Ignition Community Live: OEE Accelerator Built with Ignition Perspective
50 min video / 45 minute readSpeakers
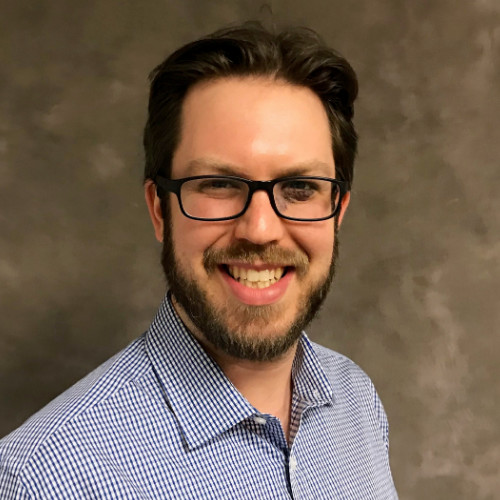
Sam Russem
Sr. Director of Smart Manufacturing
Grantek
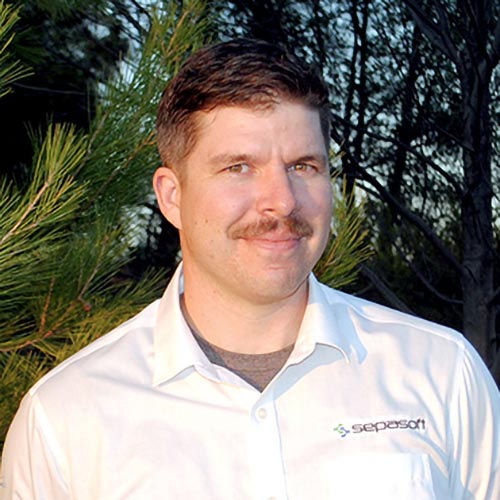
Mark French
Director of Operations
Sepasoft
Understanding how your manufacturing systems and assets are performing is one of the first steps to real-time operational insights, identifying opportunities for improvement, and intelligent Smart Manufacturing initiatives. Overall Equipment Effectiveness (OEE) is the essential, industry-standard metric for capturing asset utilization and efficiency.
Implementing systems for tracking OEE and downtime needs to be easy so that you can move onto identifying problems and developing Smart Manufacturing solutions as quickly as possible. Luckily, the Ignition Perspective Module can put mobile-ready OEE insights in the palm of your hand.
In this presentation, Sam Russem, Sr. Director of Smart Manufacturing Solutions at Grantek, will share an OEE Accelerator Built with Perspective, and how this application of Ignition can immediately improve your operations.
Webinar Transcript
00:01
Mark French: Alright, welcome everyone to Ignition Community Live. My name is Mark French, I'm the Director of Operations at Sepasoft, the Strategic Partner with Inductive Automation, makers of Ignition for MES. So our sole focus is MES on the Ignition platform. It's my pleasure today to introduce this topic and our speaker and presenter. The topic... Can you go back, Sam? Is the OEE Accelerator project built in Ignition Perspective by Grantek. So Grantek is one of our Premier Systems Integrator partners. And from Grantek, we have Sam Russem. And Sam is the Senior Director for Smart Manufacturing Solutions at Grantek. I've had the pleasure of working with him for several years now, as he and the Grantek team deliver really what his title says, MES and smart solutions for manufacturers in all different industries. So Sam's drawing from that experience. And I think he has a great presentation for you today. Sam, over to you, sir.
01:07
Sam Russem: Yeah, hey, thanks a lot, Mark, really appreciate that introduction. Yeah, and I run Grantek's Smart Manufacturing Solutions department. So the OEE Accelerator, which I'm gonna be demoing for you all later in the session, is really one of these solutions that our team has and manages around all about trying to get ahead of the problems of manufacturers and try to get real quick time-to-value. Then get out of that design purgatory phase and into the real part where we're implementing solutions really quickly from the get-go. So, happy to be here and happy to show you all some of the work that we've done. So what we're gonna do today actually is I'm gonna start by giving a bit of an overview of measuring performance and efficiency with OEE just making sure that everybody knows what we're talking about as we go through the rest of the presentation and understands what we're seeing, then we're gonna talk about bringing MES and OEE into Ignition with those Sepasoft modules that Mark was just mentioning that their company makes. Then we'll talk about the philosophy of accelerators and quick time-to-value. So the whole idea of Grantek making our OEE Accelerator and why we've done that, helps you and then really the main event of me showing some screens and doing some live demos and showing you how this whole thing comes together before we open things up for a Q&A.
