Combining the Best of OT and IT
Why Industrial Organizations Need to Bridge the Gap
15 minute read Download PDF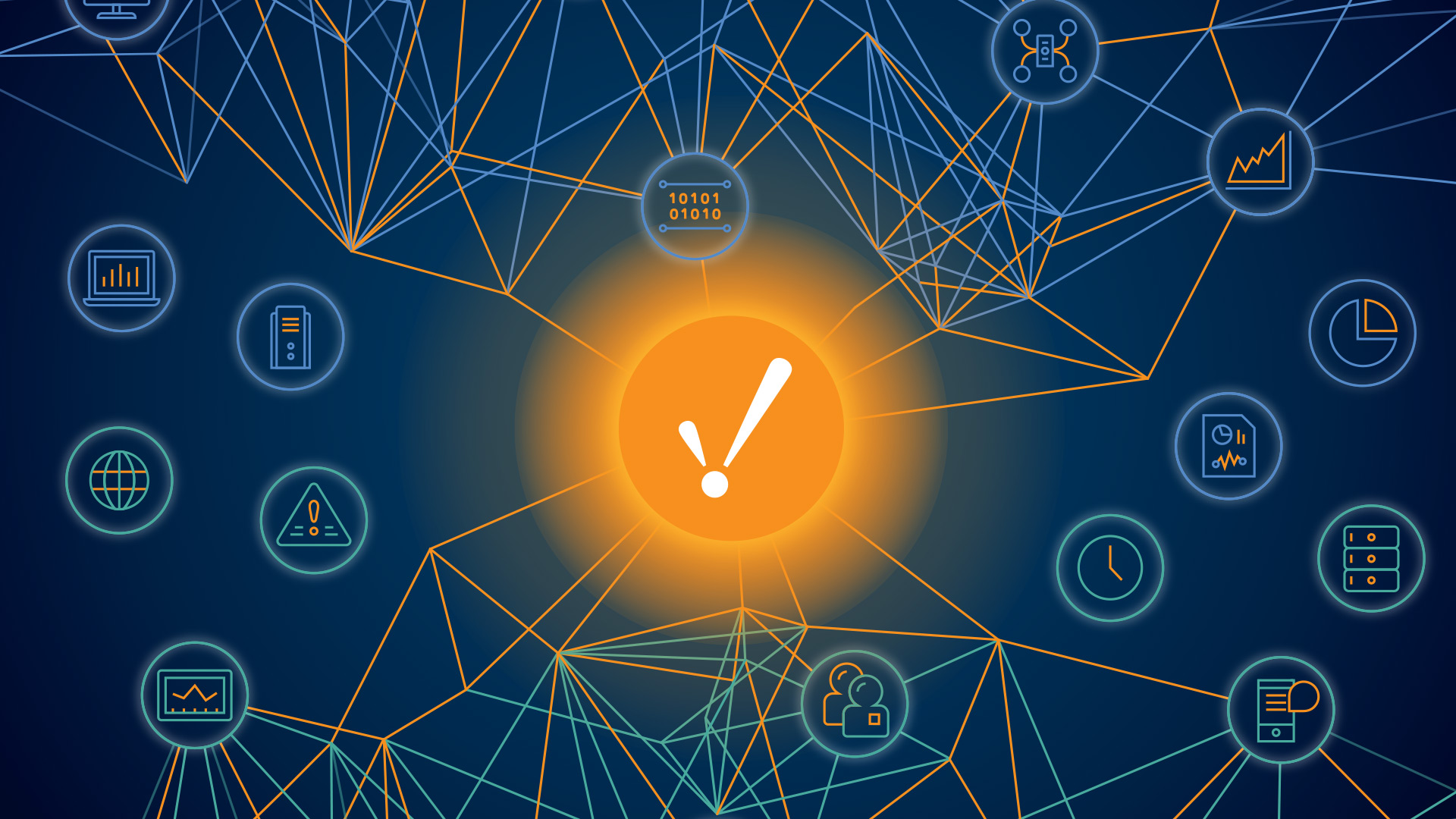
Disruptive technologies are causing major waves in the industrial sector, enabling organizations to vastly improve the accessibility of data in order to connect people, organizations, and technologies.
