there is a huge benefit to me. If I was to pick out a single one, that would be the one that I'd pick.
45:01
KA: Okay. I'll dive in here too. Thanks, Don. Thanks for pressing me into this. I truly do think that the combination of Ignition as the best-in-class automation platform for HMI and SCADA and just general business automation in tandem with the Sepasoft OEE Module really are the best tools for really driving that virtuous cycle we described. Like Kevin said, we think it's uniquely customizable to your use case while also featuring rich out-of-the-box functionality so you can build what you need in a rapid and scalable way and roll it out to your entire enterprise quickly and rapidly and accurately and really get a real understanding of what's happening in your plants. Are you hitting your OEE goals? Why is your equipment down? We think it uniquely empowers your plants and lines and areas to do that just due to how easy it is to use, how flexible it is and how battle-tested it is by so many folks who have implemented it across their plants. Thanks, Don.
46:14
DP: No, thank you for the answer on that. Definitely appreciate that. If you're new to Ignition or you just wanna try it again, try Ignition 8 and the Perspective module for yourself. You can visit our website. You could download the full version, which takes about three minutes to download. You can use it in that mode for as long as you want, absolutely free. As far as the education side goes, once you download Ignition, we've also got a free online training website called Inductive University and you can learn all about how to use Ignition. We've also got a comprehensive online user's manual that you can certainly access any time you want. Additionally, from the viewpoint of Sepasoft, if you're looking for more information about Sepasoft, you can find video training courses about Sepasoft modules such as the OEE downtime module and others at sepasoft.com/learn.
47:08
DP: So with that, I think that's enough to move us into Q&A and maybe I'll start with the one that's at the top of the queue here, and I think I'm gonna ask you. This is... Dithmore has this question. Keith, I'll throw it your way. "As a systems integrator, we've received many RFPs including OEE functionality. Each customer and each RFP is more or less individual in case of calculations, design of dashboards. Every time when I propose to start with, example, Sepasoft standards, it's denied with a lot of arguments of company and/or individual requirements that that company has. It's maybe a German disease," he says, "Or a weakness. Or what can I do to argue and win that argument?" So, thoughts on that.
47:53
KA: Yeah, it's so interesting 'cause that drives right at that one slide we had about getting the team together. If you're having to argue to prove your point, maybe there's a better way to go about it. You can share, perhaps, what other folks have achieved in this space using the same tools or you can help them see what the benefit of OEE is. It's that idea of a guide post or a measuring point and without that, how can you make that progress? How can you improve? And so, if you help folks to see and understand why you're trying to achieve that and try to get them on your side rather than trying to argue them down, you might be able to get there more quickly. In addition, individual requirements, we really think it's a strength of our solution that you're able to fit those individual requirements. If you need counts or downtime or rejects in your dashboard or what have you, you build your own dashboards that emphasize your own points. So when I work with a beverage company or a dog food company or an aerospace company, their dashboards all look vastly different. And so, with our solution, you're not buying that sort of canned, it only does this, you only have this choice screen. Even with our newest tools, we really emphasize you building what you need to make it right.
49:21
DP: Thanks, Keith. Let's go to another one. "I appreciate your efforts. Can Ignition and Sepasoft-based OEE platforms assist in predictions?" Aaliyah has that question. Wanna respond to that, Keith?
49:33
KA: Sure.
49:33
DP: And maybe Kevin.
49:34
KA: I think it's... It's the best way to produce the data you need for those predictions. When our software produces data sets, uptime versus downtime, scheduled rate versus actual rate, out-feed count over an hour, that data is so clean and so pruned and so accurate that you can then use that data, that output data, easily to feed into machine learning tools on AWS or an Azure or what have you. Our data becomes the data that the other tools, those machine learning predictive insight AI tools, need to produce their data. Ignition consumes the information out of the equipment, we contextualize it in MES and OEE and then you can feed that into whatever solution you need to make those corrective insights. And we also help you understand that if you run at this rate, you're likely to finish this work order in X time, versus if you run at that rate, you'll finish it at that time. And your schedules in our software adjust in real time as you have problems on your line. If your line goes down, your schedule will lengthen, for example. So we help you in that way as well as far as a predictive manner.
50:53
DP: Kevin, did you have anything you wanted to add or any comment on that area?
50:58
KM: Sure, yeah. So, that's a great point that Keith made. And in addition to that, we have a number of our customers who are doing some of that machine learning predictive algorithms directly inside Ignition too. So we ship with that handful of algorithms that are accessible inside Ignition. Our sales engineering team is happy to talk to you and help point you in the right direction if you want to be served with that as well.