02:22
Sam: So to get started, let's make sure that we're all on the same page when I'm talking about OEE. So OEE is Overall Equipment Effectiveness, the industry standard KPI for performance monitoring. For a couple of reasons I'm sure you'll grasp pretty quickly, right? One, very easy to understand. It is a score, a single score of your asset or line utilization, broken up into three components with some extra stuff on top of that, and I'm gonna go into some examples of how that works in just a little bit. It's readily measurable, so a lot of the systems that you're gonna have in place are probably already tracking the data that we need to do an OEE calculation, or it's probably a pretty easy lift to get them upgraded and get that information flow. So, good to know that it is within the reach of a lot of manufacturers. It's also immediately useful, but then extendable. So just core vanilla OEE and downtime measuring is usually gonna give you a lot of immediate value, and then if you do want to expand that you connect more to your ERP data or maybe add track and trace functionality or something like that, it's giving you a lot of that core functionality that's gonna let you expand that MES over time and continue to drive your operations and get smarter.
03:37
Sam: So I promised we would get a little further into the calculation of OEE itself. So this is the graph I like to kinda use to illustrate some of this. Imagine the total amount of time that we could be running a particular production asset or a line, right? Of all time, you might not be running it or planning to run it for the full amount of time. Maybe there's a holiday or an intentional break shift or something like that. So of all time, you have a certain amount that is your planned production time. OEE breaks down the rest of that. Of your planned production time, how efficient was I? So there's time that I was planning on running, but I didn't run. That is an availability loss, right? So an unplanned downtime or say there was a staffing shortage or something like that. Of the time that we were able to run, if I wasn't running maybe at the full capacity or speed that my line could be running, that's gonna be a performance loss or a throughput issue. And then finally, if we are running, if we are making parts regardless of the speed, but those parts aren't usable, they're failing quality checks and we can't sell them, that's gonna be a quality loss. And by the time we've added up those three losses, essentially, we have gotten to the overall utilization of that line or its OEE.
04:55
Sam: To put this with some more concrete numbers behind it, let's say that you were gonna run 1,000 units and you're not gonna do a schedule loss, you're gonna run for a full eight-hour shift, but then you have a downtime for two hours, right? So now you're only available 75% of the time that you thought you were going to, and realistically, you're only gonna make 750 units of that order. Now, if you're also on average only running it two-thirds of your top speed during that time that you're... During the six hours you're running, now we're only running at 66% performance, and we're down to about 500 units. Now, on top of that, if of those 500 units, only 80% are passing quality, we've lost another 20% off of our total production time and we're down to 400 units. So what you really see here is how smaller dings across these individual elements, availability of 75%, performance at 66%, quality at 80%, how that can really add up and at the end of the day, we're only making 40% of what we set out to make during that shift. So understanding kind of those losses and kind of where they're coming in and where you focus your attention, is all what OEE is about. That's the basics of OEE. If I wanna start to add this into Ignition...
06:15
Sam: That is where Sepasoft and Sepasoft's modules start to come in. I bring up this graph here of the Ignition software stack. People have probably seen a simplified, or this version of it, but what I really wanna focus on here is these partner modules. So of course we have Cirrus Link... Let's start over here, actually. We have Inductive Automation, these modules that I know everyone knows and loves, that's probably why you're on the call today. We also have Cirrus Link, which is some of these connectivity modules, but really here we're focused on Sepasoft and these MES modules. You see the OEE one we're talking about today, right here, track and trace, batch procedure, even some connectivity modules here for MES functions like connecting up to your ERP systems via Web Services or the Business Connector.
07:01
Sam: So these are one of the lesser known gems of Ignition, you get so much value out of the main platform itself. There's this modular approach that you're taking the elements that you need, but these third-party modules, these strategic partner modules, are also really important to be able to expand the capabilities of the overall system. How do you get to it if you're on Ignition's pricing page and just in that checkout counter? There is a strategic module section there, so you're gonna see sections like this around, if you want OEE Downtime, Batch Procedure, Track and Trace Module. So if you're looking at where to find these, you can find them directly on Ignition's website. Of course, you can also go to Sepasoft's website and get a lot more information from them. Or you can always give us, or whoever your local integrator is, a call, and we're happy to walk you through it as well.
07:52
Sam: So what do you get for that Sepasoft OEE Module? So it's gonna give you some data structures, there are some scripts and databases in there to help take the tagged data that you're getting from your automation systems and put it into that OEE perspective. And it gives you a bunch of modules and kind of components, like you're seeing on the screen right now, to help build some of those dashboards. So what Grantek has done, is that we've taken those components that you're getting from the Sepasoft system, and we've added our own flavor to it. We've kind of arranged some things, we've pre-configured a lot of it, to give you even more OEE value right out of the box of this accelerator, and get people started. So this is what we're gonna be demoing in a little bit, so I'm not gonna go too deep into it. But I do wanna talk about this philosophy of accelerators in general, we've heard me talk about that a couple of times at this point. So really, what Grantek's trying to do here, is that, we know there's your features and functions of Ignition and Sepasoft that you're gonna get from your purchase of that software, but Grantek really has been working with customers delivering smart manufacturing and OEE systems for decades, now.