These disruptive technologies are allowing organizations to directly access plant, manufacturing, and remote industrial device data. No technology has been more disruptive in recent years than the Internet of Things (IoT).
The IoT refers to the network of physical objects made “smart” with electronics, sensors, software, and network connectivity, allowing these objects to collect and exchange data. The IoT is rapidly expanding: by 2020 there will be an estimated 20.8 billion devices in the IoT, and more than 30 billion devices will be wirelessly connected.¹,² IoT ushers in an era in which objects can be monitored and controlled through existing network infrastructures, including the Internet, to improve efficiency, accuracy, and cost. In the consumer market, this has led to a flood of products such as smart door locks and connected home appliances.
Data is Revolutionizing Industry
Industrial organizations and system integrators are starting to realize the huge benefits of IoT and have coined their own term for it: the Industrial Internet of Things (IIoT). Confronted with a world where data is increasingly infused into every aspect of business, forward-thinking companies are now investing in data like never before.
General Electric (GE) and Siemens are two major companies leading in what Smart Industry Magazine calls the “ongoing digitization and ‘data-fication’ of industry.” For example, GE has shifted its entire approach to the value of data in recent years by investing $1 billion into rebuilding its software and analytics approach, and hiring a team of 1,000 software engineers. GE continues to build big machines such as locomotives and jet engines but now also incorporates intelligence within its machines to collect and parse data. Through these efforts, GE expects to achieve a 1% improvement in productivity, which for a company of its size can equate to hundreds of billions of dollars.⁴
Many other organizations are also embracing IIoT. A survey by Gartner found that the number of organizations adopting IoT will reach 43% in 2016, and that includes many industrial organizations.⁵ As more organizations move to adopt IIoT, operational technology (OT) and information technology (IT) are converging.
Adapting to this convergence will require industrial organizations to change the way they think about OT and IT. Unfortunately, industrial organizations have kept data and control on the manufacturing floor, residing on restrictive and costly systems, unlike systems found in IT. Essentially, this has stopped useful data from reaching those who need it on the enterprise level to aid in their decision-making.
With the great need to leverage IIoT to make industrial data more accessible on every level, it is important for industrial professionals to understand why the convergence between OT and IT is taking place. Furthermore, they should actively work to align OT and IT. Although OT and IT have been viewed as two distinct domains for decades, they must now work together to start bringing the IoT to the industrial level.
The OT-IT Divide
You are most likely to think of IT as the software, hardware, networks, communication technologies, and systems that store, process, and deliver information to all aspects of an organization. IT professionals are experts in networking technologies, and are very familiar with rapid scalability, cloud infrastructures, web-based deployments, and technologies such as SQL, Java, and Python.
OT encompasses machinery, physical plant equipment, and remote industrial software and hardware. OT professionals focus on systems used for monitoring and control. They are adept with Programmable Logic Controllers (PLCs), Remote Terminal Units (RTUs), Human-Machine Interfaces (HMIs), Supervisory Control and Data Acquisition (SCADA) systems, and embedded computing technologies.
OT and IT tend to use different approaches to problem-solving. IT implements solutions using a top-down approach, starting with the big picture, such as an organization’s overall needs. The big picture is then broken down into sub-components, and solutions are developed for each sub-component. The top-down approach forces you to understand the method of the solution and not just the problem.
OT professionals approach solutions from the ground up, starting from the individual components to build a more complex system. SCADA environments collect data from different processes on the plant floor, so those who work in OT must figure out how to integrate all the systems to work together. Because most OT technologies are proprietary, many SCADA solutions can be difficult to integrate. OT professionals work with sensitive, mission-critical, high-risk systems; therefore, their foremost concern is security, which is why Internet and Wide Area Network connectivity has not been a priority for them.