51:24
DP: Thanks, Kevin. Here's another question here. You mentioned tracking OEE for a line but can you track OEE for a production area, a plant or enterprise? Maybe that was an assumed answer but I think you need to talk a little bit more about the expandability of how one views an OEE across an enterprise.
51:42
KA: Yeah, absolutely. Both in general and in our product, the answer is absolutely yes. One of the core features of our product is that if you've installed our OEE Module on Ignition at three of your plants and you're then empowered to compare their OEE scores, not just per line but also per site. What is this site's OEE score, the combined OEE of all the lines? And we'd do that math in an accurate and intelligible way, we sum all those values and do all the math and give you that OEE score all the way down from the machine level. You can get the OEE of your filler all the way up to the OEE of your enterprise as a whole. That's working and running in the software now, you could do that today. But when you think, that's pretty important, right? You should have a corporate OEE. How well are we doing in a corporate way? And then you can measure that. In 2019, we had an OEE of 81% now we're 83. That's a huge improvement across our entire organization. Great question.
52:47
DP: That's great. Thanks for that. This is just a little note here from Jamie Whitley from Denver. He just says, "We love your product. Thanks very much." So, I thought I'd give you a little shout out of a customer endorsement there for your work there, Keith.
53:03
KA: That warms the cockles of my heart. That would make me very happy to see that. [laughter]
53:07
DP: I know. That's why I threw it in. So, here's the question. And I think there are several questions that lead in this direction of how do I start, where do I go to begin? So, I'll read this question and with the couple of minutes we have left, this may be our last question. Maybe we'll have time for one more but the question from Matthew is, "How do you recommend transitioning from manually collected data, MES, to automated data collection for production equipment and lines? What systems are in place to ensure useful data is being collected and reported?"
53:39
KA: Sure, I'll dive in there too. It sounds like this is a heavy user of that original MES, the Multiple Excel Spreadsheets.
53:47
DP: So, it sounds...
53:49
KA: [chuckle] We all start there. We all start there. It's like I say, the right thing to do is to start small. Pick a line. Pick the line that has the most PLC data where you have that in-feed, out-feed and reject. Don't think that you need in-feed, out-feed and reject every piece of equipment and super granular downtime. Just start. If you know how many pieces come into a line and how many come out, and the state of the important equipment on the line, that is enough to get going. Much money has been saved and made by very simple OEE metrics on a line. And then, once you've done it for one line and you just pitch that as, "This is the line we're starting with, it's the biggest problem for us," if you start there, you're gonna see some serious ROI there potentially. And when that happens, you're gonna get the authorization to acquire the equipment and the training and the materials necessary to roll that out elsewhere to the increased licensing costs or what have you. When you start small and you show the benefit, it empowers you to roll that out more broadly and convince others and bring everyone on board to be part of that team working together towards improving the whole plant or the whole site, or the whole enterprise.
55:08
DP: Thanks, Keith. Listen, we're coming to the end of our time. I'm gonna read one thing 'cause there were a lot of questions in this area. This comes from Arun and he says, "Amazing webinar. Thank you. Can't wait for the recording to share with others on my team." That's the whole point of these kinds of webinars is if you found it valuable, share it with others. We wanna make it readily available. With that, I think I would say, not that you guys have to have anything else with the minute we have left, Kevin, any final things you wanna say? And I'll end off with the final statement from you Keith. Kevin?
55:40
KM: Very much appreciate everyone being here and coming and joining us. I obviously, from an engineering standpoint, have experienced the power of these tools and I'm excited for everyone who's on this webinar who is going to explore them to see what you do with them, and what kind of efficiencies and improvements you're getting. So, we're always here to help and to talk and to answer any additional questions you might have so please feel free to reach out going forward.
56:11
KA: And I'll just top in here and second that. It's a total joy working with people who are all along the path towards digital transformation and improving their OEE scores. And the stories we hear back about the things people are able to do and improve are so striking. And so, we love helping people. It is truly one of the things that makes me get up and run to other's offices and say, "Hey, this person saw this improvement." It's such a great experience and we'd love to bring more people into that. So, if you have questions or interest or anything, please reach out, please get in touch and we're happy to help you start this process as well.
56:51
DP: Keith, that's fantastic. We're at the end of our hour. Kevin, thanks for being here to help out with the Q&A. Keith, thanks so much for a great presentation. With that, we concluded today's webinar. Have a great day.
Want to stay up-to-date with us?
Sign up for our weekly News Feed.