09:01
Sam: We know the ways that people like to see this information collected and presented to them. We think we have a lot we can add to that, so we just put all of that together already so that you have a really great starting point for your OEE project. Some of our core design philosophies as we go into this, so we're really emphasizing out-of-the-box functionality and trying to not customize as much as we can. So we're customizing form and format, not as much function. And the value of that is that it helps us keep you up-to-date as Ignition and Sepasoft continue to improve their products. There's less of a chance of re-work as they continue to make their system updates, since we've generally stuck to the core functionality. It also just gets you up there and running on day one, we don't wanna have to go through a lot of extra troubleshooting and testing and things like that, this is a pre-tested system. And then we can of course adapt it and grow it and change it as we need to, based on your business needs. Which is really how Grantek approaches MES projects in general.
10:05
Sam: So Grantek does have... If you go to our website, you can find a lot of information on our Agile MES process. So we're taking those Agile philosophies of software design and applying them to MES projects, including the OEE Accelerator. So that OEE Accelerator is your minimum viable product, your proof of concept, your proof of value, whichever term you wanna use for that. But it's kind of that quick, okay, I can see how this might work in our environment, and then we can figure out how to adapt that to more processes or add more features that your company is gonna need before we get to a larger scale rollout.
10:42
Sam: Now, one of the reasons that that accelerator quick time-to-value philosophy is so important with OEE specifically, is that OEE should not be your end goal for an OEE project. OEE itself is a tool that you're gonna use in a larger continuous improvement program. OEE is just giving you the data and the information, so it's looking at all this information from your line, it's helping you contextualize that and kinda focus your efforts where you can have the largest impact and effect. But in itself, it's not really updating your process, you might get a little bit of a bump in performance from people realizing they're being measured and understanding, kind of, the measures and numbers that they're expected to hit. But really where you get the value of an OEE project is by looking at the data and using it to drive other projects or drive new behaviors, maybe even processes within your plants to actually improve the manufacturing operations, so...
11:44
Sam: So many people I see get stuck in developing the OEE tool, they never get to that continuous improvement point. We wanna beat that, we wanna beat that trend, we wanna have our OEE Accelerator giving you value very quickly so we can get to that fun, more continuous improvement part of things. So with that in mind, I've talked about this thing enough, let's go ahead and actually show it. So again, what you're gonna see is our core performance management and downtime analysis out of the box, everything you're gonna see here is gonna be in Perspective. We do have a Vision version of this as well, but Perspective's the new hot thing, so we wanted to make sure that we showed that off. And what you're gonna see are some operations dashboards, alarm and manual downtime entry, work order management and scheduling, analysis, and configuration. So quite a few things to cover. I'm gonna do a pretty quick version of it, if you wanna get into more depth on this, ask more questions about what our accelerator does or doesn't do, or how this could adapt to your process, I'll give you some more information on how to get in touch with us, and we can do a one-on-one meeting down the line with Grantek.
12:54
Sam: So hopefully, everyone now sees our plant overview screen. You'll notice that this is all just running in Chrome, Oh, sorry that's my OneNote. So this is all running in Chrome, this is all HTML5, and we are just kind of running this through a regular ISA-95 model. So you can see some of the elements of that here, where this is our enterprise view, and we can see all the places we have OEE installed. We have two sites, each of those sites has their own production areas with their own independent production lines, and today we're gonna be focusing on Allentown production. And we're mostly gonna be focusing over here on Line 1, so we're seeing some of the data come in. So again, overview screen here, multiple, you can see over the last 12 hours, how our OEE has been over time for the area and site level, that's more of a day-by-day granularity, 'cause we're looking at a bigger picture there. But let's dive in a little bit deeper and see how Line 1 is running. So I'm gonna go to our OEE dashboard. I'm gonna pick that line. And we're gonna get some of our metrics coming up in here. I do think this is running a little slower since I'm doing the presentation and the webinar and showing the demo, but just I'm sure you all get the sense of what's going on here.
14:23
Sam: So here's that line overview, right, and what we're seeing here is OEE data in two different time frames, so up here at the top, we have our data for the current production run, and down here we have it for just this first shift that we're in right now. So our production run has been much longer than the current shift, and we can see some kind of differences between the two time frames that we're working in. So in... We have our overall OEE score, we have each of its component parts here in availability, performance, and quality, and I can actually even start to make some interpretations about this right now, which is interesting. So if I'm looking at our overall run, how we've been going for the... Since yesterday afternoon, I noticed that we were barely down, our quality was pretty good, but we were running real slow. So that's maybe why we weren't having those breakdowns, maybe why quality was higher, 'cause we were running the system in a slower, more controlled way. This more recent shift, we've really picked up those performance numbers, but in doing so, our availability has gone down and our quality is going significantly down, so overall production across those two time frames, honestly, kind of around the same. Which is interesting, right?
15:39
Sam: There's other information that we glean from this too, so we do get some information on the durations of the current run in the shift, how long we've been up and how long we've been down, some numbers around actual production to feed into these values over here as well as some graphs showing how we've been producing over time. One thing that's really important is this little running icon up here, so you might have noticed this kind of ticking banner over here, the main dashboard here is gonna update once a minute, but this running icon is in real time because that downtime is so important for these OEE systems. So I just popped open our simulator over here, and I'm gonna say, simulate a false over on our box closure and with the way our simulator works, we can see that's blocking some of the work cells before it. So the second that I hit that, oh, see we have a big unplanned downtime banner up at the top, it says that our box closure is the root cause of that downtime.