With the introduction of smart machines, Big Data, and the Industrial Internet, OT and IT are finding themselves needing to solve the same problem: accessing industrial data. Unfortunately, since OT and IT have existed on separate planes, neither side truly understands the needs of the other from a solutions standpoint. IT professionals may not understand the reasons why OT still uses legacy equipment and deals with proprietary, astronomically priced solutions. OT professionals may not have in-depth knowledge of SQL databases or the breadth of security protocols used in IT today.
Even with this divide, a great opportunity exists for OT and IT to come together and leverage each other’s strengths to arrive at a truly disruptive technology. Keeping OT and IT separate is an Industry-3.0, pre-IIoT mindset. To meet the demands of today’s data-intensive environment and enter Industry 4.0, enterprises must work to align OT and IT.
Benefits of OT-IT Alignment
Gartner defines IT-OT integration as: “the end state sought by organizations (most commonly, asset-intensive organizations) where instead of a separation of IT and OT as technology areas with different areas of authority and responsibility, there is an integrated process and information flow.” The alignment of OT and IT brings forth many major benefits. One of the biggest benefits is improved decision-making. By having access to a greater quantity of high-quality data, every person in an enterprise can make better decisions more often. If machines and devices are not connected to an IT network infrastructure, then the other parts of the enterprise cannot take advantage of the useful real-time data and operational intelligence.
Let’s look at an oil pipeline as an example. On any given installation, there can be over 10,000 miles of pipeline, thousands of PLCs and devices, and miles of wiring. In a typical operational environment, only critical operational data is used for monitoring and safe operation. About 80% of the data is left out on the field. IIoT can bring all of that pipeline data and much more to the enterprise level. Additional data on the health status of all devices on the network aid in decisions such as whether to send a repair vehicle or to solve the problem at the local level.
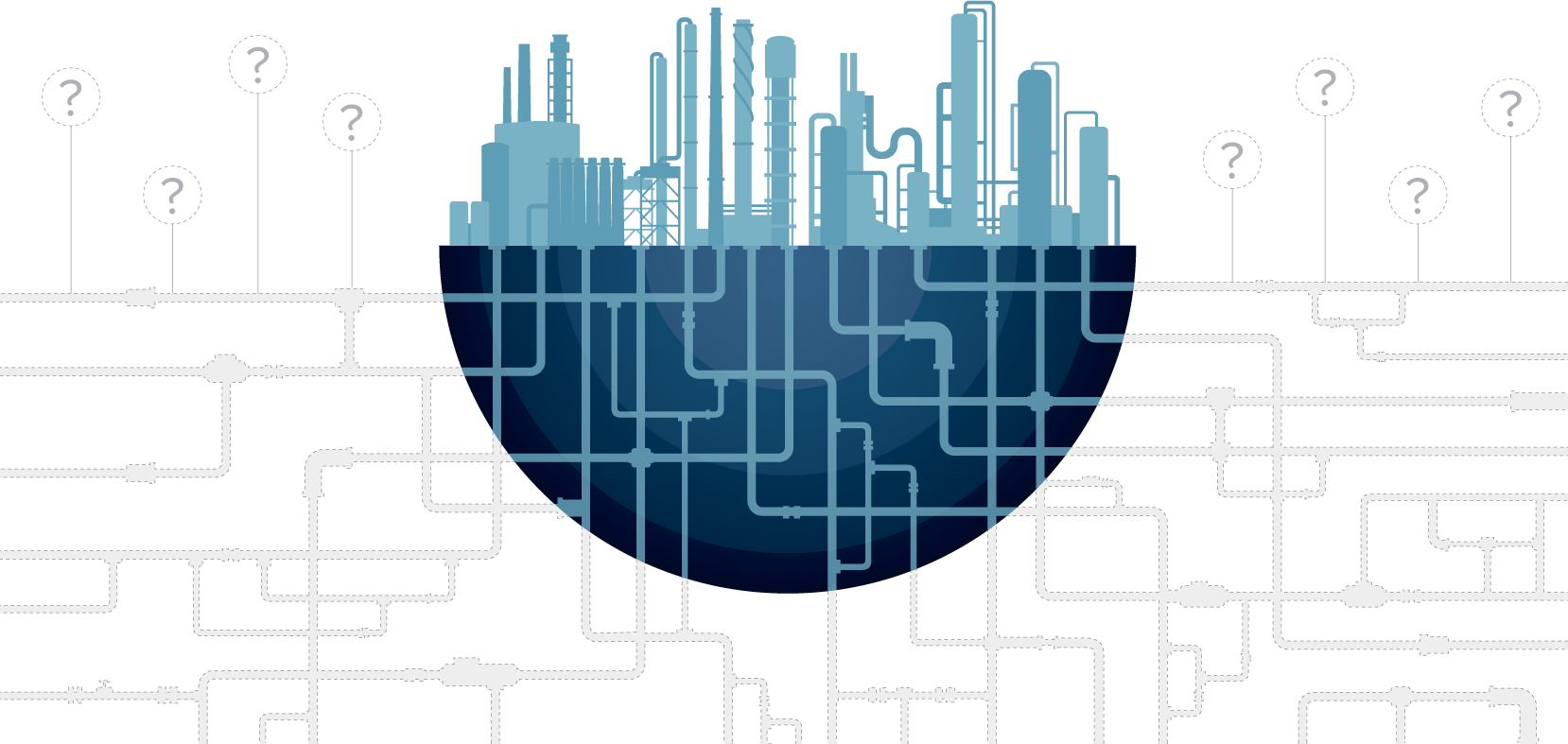
Other benefits of OT-IT alignment include cost reduction, optimized business processes, lowered risks, faster development and integration times, and standardized communications and control. Connecting OT to the enterprise level can be a large cost, and OT can benefit from the affordability of maintenance and licensing costs that IT has to offer. Additionally, now that data can be easily accessed, those in OT and IT can share data across an organization to make better decisions as a whole. By integrating OT and IT systems, the overall system has greater value, optimizing the way companies share information.
