Inductive Automation Blog
Connecting you to ideas, tips, updates and thought-leadership
from Inductive Automation
Behind The Scenes Of Ignition’s Public Demo
Chris Fischer
Wed, 08/28/2024 - 12:07
In this first installment of Power Hour, Application Engineering Managers from Inductive Automation will share the inner workings of how IA built the Ignition public demo, offering expert development strategies and tips and tricks for Ignition Perspective along the way.
Hero
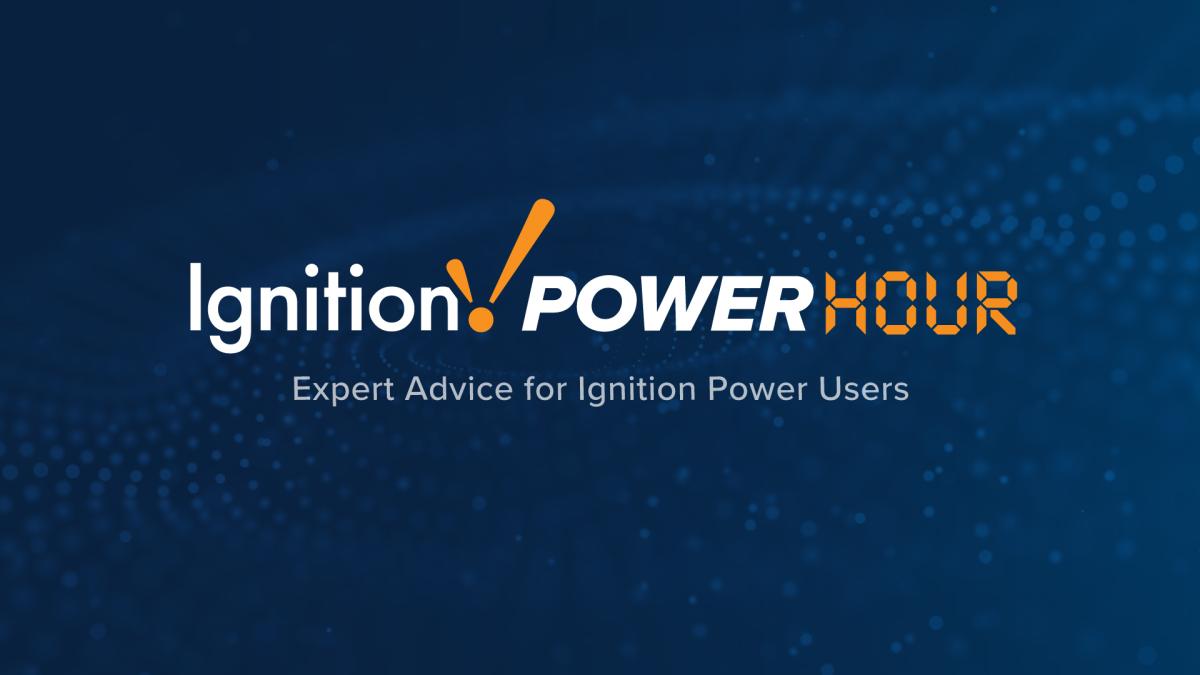
Integrator Program Level
Thumbnail
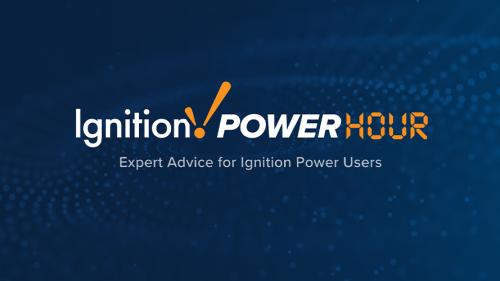
Wistia ID
lsw9ldiq1a
Topic
Featured at Location
Learning Series
Coffee with Kevin & Tea with Travis
Device Simulation
Learn about your options for device simulation, including the new simulator in Ignition, SFCs, and connecting to emulated PLCs. As always, this is also an open Q&A, where we can also discuss any other Ignition related topics.
Locked