16:40
Sam: It's giving us the reason code that that is down and we're gonna start to accrue downtime in this little line status history down here. In fact, if I expand this and dive into it a little more, you can see some of the downtimes that we've had earlier, so this is our overall lineup here, but it doesn't necessarily mean that everything on the line was down to the given point. So you can see those breakdowns in this section here, I see it's a little bit of red start to show up as we accrue downtime, and as you see as I'm scrolling over these, it's telling me what the main causes of those downtimes were, so all really good stuff.
17:17
Sam: On top of that, we do have alarm management within them, so of course you can click into the Allentown alarm banner here, I see I do have this unacknowledged alarm, I can go through and say, “Okay, I see that I'm gonna go fix my machine,” I'll acknowledge it, I'm gonna come into our simulator and turn things back on here, and this alarm is gonna clear out of the system. And as I go back to my OEE dashboard, we're gonna see that that banner is back to normal and we are back to normal production time. Yeah, there we go, see, back to running, looking good. So I wanna dig into downtime a little bit more because again, it's so important for these OEE systems, of course, it's great to have these parts of availability, performance, and quality, but really understanding your downtimes and why your line went down and where you should be focusing your maintenance or improvement efforts, is such a huge part of these systems. And I can't even tell you the amount of times we've installed an OEE system or seen one that's been installed, and it tells you that the number one reason for your downtime is unknown downtime.
18:34
Sam: We wanna fix that, we wanna be adding more information into the system, we wanna add more things that are used to be useful. So we can go through and work on some of that if I come into our run manager here and I'm gonna pick our line, here we can see all of the downtimes that have happened for our current run, and we can do this for other time periods too, like the last two or three runs, let's stick to this one, and here are the downtimes that we have, now, let's say, for example, that I wanted to add a manual downtime that maybe the system didn't collect. I have a whole interface to do that, I can say when it was down, I can pick my equipments, I can pick a default reason, and I can even add my note right here to explain why and how that happened.
19:19
Sam: I can also go through and edit some of the faults that have been automatically recorded by the system, so I have a 10-minute metal detector jam fault right here. Let's say that me as the maintenance guy who fixed this piece of equipment, and I'm going in and saying, “Actually no, that's not entirely right,” I could change that equipment to something else, or let's say actually that I wanna split this downtime reason, I'm saying of these 10 minutes, really, for the first five of those, that was something different. So I've split that event. This first one, this wasn't unplanned downtime, I know what I was doing, I was training Steve. And we brought it down on purpose to try to do some training for him, oops, I didn't mean to close it that quickly, I'll open it back up, or I'm gonna change this to a planned downtime, and you can see it's recording all these changes as we go through it, right, so here's my note right here, it's denoting these were split and it's denoting that I overran this unplanned downtime with a planned downtime, and we can undo all of that too. So if I am now the supervisor coming in saying, “No, no, that's not true, that's not how I wanna allocate that,” I can, “No you weren’t,” I can put in some notes onto the downtime still, I can confirm that. I can even revert to the original reason.
20:45
Sam: So it's now, the overridden check went away, and I can even revert the split so that now it is all, one of them even kept my note in there too, which is nice. So the reason this is so important for a lot of OEE systems is we don't want perfection to be the enemy of good, if we don't have great fault information coming out of our systems, or if we know there is going to be some manual intervention that happens, we don't wanna stop our OEE project until we have completely perfected our automation systems, we wanna make progress with what we have, right, so even if you don't have all of the fault information from your system immediately, or even if there are mistakes that just naturally happen sometimes as we're working out some processes, you have the interfaces that you need to go through and do some of this manipulation that you need to, manual entry, if that's valuable to you. And again, one of the reasons this is all nice, looking at all this downtime here in the chart, yes that's valuable, but I wanna get a little bit more information, so I'm gonna jump into our analysis selector over here, so I can come to our line downtime, I'm gonna select Line 2 'cause I know we have some good data in there, so what this is now showing, I'm even gonna expand this time frame. Let's go to the beginning of last week.
22:08
Sam: So there we go, there's our chart, so as you can see here, for each of these days now I could see we were idle for a bit, we maybe tried to start up, but went down and had some issues for a couple of days with that before we were able to get the system up and running again. So, good information on the downtime that we had. Since we were just playing on line one, I'm gonna jump in there and look at kind of our more what we've been doing just today for the demo. So again, mostly I've been running for the past couple of days, but we do have some unplanned downtime in here, and I wanna learn more about it, so I can click on this “Unplanned Downtime,” I can go into “Downtime Reason.” And now of those 17 occurrences, I'm getting more information on exactly what went down, right, so today, we've mostly been having an issue with the metal detector, yesterday it was more varied, the knife was jammed a couple of times, the metal detector was having issues. But our box closure was also an issue then too, right? So this is kind of giving us, and there's all sorts of options around, what you can drill down into here, you can slice this by what product you were running on the line and things like that, so a lot of power here. Again, we're not just collecting the data for fun, we're collecting the data, so you can go into these analysis screens and really slice and dice it to get to the root of your problem, and come up with an action plan on how to fix it.