OT and IT alignment lowers the risk for an organization. Not only do you get improved data accessibility, you also get the stability and fluidity of an IT infrastructure for an OT environment. Putting in an infrastructure to access a greater volume of high-quality data from the OT side can be done without impacting the current SCADA system. With Cloud and virtualization technologies, plant- or manufacturing-floor servers can be moved to the Cloud, helping to reduce equipment as well as keeping systems up to date. With today’s standard IT security protocols, OT can rest assured that their SCADA system will not be compromised.
With IT’s strengths in standardization, organizations can leverage technologies such as SQL databases, Java, and SSL to quickly develop and deploy a solid, secure solution. The need for proprietary technology is a thing of the past.Organizations can monitor and control multiple systems without incurring high costs and being locked into a highly restrictive HMI/SCADA environment.
Challenges of OT-IT Alignment
The most pressing concern about integrating OT and IT is security. The reality is that the proliferation of sensors and other smart, connected devices has brought with it an increase in security vulnerabilities. OT and IT have historically had differing security needs although they have become more similar over time.
OT systems have used proprietary technologies that made them less likely to be targeted for attacks (i.e. security by obscurity). OT systems have also been fairly self-contained by only having a few connections to other systems. On the other hand, IT and enterprise systems are well-connected and frequently under attack, but have a higher level of acceptable security risk because IT usually has a higher tolerance for downtime. From an OT perspective, downtime could equate to millions in lost revenue, and thus, their tolerance for downtime is lower.
Another big challenge organizations face is return on investment (ROI). The research director at Gartner, Chet Geschickter, said, “the big challenge now is demonstrating return on investment. Executives need to validate the contribution that IoT can make in order to justify large-scale rollouts.”⁶ With IIoT being essentially a new market, industrial organizations must prove that IIoT is the most cost-effective solution to bring industrial data into the enterprise level.
