ILS Automation Develops SFC & Diagnostic Toolkits
7 min video / 4 minute readProject Overview
Problem
Ignition applications in chemical plants and oil refineries (C&O) are unique from typical applications in several ways. First of all, C&O plants generally have a mature automation infrastructure that includes a distributed control systems (DCS) including operator consoles and a plant historian. Whereas many Ignition applications tend to serve these functions, in a C&O plant the Ignition application augments these systems. The other constant is that nothing is constant! There are many factors that are always changing in a chemical plant. From the raw feeds, to unit configuration, to product specifications, the demands of the control system need to evolve to keep pace with the environment. Consequently, a modern chemical plant needs a set of nimble tools that allow changes to the control and diagnostic regimen in a Rapid Application Development (RAD) environment. The applications that are developed need to support changes on the fly and support intuitive debugging and development interfaces. ILS has developed two modules that extend the power of Ignition in important ways for the chemical and oil and gas industries as well as any other industry that can benefit from such nimble application development tools.
Solution
The first module created with Ignition is the Diagnostic Toolkit. The diagnostic toolkit is used to detect and correct complex problems in a maintenance friendly framework. The diagnostic toolkit uses a block language to construct a schematic for detecting problems that are difficult to represent in the DCS and difficult to detect using standard DCS languages. The block language is based upon and extends the IEC 61131-3 specification for functional block diagrams but is tailored for supervisory, diagnostic applications. The schematics analyze real-time data coming from instruments in the field and from laboratory analysis. The culmination of a schematic is a diagnosis. A diagnosis represents a specific problem; for example, a specific characteristic of the product such as hardness being off-spec. But the Diagnostic Toolkit is more than just another alert system. Whereas detecting an abnormal condition is where most alert systems end, it is the beginning for the Diagnostic Toolkit.
The configuration of a diagnosis includes facilities for calculating recommendations for the setpoints that control the product characteristics. The recommendation calculation methods are written in Python using standard chemical engineering analysis of the process and the problem. The recommendations are fed into a recommendation engine that considers all of the active diagnosis and attempts to resolve the most important problems first. It automatically combines recommendations from multiple problems for the same setpoints and evaluates each recommendation against a set of output specific constraints such as maximum allowed change and maximum and minimum absolute limits.
The second module is the SFC+ Toolkit. This is built on top of IA’s implementation of the IEC 61331-3 Sequential Function Chart (SFC) module. SFC+ implements many of the ISA S88 guidelines for batch recipe control. The SFC+ module is used to implement automated startup, shutdown, and grade change procedures in a complex continuous process environment. The challenge in these three procedures is safety, quality, and efficiency. The faster that the unit can be safely started, stopped, and changed over, the less off-spec product will be produced, thus maximizing productivity and quality.
The SFC+ module takes advantage of the robust execution engine in IA’s SFC Module and adds a host of specialized advanced blocks for things like: reviewing a spreadsheet of timed setpoint changes; confirming that all of the necessary controllers are in an appropriate mode to accept setpoint writes; and monitoring the instrument value associated with a setpoint to make sure that the control action was effective. The SFC+ module also expands the use of chart data into the broader notion of recipe data. It provides additional built in types of recipe data and includes facilities for passing recipe data efficiently that are robust to changes in chart structure. Finally, the SFC+ module provides important capabilities to troubleshoot, test, and develop recipes. The call tree utility shows a graphical call tree of charts. The recipes used in a typical plant contain several hundred charts and may be 15 levels deep. Being able to visualize this call tree is critical. Another important capability enables development and testing to be performed on the production system without affecting the actual production facility. ILS has developed an “isolation mode” whereby a chart (or diagnostic diagram) can be placed in isolation mode whereby all of the tag references will automatically be switched to a shadow provider and all database calls will automatically be switched to a development database. This allows a chart within a recipe of a hundred charts to be analyzed, changed, and tested in a rapid manner.
Result
With the Ignition modules in place, this project demonstrates that Ignition can play an important role in the operation of chemical plants and oil refineries, and these toolkits provide inexpensive, powerful alternatives to the tools provided by large DCS vendors.
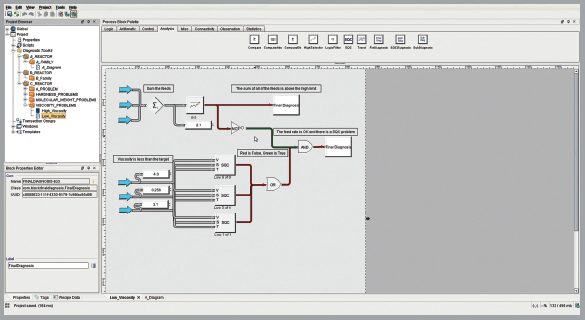
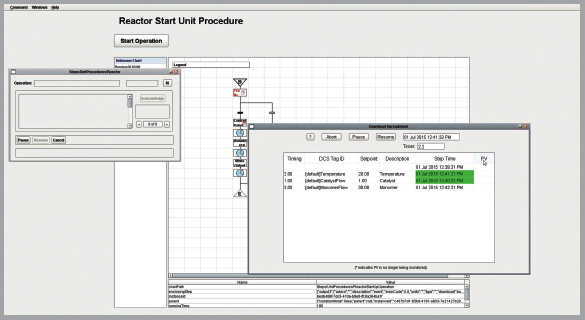
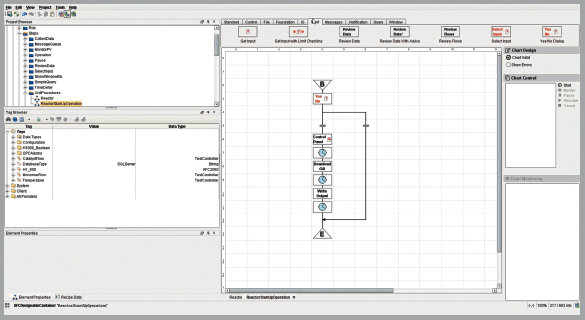
Project Information
Created By: ILS Automation
ILS Automation provides automation solutions for process industries including chemical, refining, and biotechnology. The founders of ILS have a background in real-time, rule-based systems for a wide variety of industries including: laboratory, batch, process, manufacturing, and business applications. ILS also specializes in integrating laboratory and hardware control systems with SCADA software and databases. ILS provides complete lifecycle development and support of Ignition SCADA applications, including custom modules. ILS products and services also include control panel fabrication and electrical design which includes the AFC line of hardware controllers for cell-culture and fermentation processes.
Project For: ExxonMobil
Exxon Mobil Corp. (ExxonMobil) is an American multinational oil and gas corporation headquartered in Irving, Texas. It is the largest direct descendant of John D. Rockefeller’s Standard Oil Company, and was formed on November 30, 1999, by the merger of Exxon (originally the Standard Oil Company of New Jersey) and Mobil (originally the Standard Oil Company of New York).
Want to stay up-to-date with us?
Sign up for our weekly News Feed.