23:31
Sam: Okay, so that's a lot about alarms, it's a lot about that kind of overview screen. There's two more quick things I wanna show that come with the OEE Accelerator, one, is I just wanna point out that we do have this configuration manager here. I'm not gonna get into this too deep, but a lot of the things that you need to do for overall administration of this system are gonna be right here in this portal, so you don't need to open up the designer, you don't need to have a knowledge of how Ignition works for training, for a lot of things, like managing the types of equipment that you might have, say, what types of shifts and people that you have on those shifts, right. Even coming back, creating specific products and materials, you can do all of that right here if you have a new material or a new skew that you wanna run, and security as well, if you wanna get into who has permission to do what at what points, all right here within the application, good stuff.
24:26
Sam: The other thing, so I mentioned the different materials that you could run, there is a scheduling system within the OEE Accelerator as well, so I'm gonna come back into here, I'm gonna look at our scheduling tab, there's a couple of ways that you can do this, again, I'm gonna do a light touch here, we can go into more detail if you would like in the future, just reach out to us at info@grantek.com, but what I really wanna show is what you can do in scheduling, and what you need to do with scheduling because you don't need to do a lot. If you do not, are not ready to kind have a full scheduling system in here, or maybe you have another system of record that handles all of your scheduling and you don't wanna immediately take on the complexities of tying into that, you don't need to run this in a scheduled mode, you don't have insights to some data like, you wouldn't know what material was running on the line to say, “Does my metal detector go down more running product A than product B,” but you will still get your general OEE and downtime information and things like that, whether you run scheduled or not, either way.
25:32
Sam: We do have these schedules in here and all of these work orders that we have assigned, right, I can right-click on our schedule and make a new entry to where I can say I'm gonna run Work Order 2 and we're gonna do it on Line 1 for 500 units, and I'm gonna save it and it's gonna auto-calculate how long it thinks that's gonna take and puts it into my schedule and we'll change it over to that when we hit it. I don't wanna do that right now, so I'm gonna delete that entry... Yes.
26:01
Sam: We can also... Again, if you're not maybe planning ahead of time, or if you do have emergency work orders that you need to fill, you don't need to have everything scheduled either. You can go into your production run and production control, select your line... And I can just say, "You know, I need to be running a FG001 right now," and I can just start that changeover right here from this screen. We can also schedule work orders that way too, if we need to. Again, I'm not gonna do that to mess up the data, but it's all an option that you have here. It also does support rolling changeovers or entire line changeovers, so... Right, so if you're gonna say "I've run product A, now I need to clean everything out, now everything is running product B at once," we can do that. If you are doing a rolling changeover, like in the beverage industry a lot, where you might run flavors back-to-back, it can handle that too as you index across different work cells of the line.
26:57
Sam: So that is a lot of it. That is what I wanted to show. Again, coming back to this main screen here to see our overall OEE performance. But yes, that is Grantek's OEE Accelerator, and a lot of the features that you get for that out of the box. If you wanna learn more about anything I just showed you with the OEE Accelerator, with Sepasoft MES in general, Ignition integration questions, general integration questions... If you wanna learn more, reach out to us over at Grantek. You can visit our website, grantek.com, or you can always email us at info@grantek.com, follow me on LinkedIn and things like that. Easy to stay in touch with us. Just Google around a little bit, you'll find something real quick.
27:37
Sam: And with that, I'm gonna get to the Q&A portion from our audience. First things first, Muhammad asks, "How is it possible to calculate OEE on a continuous production line, say, iron ore concentrate process? Is OEE still a good application for that?" Very good question, especially since, yes, a lot of kind of the origins of OEE are from discrete, like in packaging manufacturing, but you can, and Grantek has, applied these principles to a continuous process before. What happens sometimes when you do that is maybe all the data isn't as real time as it could be. Scrap can be a big issue, because, especially in continuous processes, you could be reworking a lot of scrap, or maybe you dump things into a tote, maybe you don't measure that until kind of the end of a process, and at that point, your production run is over, so you're reporting scrap far after the fact. You... We can accommodate for all of that, and we've done that in the past, so... You know, again, it's a... It's a standard; it's a template, something that we can follow, but it's not set in stone, so we can be adapting things for continuous processes.
28:46
Sam: The other thing I mentioned in that is a similar metric to OEE that can be used for a continuous process sometimes is called “Time and State,” which is, instead of kind of measuring that performance and availability and quality, what it's doing is measuring how close you are to certain key performance indicators and critical control points within your continuous process, so it's more kind of measuring how close you are to an ideal state. Our OEE Accelerator does not do that, but if you were curious to learn more, I'd actually encourage you to look up MESA International, M-E-S-A, has a really good paper on Time and State and how to use that, so I'd recommend going and giving that a quick lookup. Mark, I see you joined us again. Any other comments that you wanna add around continuous process?