Then there is the fact that edge-of-network devices tend to use different protocols for sending and receiving data, and there is the issue of interoperability: how do we make all of these different kinds of devices all connect to each other? Customers want to achieve a common infrastructure, and to do so requires laying down the groundwork to achieve a standardized communication protocol.
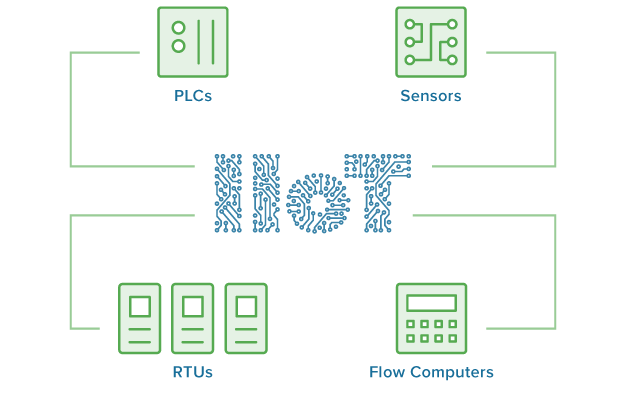
Should IIoT Be Built Top-Down or Ground-Up?
SCADA has already been doing many of the tasks associated with IIoT for years, even before the term came into use. For about 30 years now, industries like oil and gas, chemicals, pharmaceuticals, and manufacturing have used sensors to improve their processes. Those industries capture large amounts of data from PLCs and pass them to SCADA systems as real-time data, which is then stored and displayed, enabling improved decision-making. From this perspective, IIoT is not as much a new thing as it is a redefinition and an extension of what OT professionals are already doing.
Many of the players in the IIoT space today are IT professionals who do not necessarily understand the operational side. Even some IIoT alliances and consortia have put forth a notion that IIoT should be built using top-down, IT-driven methodologies. The problem is that if you try to put out an IT-centered, top-down IIoT solution that isn’t amenable to OT professionals, it simply will not succeed. IT professionals must prove operational excellence and security performance to an operations manager; otherwise, the project comes to a complete halt. This makes a strong case that OT should drive the implementation of IIoT, rather than IT.
To make IoT work in an industrial environment, the approach must be from the ground up. The IT side must recognize that top-down methodologies may not take into account the importance of stability and security, and the variety of protocols, in SCADA solutions. The OT side must recognize that IT has incredible potential to bring OT data into the enterprise. Since most of the needed data resides on the OT level, the ground-up approach is the best path to a fully functional IIoT solution that combines proven OT and IT technologies.
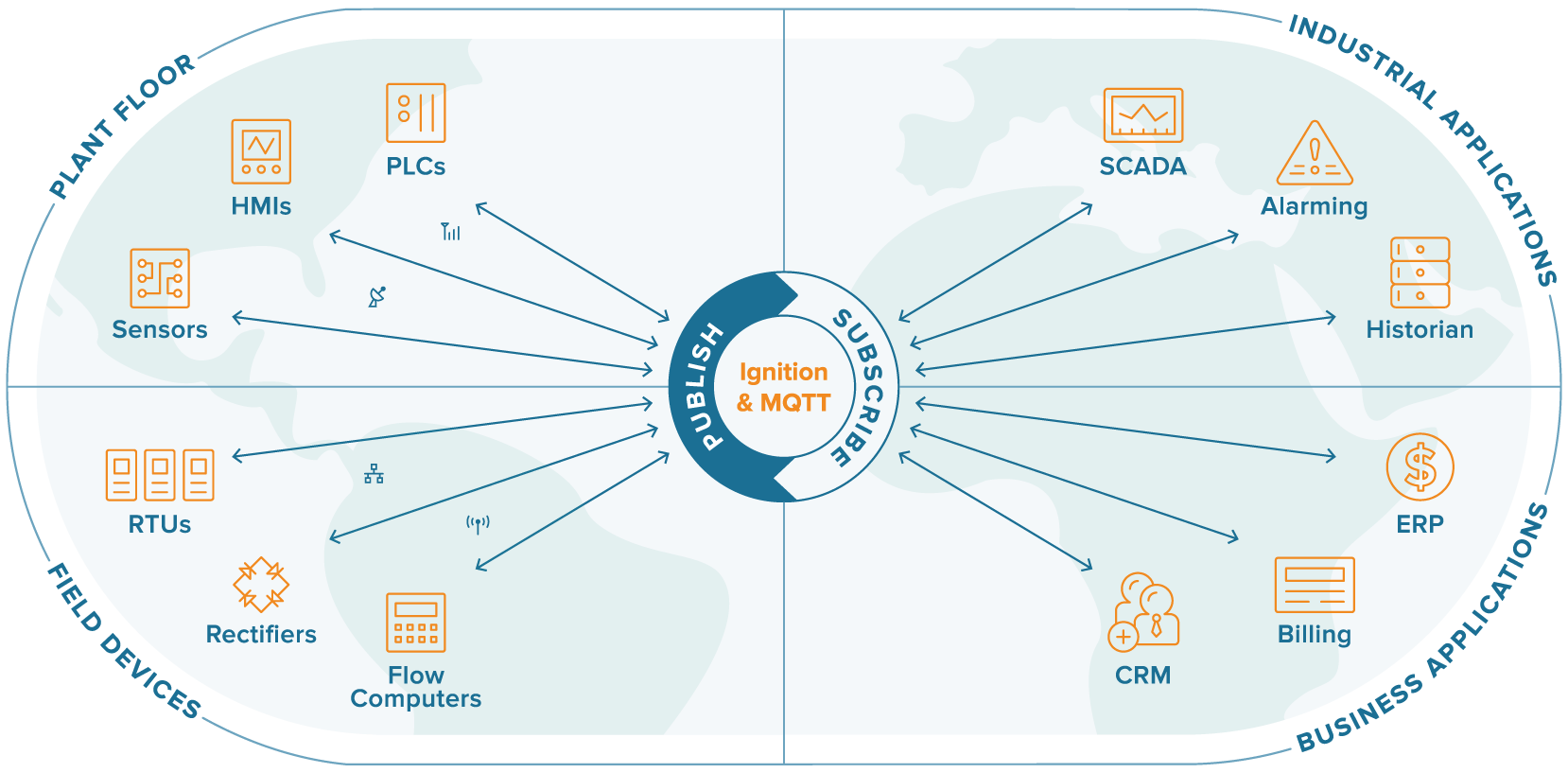
An IIoT solution that is not just a theoretical possibility but a concrete reality must be built on technologies that sit squarely at the intersection of OT and IT. There are two specific pieces of technology that are crucial for a true IIoT solution: a platform and a protocol.
Enabling IIoT: The Ideal Platform
With many so-called IIoT solutions coming to market, what features are necessary to truly deliver a solid IIoT platform? The IIoT requires the connection of many devices and systems to collect and share the vast amount of high-quality data across an industrial enterprise. It is vital that the IIoT platform be extraordinarily flexible, scalable, and equally capable in dealing with both OT and IT technologies.
Unlike most SCADA solutions, the ideal IIoT platform must exhibit extreme agility and flexibility — no proprietary solutions, no locked data, and no unneeded frustrations. The ideal IIoT platform must be able to adapt quickly to a wide range of industries and applications without hindering current enterprise infrastructures. Furthermore, it should be capable of making changes without interrupting current processes and workflow. Ready, set, connect, and data is available with just one click.
Scalability is an incredibly important feature of the ideal IIoT platform. As more systems and devices go live, the IIoT platform must be able to quickly accommodate the influx of data points, giving organizations the ability to share and analyze massive amounts of data in little time. The IIoT platform should also scale without any restrictions. Taking a page out of the IT playbook, the IIoT platform should offer unlimited licensing, allowing unlimited number of connections, tags, and user clients. The unlimited licensing allows for incredible scalability and results in significant cost savings.