29:34
Mark: No, I think you've covered it well. And we've got a load of questions here, so...
29:39
Sam: Oh, do we? Great. I'm gonna show all the ones that we had beforehand I haven't even dared to look at, so... And Mark, actually, give me a second to do that, because the next question is for you. David asked, "Can you cover how Tag Historian data and Python, and how you can manipulate that in Python and maybe use that for your OEE calculations?" So if we're talking about what goes into those OEE tags, how does then Historian and Python kinda play into that, Mark?
30:07
Mark: Yeah, a good question. I don't wanna get bogged down too much into technical details, so just at a high level first... We're pretty flexible with the OEE Downtime Module on data ingestion. So, like Sam showed, we want to get data into the... Into the module live from Control Systems; that's usually best, but, you know, if it is manual or after the fact, we can handle those as well. So, I would put this type of approach in that after-the-fact category, and we do have features built into the product to do that, to take in data with a timestamp, so that we can understand that properly. Again, I'm not gonna get into which Python scripting calls are necessary. Some of that is supported out of the box in the Ignition platform, with the Tag Historian features, and some of that also is part of the feature set of the OEE Downtime Module, so... Great question. Sorry if I didn't get into the technical detail that maybe you wanted there. If you have further questions and you're working with Grantek, great. Otherwise, support@sepasoft.com is available to you, and we can either handle that with our design consultation team, which is... It's not a replacement for a systems integrator. It's more of coaching around how to use the products. So... Great question, back to you, Sam.
31:32
Sam: Cool. Thanks for that, Mark. Yes, even that was a little more technical than I got, yeah. So, Brandon asks how generically OEE can be used, versus how much it needs to be tailored for a manufacturing process in a company's objectives to be effective. So, this is one that I really love diving into, because I see a lotta people get hung up on it. You know, OEE is designed to be a fairly standard KPI, and I think there's a lot of value in that vanilla version of OEE, both in that I think it's a very good enough metric; I think that a lot of the tweaks that some people can make to it, you know, don't always add a lot of value, but it also... You know, it is. It is that standard, so, in theory, any continuous improvement person that you have coming in, if you're using vanilla OEE, they should have a very good understanding of what that is and what it means for you, right? So...
32:30
Sam: Hopefully, if you are customizing, you're customizing for purpose, right? If you're customizing that OEE, hopefully you have a real reason for it, but I'm hoping that the complexities that we're adding into the system are in a particularly complex machine interface or maybe to really do some data exchanges with the ERP system or to add some kind of extra screen or functionality that's really custom, as opposed to taking this formula that's pretty well established in the industry and trying to fool around with that. So that's my recommendation to take.
33:05
Sam: Next question that I had was from Andrew asking, if we needed our tags structured in an ISA-95 equipment model for OEE to work? I really liked this question. So the answer is technically no, but you almost definitely want to do it. Because, yes, these are again it's general availability, quality, performance, good parts, bad parts, downtime codes, like the data that you need for individual work cell or a line, fairly simple and it seems pretty achievable, right? But when you start to kind of roll that up and start to use this for your whole enterprise, a lot of that roll-up comes from organizing things properly in the tag hierarchy. So if I'm gonna have a bunch of machines that are summarized into a line and then a bunch of lines summarized to an area, area summarized to a plant, that is your equipment hierarchy model. So you get a lot more value out of the box if you're kind of adhering to that and if you're doing all these kind of connections manually.
34:09
Sam: It also is gonna help give you a pretty standard reference, usually across your Ignition architecture, it's gonna... The whole idea of modeling is it's gonna make it more intuitive and easy for people down the line to understand what they need to understand about a piece of equipment, rather than all of the technical details of how that data got to where it needs to be. So I think there's a lot of value to that modeling, yeah... And it's a fairly easy exercise to do. I definitely would recommend looking into it. Mark, do you have something that you wanted to add to that too?
34:43
Mark: I think you covered it well, but there was another question that's kind of analogous here, or maybe alongside it from Ivan. “What are the minimum requirements at the level of information in the control systems, for the calculation of OEE?”
35:00
Sam: Yeah.
35:04
Mark: Similar topic, the first, "Hey, how do I organize this information here," Ivan wants to know. Well, what information do I really need? So I have a way of answering this, but I'll say that and then Sam, I'll let you expand on it. At its simplest form, you need some production counters, things like Infeed, Outfeed, Waste, as well as the status of the equipment, the state, is it running, is it down. With that, you can get away with just that. More is better. As far as context, we'd like to have start/stop signals and things like that. But at its core it's pretty simple, so Sam, what do you look for from customers and say, "Hey, this is really what you need data-wise to get started, to really get that value."
35:53
Sam: Yeah, I think that you're totally right, Mark. So yes, the good parts, bad parts, those part counters, general availability was one of them too. But then the other thing that I usually look for is to have a good downtime system and to have things that are... Even if the downtime, the reporting isn't perfect, they should be reporting some level of downtime, if you're not there yet, I would just recommend that you kind of start with that, because you're gonna get limited value out of the OEE piece until you really have that downtime information too, it's kind of more of a maturity thing. So I would say, if you don't have that downtime data, that's probably where I would start, but once you do, you probably got the rest. Cool, good questions. Another one from Andrew that I did want to bring up, was he was asking if Ignition has a base OEE module or if they rely on Sepasoft for those functions. So Sepasoft, it is the module, so yes, it is made by a different company, but it is a strategic partner, Inductive is not making their own OEE module on top of that, so Sepasoft is the module.
37:00
Sam: It does also make me think about... One of the things that I've run into a lot as an integrator, is the amount of times that we've had to go in and essentially rip and replace custom home-grown OEE systems. So again, with that core calculation being pretty simple, it seems pretty achievable for people to go and put in some pretty basic OEE without paying for these modules, but as soon as you start to get to scale, as soon as you wanna start doing scroll-ups, that deeper analysis, as soon as you want help from another integrator or from another software company or something to move these things forward, I think going with that Sepasoft standard really helps you a lot. And it also kinda goes back to that point I had earlier about, the OEE installation should not be the hard part where to focus on what you're doing. You wanna be focusing on continuous improvement and optimizing your process and making things better. So why would you spend all of this time, creating your own spin on OEE when we already have something that's gonna go out there and cover most of your use cases and really let you get to the more value-add part of it.
38:07
Sam: So I maybe took a bit of a tangent there to get to a point that I wanted to make, but that's definitely I think an important part of the way that Sepasoft and Inductive, your integrators all work together to let you focus on the things that are much important for your manufacturing lines. Okay, so I'm gonna try to look at a couple of the questions that we have coming in online, so going a little live here. One thing that I've seen come up a couple of times, it looks like in here, I see Lynn asked about it, I see Mark asked about it, was…
38:40
Sam: Does the work orders and scheduling need to live in the Accelerator and those interfaces or can you get some of this information from an ERP? Kind of genericizing some of those questions there a little bit. The answer is both. So usually, especially when we're doing like a proof of value or some type of minimum viable product, I don't recommend jumping straight into ERP integration from there, or you do something very basic just to prove that you can do that ERP integration without necessarily going through the actual integration of everything, right? So maybe it's something simple like, I'm just sending up finished goods, or maybe I pull down all of my work order information, good for a minimum viable product, and then when we get to... And then we get to full... No, no. We do all of our scheduling in SAP, we wanna download all of that to the OEE system, once that run is done, we want... We either report back up finished goods and scrap and things like that. Absolutely doable in the system, not recommended for a minimum viable product. So yes, you can be scheduling entirely in the Accelerator, you could be scheduling, or you could be running unscheduled, if you don't want to deal with all that, you can be interfacing with ERPs or other scheduling systems as well, or work order or schedule information. All of that is on the table... Yeah.
40:00
Mark: This is a question from Tim. I think this is a great question. “What's your view on the Accelerator for high mix, low volume? Is that a use case that is well covered in the Accelerator? And if not, what are your recommendations for them?”
40:16
Sam: Yeah, no reason that you can't, honestly. So one of the nice things about these types of systems, again, it can make your work-order management maybe a little bit tough if you're doing changeover after changeover after changeover, right? So that's probably a good use case where you probably either do want to run on schedule or make sure that you're immediately tying into that master scheduling system or doing that as quickly as possible. But yeah, there's no reason that you can't have a whole lot of different work orders and materials in there, that maybe have very different run rates or kind of OEE targets for each of them based on how you expect for that to run. So, yeah. It really shouldn't be an issue at all. We have also done this at very high-speed volumes as well, so food and beverage, high-speed bottling lines, as long as that information coming from the automation systems is going well... Yeah, we should be able to handle that without a problem. I see a question in here kind of around, "How do you register problems with performance?" I'll maybe kind of make sure that we're clarifying the performance metric and part of the OEE conversation there, so you have again, that availability.
41:27
Sam: How long was I up? Quality, how much did I have to scrap? Performance is where they throughput or a speed of line value, right? So, if I'm supposed to make 1,000 bottles a minute, but I'm only running at 800 bottles a minute, gee that’s really fast. So that's kind of where that performance number is coming in. Of course, performance and problems with performance can be a very big category, and I'm gonna take that question very literally, so that would definitely involve some more kind of consulting to make sure that we have that fully ready to go.
42:00
Mark: Yeah. Well, I think you hit it, but I wanna point out, this is one of the great benefits of OEE, right? Is that self-diagnosing nature of the metric. The fact that you have issues with your OEE performance, means you know you need to look at rate and you need to examine that in your continuous improvement process as opposed to your availability quality scores. So that independence of the factors guides you in your continuous improvement process for what you need to focus on. I think that's one of the reasons why OEE is an industry standard metric, so... Great question.