The ideal IIoT platform should bring interoperability between OT and IT by communicating with most if not all industrial and enterprise systems and devices. The platform combines IT standards such as SQL, Python, and Java with OT standards such as OPC-UA and Modbus. By having a platform that can bridge the worlds of OT and IT, industrial enterprises are able to share data across an entire organization easily. The ideal IIoT platform can truly empower organizations to make better decisions more often by leveraging SQL and Java to collect data from PLCs, RTUs, and HMI/SCADA systems.
Enabling IIoT: The Ideal Protocol
Message Queueing Telemetry Transport (MQTT) has quickly emerged as the standard messaging protocol for industrial M2M applications. Developed in 1999 by Arlen Nipper, who is now president of Cirrus Link Solutions, and Dr. Andy Stanford-Clark of IBM, MQTT has become one of the most dominant IIoT message transport protocols.
MQTT was initially developed to suit the needs of the oil and gas industry. Oil and gas pipeline installations can cover several thousand miles in remote areas. A single installation may contain thousands of PLCs which connect to thousands of devices. Legacy communication protocols use a poll/response methodology which saturates communication channels with unchanged data, leading to network congestion. MQTT is a lightweight solution that makes the volume of usable data available in applications such as these. Other industries have also discovered the value of MQTT: it is now used in Facebook Messenger and Amazon IoT, and is both an ISO and OASIS standard.
The publish-subscribe methodology of MQTT creates a single, super-efficient data pipeline through which data is pushed from thousands of devices into a central location where it is accessed by industrial and business applications. MQTT maintains stateful sessions and is bi-directional. Its lightweight nature facilitates a higher throughput rate, which significantly increases the data monitored or controlled.
MQTT’s one-to-many capability enables the use of message-oriented middleware (MOM) technologies, which decouple edge-of-network devices and data-consuming client applications for more efficient information distribution and increased scalability. The decoupling of devices from applications is very significant from a development, information, and security standpoint.
Connecting intelligent devices into the infrastructure through MOM, rather than directly plugging them into applications, accomplishes three major things. First, it allows you to explore the possibilities of IIoT – to build new solutions on-the-fly and to go wherever the data takes you. Secondly, it allows you to bring in much more data much more quickly. Thirdly, it improves security by not directly exposing edge-of-network devices. Middleware helps to keep vulnerable devices such as PLCs out of reach.
The Optimal Solution
Unlike other IIoT solutions, Ignition IIoT has been built up from the OT level to connect up to the IT level.
Ignition offers a solid and secure industrial development platform for today’s data-intensive industrial applications.
Ignition includes features that make it singularly effective as a universal industrial automation platform for HMI, SCADA, IIoT, and MES. It has an unlimited licensing model, which allows unlimited tags, clients, and connections. Unlimited licensing allows solutions to grow along with an organization without restrictions and additional costs. Ignition offers cross-platform compatibility, and you can Web-launch it on desktop PCs or mobile devices. It features IT-standard technologies and scalable server-client architecture. It’s also modular, which means you configure Ignition’s capabilities by adding modules to it.
By adding the MQTT protocol to the inherent capabilities of the Ignition platform, you can decouple intelligent devices from applications in order to make data available to the entire enterprise.
Ignition IIoT is a real IIoT solution that can bridge the gaps between the enterprise level and the plant floor by converging OT and IT. It fills the fundamental need to access more data in order to make better decisions, faster.
1 “Gartner Says 6.4 Billion Connected ‘Things’ Will Be in Use in 2016, Up 30 Percent From 2015,” Gartner.com
2 “More Than 30 Billion Devices Will Wirelessly Connect to the Internet of Everything in 2020,” ABIresearch.com
3 “An Internet to Call Our Own,” Smart Industry Magazine
4 “Behind GE’s Vision for the Industrial Internet of Things,” Fast Company
5,6 “Gartner Survey Shows That 43 Percent of Organizations Are Using or Plan toImplement the Internet of Things in 2016,” Gartner.com
Want to stay up-to-date with us?
Sign up for our weekly News Feed.