42:41
Sam: Yeah, absolutely. Here's a good one from Andrew that I've seen here too. So he's asking, "Does OEE Accelerator calculate OEE at the line level, based on component machines and how is that done? Or is it measured at the line out of one point, it sounds like, and then also just happens to measure machines?” So the answer is, again, it can kind of work either way, so if you do just want line-level OEE, and you don't care about the individual equipment, we can do that. Or we can look at a bunch of individual pieces of equipment and then summarize that based on usually your bottleneck machine and use that to represent the performance of the overall line, right? So an important aspect of that, and one that I didn't cover actually in the demo, is that you don't need to have complete OEE for every single machine to have this be effective or to get it for a line. So, what I mean by that is, if you have a 12 work cell line, your bottleneck machine and kind of two or three others that are the most important to you, and all the other ones there, may be very old legacy equipment or aren't on the network or something like that, it's not really worth it to bring all those online, you don't need to do that. You can just kind of pick the work cells that matter most to you, you could still see information at the line level.
44:01
Sam: Again, this is a tool, it's adaptable, kind of fits to what you need on your side, so either way. Long and short of it would be, yes, you could do every machine on the line and summarize that up, you would do some machines on the line and summarize that up, or you can do no machines and just measure at the line level, all of that works and it works just fine.
44:22
Mark: Can I queue one up for you, Sam?
44:25
Sam: Please do.
44:26
Mark: Louis asks about the Accelerator. He said, "What is this practically? Is this a module for download?" And how does he incorporate his existing SCADA Perspective project with the Accelerator?
44:43
Sam: Great question, and a good thing to clarify too right, because there are three players involved here, so there is Ignition and Inductive Automation, we all know and love, clearly because you're here on their Community Live, so I'm assuming everybody knows Ignition, on top of that, you have your Sepasoft modules, so your strategic partner modules that are plugging into your Ignition instance. Now, the Accelerator is a Grantek product and solution, so Grantek, a systems integrator across the US, and Canada, we have assembled those core components of that Sepasoft module and created our Grantek OEE Accelerator. So if you want that, you're giving me or my team a call soon after this, again, if you wanted to do something with Sepasoft OEE directly and kind of spend your own stuff, you could do that. The reason that we made this is that I think it's gonna be a good place for everybody to start off and get these initiatives kicked off, so that's part one to understand that definition between Ignition, Sepasoft, Grantek, the other piece of this is, can it be incorporated into another Perspective project, and the answer is yes. It definitely can, so it could be just its own project that you're launching on its own for certain reasons, you could take the elements that we have of this and put it into another Perspective project.
46:01
Sam: Yeah, it's not gonna come out of the box that way, we can't have it automatically configure to everybody's Ignition environment, but that's one of those small tweaks that we can put in there to, as we're doing that minimum viable product, to make sure it's gonna work with your whole system as long as, including other things like again, what the specific machines we do, what specific colors we use to maybe match your corporate standards, any kind of custom report, things like that, all things that we can build into this over time, including integrating it into other Perspective projects that you may already have. I do have a quick one in here from Matt, too, that I can answer really quickly, which is if you are gonna change downtime data from further in the past, from a previous day, does your OEE data re-calculate for that day? The answer is yes, if you're gonna run a report on it, you might need to go and re-run that report, but yes, if I go back three days ago and say, actually there was a 12-hour manual downtime in here, or no, we didn't make all of that, yes, it will re-calculate those OEEs for you and that'll be reflected in your system of records which tracks those changes too.
47:10
Sam: And you know what I actually really like this last-minute question from Tim around, do these applications run on generic PLCs, connector to sensor, connected to sensors or HMIs, or maybe the system architecture piece of this, good point there, right? So again, the Sepasoft module and Grantek's Accelerator all run in Ignition, so you're gonna have your Ignition server that is running your SCADA system, it has that MES module, and all of our screens are driven from there, the data itself is either coming from tags you already have today, in Ignition, and you know how those got there because you probably did it, or by accessing new data sources in the field, so tying in new PLCs, adding those into Ignition, making that available in the data model, and then of course, getting that over to the core OEE Accelerator screens, it could also be something like an IIoT device though, so it doesn't need to be a PLC if you do have something out there that's talking MQTT or something like that, collecting that information. We can capture all of that in Ignition as well, and also just use that like any other data points.
48:21
Sam: And then last point on that real quick, is that one design question that we run into as we talk about actually implementing these for customers is there usually is some type of data manipulation that has to happen somewhere, so maybe exactly figuring out your good or scrap parts, maybe counting what's available versus non-available time, there are some design decisions in that, right, is that something that we wanna be calculating at a PLC level and our automation systems are automatically calculating that for us, or do we maybe wanna do a Python tag in Ignition where we're taking information for a couple of different tags and then summarize that into an availability number, these are all options, so there are some design decisions around where we might calculate what that we'll figure out as we talk to you more about your specific implementation. Great.
49:14
Sam: So I think that that is probably a good one to wrap things up on, I do see that there are more questions in here, I'm sorry that I didn't get to answer all of them, if we didn't get to what you wanted to do today, please feel free to reach out to whoever you're most comfortable with between Inductive Automation, Sepasoft, and Grantek. And we'll be happy to get back with you. Thank you all so much for coming.
Want to stay up-to-date with us?
Sign up for our weekly News Feed.